В СНИИП внедрили систему штрихкодирования
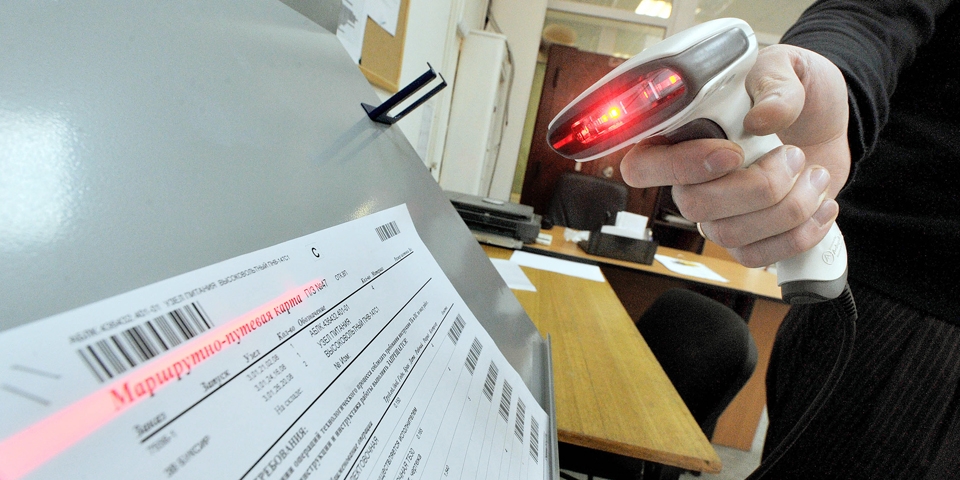
СНИИП, сканер для штрихкодирования
Когда начальник механического участка СНИИП Роман Филатов лично столкнулся с монотонной работой диспетчера по заполнению журналов, он понял: автоматизация производственных процессов не дань моде, а необходимость. Он стал инициатором внедрения системы штрихкодирования. Каких результатов удалось добиться и где еще используют штрихкоды, узнала «СР».
В прошлом году в СНИИП началась программа комплексной автоматизации управления жизненным циклом изделия. Многие операции в цехах требовали ручной обработки, из-за чего информацию о состоянии заказов на производстве невозможно было оперативно получить. Задержка достигала двух дней. Одним из узких мест была рутинная работа диспетчера, который сначала обходил все цеха, собирал отчетные журналы, а потом в течение дня вручную переносил их в электронную базу.
«Самому довелось столкнуться с этим, когда подменял старшего диспетчера. В день выходило до 500 операций. Так мучился две недели, пока в голове не созрел план, как облегчить этот труд. Все оказалось просто: на маршрутных картах изделий достаточно было разместить штрихкод соответствующих операций», — вспоминает Роман Филатов. Маршрутные карты – это паспорт детали с ее параметрами и операциями при изготовлении. Плюс записан маршрут движения заготовки по участкам цеха, где проставляются отметки о выполнении каждой операции: шлифование, сверление, сборка и так далее.
Диспетчерскую базу данных разрабатывали в самом СНИИП, поэтому программистам не составило никакого труда ее оперативно достроить. «Вместе с ИТ-отделом разработали образец новой маршрутной карты со штрихкодами. Посты ОТК оснастили стойками регистрации и сканерами», — поясняет Роман Филатов.
Решение было очень удачным, реализацию взял под контроль гендиректор — это стало его личным ПСР-проектом. «Пока штрихкодирование используем на этапе контроля, по факту выполнения какой-либо операции. Дальше больше, — обещает Роман Филатов, — охватим всю технологическую цепочку, от приемки материалов до отгрузки готовой продукции. И местонахождение заготовок можно будет узнать с точностью до станка».
