Уникальная работа: как на «Атомэнергомаше» делали реакторы для РИТМ-200
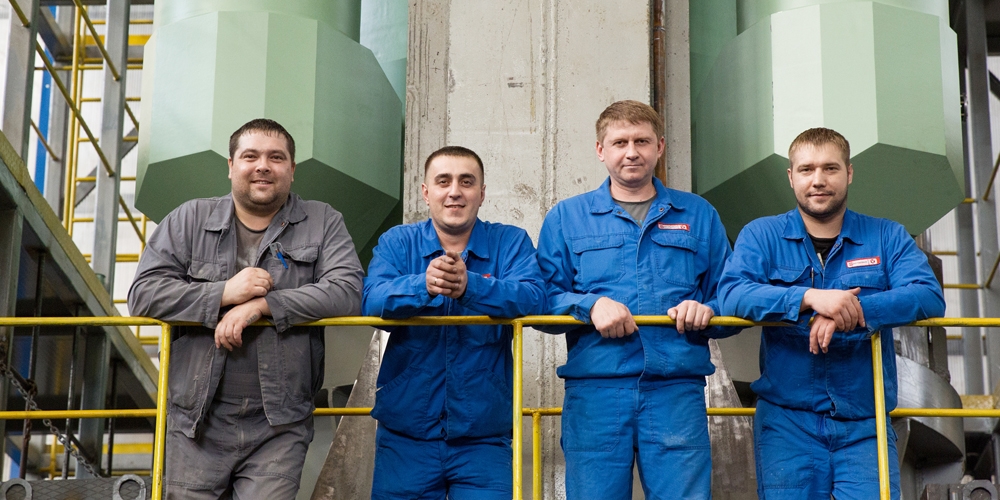
С интервалом в месяц «ЗиО-Подольск» отгрузил на Балтийский завод два уникальных реактора установки РИТМ-200 для ледокола нового поколения «Арктика». Сотрудники ЗиО, ОКБМ им. Африкантова, «ЦНИИТмаша» и «Энергомашспецстали» работали в единой команде и справились за два года и четыре месяца — рекордный для такой задачи срок.
Первым делом наладили взаимодействие между коллективами: технологами, конструкторами, снабженцами, исполнителями, логистами. Мастеров, сварщиков, слесарей отправили в центры профподготовки. РИТМ-200 — принципиально новая продукция для ЗиО, поэтому нужно было разработать технологические процессы, методики изготовления оборудования, приобрести новые станки и материалы. «Например, требовалось освоить новую технологию алитирования. Это насыщение поверхностного слоя металла компонентами, которые в течение эксплуатации реактора предотвращают скипание крепежных элементов с корпусом изделия,— объясняет Алексей Стрюков.— Мы освоили технологию и создали на заводе участок под нее».
Космическая точность
Изготовление корпусного оборудования реактора началось с антикоррозионной наплавки для защиты от разрушающего воздействия воды и высокой температуры. Для этого завод
модернизировал девять установок наплавки под внутренний диаметр труб. Всего на разные элементы каждого корпуса было наплавлено около 10 т антикоррозионной ленты. Работы продолжались восемь месяцев.
Дальше собирали части корпуса и сваривали по разработанной специалистами «ЗиО-Подольска» технологии. Первый основной шов, кольцевой, толщиной 150 мм, соединил фланец и обечайку. Второй — обечайку и днище. Третий, замыкающий,— половинки реактора. Каждый шов безостановочно варили пять — семь суток. «Днем и ночью, без перерыва на обед и без выходных. Смена была по шесть часов, потому что дольше человеку не выдержать,— рассказывает Алексей Стрюков.— Условия очень тяжелые: постоянно включенные горелки не только выжигают кислород, но и раскаляют участок корпуса, на котором работает сварщик».
АЛЕКСЕЙ СТРЮКОВ:
«СКЛАДЫВАЛОСЬ
ОЩУЩЕНИЕ, БУДТО
РАБОТАЕТ КОЛЛЕКТИВ
ОДНОГО ПРЕДПРИЯТИЯ,
ХОТЯ БЫЛИ ТАМ И ПРЕД-
СТАВИТЕЛИ ОКБМ,
«ЦНИИТМАША», «ПРОМЕ-
ТЕЯ» И ДР.»
