Недостающее звено: концентраты РЗМ скоро начнут разделять в России
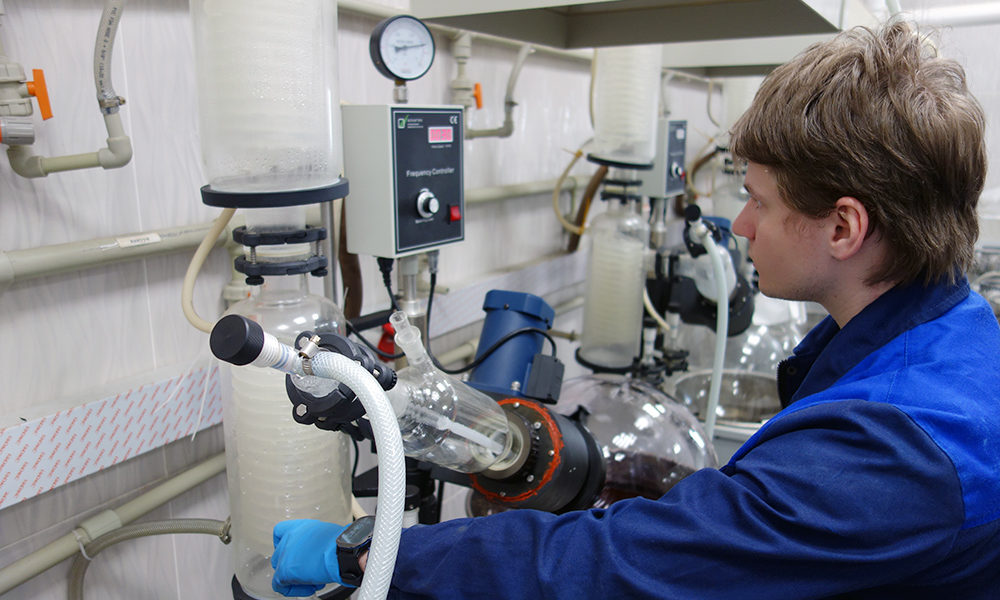
Электронике, приборо- и машиностроению, атомной, металлургической и прочим отраслям требуются редкоземельные металлы (РЗМ). В России добывают руду и производят коллективный концентрат — но не индивидуальные соединения. Чтобы получать их, нужно специализированное предприятие. Горнорудный дивизион «Росатома» и группа компаний «Русредмет» построили опытную разделительную установку и готовят проект большого производства. Подробности — в интервью с гендиректором «Русредмета» Андреем Нечаевым.
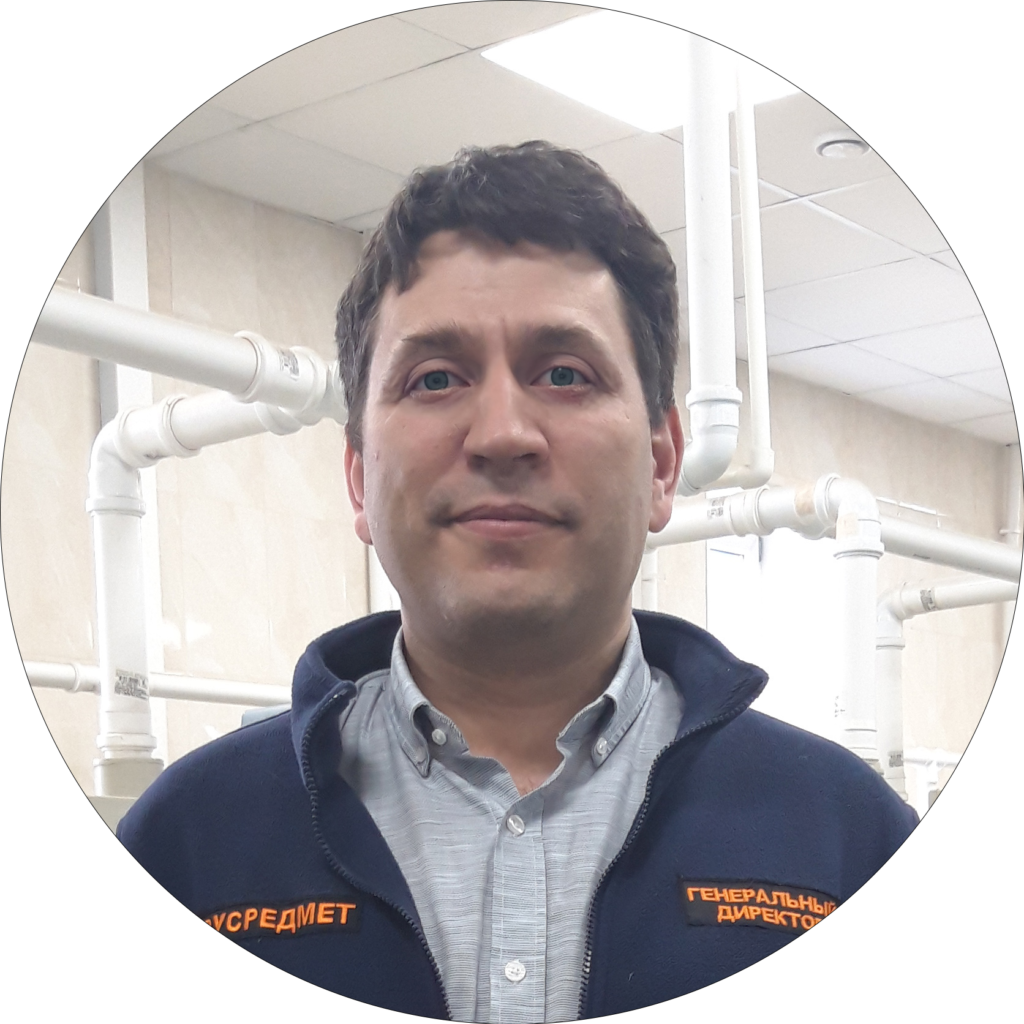
— Расскажите о предыстории проекта.