В режиме реального времени
Системы штрихкодирования хорошо известны всем. Достаточно вспомнить, как в супермаркетах кассиры считывают сканерами штрихкоды,содержащие название товара и цену. В СНИИП сотрудник прикладывает к аппарату свой пропуск, сканирует штрихкод из маршрутной карты, и система мгновенно определяет номер заказа, наименование детали и характер операции. Обладая такой информацией, можно в реальном времени управлять производственным потоком и прибегать к детальному планированию. «Данные сразу попадают в электронную базу автоматической системы технологической подготовки производства и документации — АСТППиД. За счет синхронизации у старшего диспетчера освобождается до шести часов в день. Скорость получения данных за первые полгода +использования системы повысилась в семь раз», — приводит результаты Роман Филатов.
До этого неминуемо включался человеческий фактор, и возникала вероятность ошибки. Представьте: сначала контролер проверяет качество работы, делает отметку в маршрутной карте, регистрирует выполнение операции в журнале, потом журналы забирает диспетчер, чтобы ввести данные в систему. Диспетчер часто не мог разобрать, что написано, добавляет начальник участка. Теперь нет ни проблем с плохим почерком, ни лишних перемещений по цехам — контролер только ставит в карте отметку о выполнении и сканирует штрихкод операции. А в конце дня готов сводный документ, который подписывается и подшивается к отчетному журналу. «В любой момент можно посмотреть текущее состояние по отдельной детали, цеху или всему производству, — доволен Роман Филатов. — Раньше такая информация появлялась либо на следующий день, либо через день».
Аналогичную программу можно было бы купить, но, как правило, она идет в составе крупных MES-систем (от англ. manufacturing execution system,система управления производственными процессами), а это намного дороже. «К тому же не факт, что там учтены все особенности нашего производственного процесса, — уточняет Роман Филатов. — Значит, надо дорабатывать, а это дополнительные траты».
Штрихкодирование — набор графических изображений, буквенных и цифровых символов, которые визуально представляют собой пробелы и черные штрихи. Кодировка такого типа включает уникальный номер товара или изделия, а также любую введенную информацию. На производстве обеспечивает сквозное отслеживание изделия на любом этапе изготовления в режиме реального времени без необходимости обращения к бумажной документации.
Штрих в помощь
Похожие системы есть еще на двух предприятиях машиностроительного дивизиона — «Петрозаводскмаше» и «Атоммаше». На ПЗМ с помощью QR-кодов провели инвентаризацию незавершенного производства, маркировали все заготовки и настроили информационную систему «1С: УПП». На «Атоммаше» маркировали более 4,5 тыс. объектов основных средств и настроили выходные формы в учетной системе SAP ERP. В прошлом году обменялись отработанными решениями: на «Атоммаше» маркируют полуфабрикаты (пока только на участке изготовления днищ), а на ПЗМ — инвентаризируют основные средства. На ПЗМ учет ведется при помощи планшетов, для них сделали специальное мобильное приложение. На «Атоммаше» — мобильные терминалы.
«Как и любая информационная система, штрихкодирование помогает сотрудникам, но не выполняет обязанности за них», — комментирует директор по ИТ «Атоммаша» Олег Апанасик. Штрихкодирование не заменяет такие ПСР-инструменты, как сопроводительные листы и доски производственного контроля, а просто дополняет их. «Важно, чтобы производственники сначала научились работать с инструментами ПСР, и только после того, как мы поймем, что информации в мобильном приложении достаточно и производственный персонал корректно и своевременно заводит данные, можно будет говорить о тиражировании системы на другие участки», — говорит Олег Апанасик.
QR-код, в котором зашифрован номер производственного заказа и информация о технологических операциях, распечатывается до первой операции и наклеивается на заготовку. «Когдадетали собираются в узлы, наклейки заменяют новой, соответствующей сборочной единице», — объясняет директор по ИТ «АЭМ-технологий» Антон Думин.
На ПЗМ штрихкодирование повысило достоверность учета незавершенного производства и сократило время сплошной инвентаризации основных средств в четыре раза — с месяца до недели. «Про результаты на «Атоммаше» пока говорить рано, так
как запуск системы в промышленную эксплуатацию состоялся совсем недавно, — отмечает Олег Апанасик. — Наша ключевая задача на этот год — повышение точности выдаваемых на участки планов».