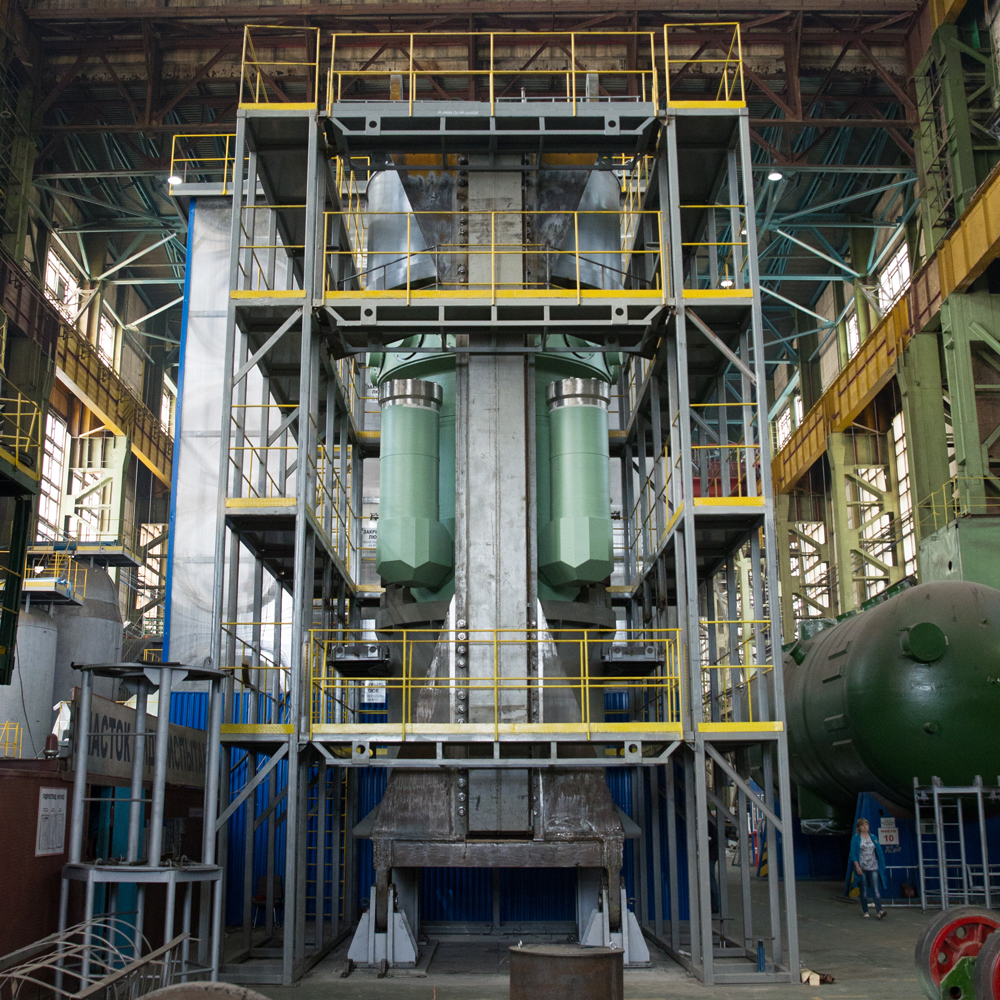
Масса интегрированного
корпуса — 146 т
Цикл изготовления —
28 месяцев
Гидроиспытания под дав-
лением 270 атмосфер (как
на глубине 2,7 тыс. м)
Габариты парогене-
рирующего блока —
3,5×4,5×11,6 м
Масса в пределах защит-
ной оболочки — 2,2 тыс. т
Срок службы — 40 лет
Так как корпус интегрированный, в нем расположены гидрокамеры для установки насосов. И приварка четырех гидрокамер — а каждая весит 4,5 т — стала следующим технологическим вызовом. Сложность в том, что сварка изделий большого диаметра, 830 мм, проводилась в неповоротном положении, чтобы отклонение горизонта не превышало 0,1 мм. Такой метод применяется в особых случаях, когда изделие невозможно кантовать, а доступ к шву затруднен. При этом шов должен завариваться с первого раза без дефектов. По словам Алексея Стрюкова, на тот момент всего шесть сварщиков в России имели подобный опыт — и все они работали на Балтийском заводе. На «ЗиО-Подольске» решили выучить своих мастеров. «16 сварщиков прошли техническую и психологическую подготовку. Ребята опытнейшие, причем как молодые, так и постарше,— отмечает Алексей Стрюков.— Они прониклись, почувствовали себя членами команды, где один за всех и все за одного».