— В Советском Союзе были производства, где разделяли редкоземельные элементы, но после распада СССР они оказались в других странах. В России содержащий РЗМ лопарит добывает Ловозерский горно-обогатительный комбинат в Мурманской области. Лопаритовый концентрат оттуда отправляется на Соликамский магниевый завод. Там извлекают ниобий, тантал и титан, а также получают коллективный концентрат РЗМ, который пока экспортируют, потому что у нас разделять негде.
Но ситуация меняется. По договору с горнорудным дивизионом «Росатома» мы разработали технологию, чтобы извлекать лантан, церий, неодим, празеодим и концентрат среднетяжелой группы РЗМ, содержащий самарий, европий и гадолиний. После запуска производства в нашей стране будет весь первичный передел: добыча, обогащение, получение коллективных концентратов и индивидуальных соединений. Это надежная база для следующих переделов высокотехнологичных отраслей, которые развиваются в том числе в контуре «Росатома».
— Какую технологию разделения вы взяли?
— Мы применили известную азотнокислую технологию: перед разделением карбонаты растворяют в азотной кислоте и получают нитраты. Мы сравнивали нитратную схему с хлоридной и пришли к выводу, что для того состава элементов, который нам надо извлечь, нитратная подходит больше. В хлоридной схеме концентрация полезных компонентов — на уровне 80–100 г/л, в нитратной — 350–370 г/л. То есть при переработке 1 тыс. т карбонатов соляной кислотой в литр раствора переходит 100 г, азотной — 370 г, а количество полезного компонента в растворе влияет на объем реагентов и проч. По себестоимости схемы сопоставимы.
— Экономику считали?
— Экономическую модель просчитывает заказчик на основе наших данных. Часть работы состоит в том, чтобы оптимизировать расходные коэффициенты — удельные затраты реагентов и материалов на единицу продукции.
— Насколько просто масштабировать опытную установку до промышленной?
— Экстракция — очень благодарный процесс. Мы с литров в час переходили на 20, 30 и 50 м3 в час, и все показатели подтверждались, все работало. Стадия научно-исследовательских работ закончилась.
— Что в нее входило?
— Мы полностью разработали и проверили технологию, провели статические испытания, перепроверили данные из технической литературы, выполнили расчеты, создали идею установки и согласовали ее. Сошлись на том, что нужны не отдельные этапы производства, а сразу мини-модель завода, чтобы получать четыре легких РЗМ и группу среднетяжелых. Мы смонтировали шесть экстракционных каскадов. Каскады непрерывно отработали несколько тысяч часов. Это позволило не только расчетно, но и эмпирически сбалансировать все материальные потоки: сырье, реагенты, оборотные потоки, отходы, основные и побочные продукты, чтобы минимизировать или вовсе исключить ошибки на большом производстве. Полученные данные стали исходными для проектирования основных технических решений, на которых будет базироваться расчет капитальных затрат.
— На какой стадии вы сейчас?
— Выбираем основные технические решения и определяем проектировщика, начинаем проектирование промышленного объекта. Мы утвердили аппаратурно-технологическую схему, предварительные компоновочные решения для заданной производительности, оборудование, запросили коммерческие предложения. Уже понятно, что цех для разделительного комплекса должен представлять собой трехэтажное здание с площадью этажа 13,2 тыс. м2. Отработка технологии на мини-модели позволит сэкономить время и, соответственно, средства, которые будут потрачены не на отладку, а на выпуск продукции, быстрее начнется возврат инвестиций.
— На все это вам потребовалось меньше двух лет. Как удалось так быстро справиться?
— Во-первых, помогла преемственность — у нас работают сотрудники, которые начинали на советских заводах и оттуда принесли знания. Во-вторых, «Русредмет» сам накопил достаточно большой опыт в разделении РЗМ. У нас не было комплексных работ по разделению всей легкой группы, но отдельные задачи мы решали. Например, создали технологию переработки железоборнеодимовых магнитов с получением неодима. Для других компаний на других сырьевых источниках отрабатывали и хлоридную, и нитратную схемы разделения.
— Вы получили первую продукцию. Потенциальные клиенты ее опробовали?
— Да, это главное. Мы отправили предприятиям «Росатома» и другим российским потребителям неодим, празеодим и прочие РЗМ. Они по всем параметрам подошли.
— По проекту в промышленную установку, которую построят на Соликамском магниевом заводе, будет подаваться около 2,5 тыс. т коллективных карбонатов в год. А сколько продукции будет на выходе?
— Практически столько же — минус 1–3 %. 50 % продукции на выходе — церий, 25 % — лантан. Это общемировая проблема: чтобы получить нужное количество неодима и празеодима, надо извлечь очень много лантана и церия. Неодима и празеодима у нас 13–18 %, остальное — среднетяжелая группа.
— Планируете ее делить?
— Да, тут хлоридной технологии уже альтернативы нет. Это следующий этап.
— Где используют элементы среднетяжелой группы?
— Самарий — в самарийкобальтовых магнитах. Европий — в производстве мониторов и электроники. Гадолиний нужен как добавка в постоянные магниты для охлаждения, он также используется в атомной отрасли.