На ЗиО поставили цель заварить неповоротный кольцевой шов быстрее, чем на Балтийском заводе,— за 22 дня вместо 45. «Решили, что после каждого прохода будем контролировать качество шва. Увеличим время на контроль, но уменьшим вероятность дефекта»,— поясняет руководитель проекта. Одновременно на площадке работали 56 человек. Шеф-надзор технологов, сотрудников технического контроля и других специалистов был круглосуточный. Добавим, что на втором корпусе реактора для РИТМ-200 справились еще быстрее — за 19 дней. Набили руку.
ПСР: польза следующим реакторам
Алексей Стрюков признается: «Пошаговый график я разработал интуитивно, понимая все сложности технологических операций. В июле прошлого года он был утвержден. С датой
отгрузки я ошибся буквально на три дня». После того как график утвердили, была создана рабочая группа. Лучшие умы трех предприятий — «ЦНИИТмаша», ОКБМ и ЗиО — пересмотрели конструкторскую и технологическую документацию и выявили узкие места. Конструкторы рассматривали все предложения и при необходимости корректировали документацию.
Начальник производства оборудования ОИАЭ, ГНХ и судостроения Сергей Голомысов и начальник отдела по развитию производственной системы Николай Гаркуша с «ЗиО-Подольска» представили совместный проект сокращения сроков протекания процессов при изготовлении корпуса гидрокамеры со 110 до 90 дней. «Применили на 40% поверхности в коленьях и патрубках автоматическую сварку антикоррозионной ленты, а раньше везде наплавляли вручную. Плюс проработали использование электродов диаметром 5 мм вместо 4 мм — с ними наплавка идет быстрее»,— рассказывает Николай Гаркуша.
Круглосуточный дозор
Итак, с началом сварки замыкающего шва корпуса работа шла круглосуточно, без выходных и праздников. Алексей Стрюков вспоминает: «Складывалось ощущение, будто работает коллектив одного предприятия, хотя были там и представители ОКБМ, «ЦНИИТмаша», «Прометея» и др. Перед отгрузкой первого реактора, в конце мая, я три дня дома не был. Руководители направлений, точно так же, как и я, не уходили с завода сутками и спали буквально по дватри часа».
Тех, кто сомневался в успехе,— а таких было немало, Алексей Стрюков в команду проекта не брал. «Если ты понимаешь документацию, знаешь потенциал своих сотрудников и веришь, что цель достижима, все получится,— поясняет он.— Я буквально через день слышал «это невозможно сделать». Тем не менее сделали».
Самое сложное уже позади. На «ЗиО-Подольске» создано новое направление производства. Сейчас на предприятии идет сборка корпуса первого реактора силовой установки РИТМ-200 для атомного ледокола «Сибирь».
Справка
РИТМ-200 включает два реактора тепловой мощностью 175 МВт каждый и входит в состав главной ядерной энергетической установки ледокола. РИТМ-200 имеет уникальную энергоэффективную интегральную компоновку: основное оборудование размещено в корпусе парогенерирующего блока. За счет этого РУ в два раза легче, в полтора раза компактнее (соответственно, дешевле), мощнее установок КЛТ тепловой мощностью 140–150 МВт, использующихся сейчас ледокольным флотом. Активная зона — кассетного типа с низким обогащением урана-235. Перезагрузка топлива — раз в семь лет. Для примера: за это время дизельному ледоколу пришлось бы потратить 540 тыс. т арктического дизельного топлива.