Трубное дело: на «Атоммаше» впервые изготовили модуль трубных систем
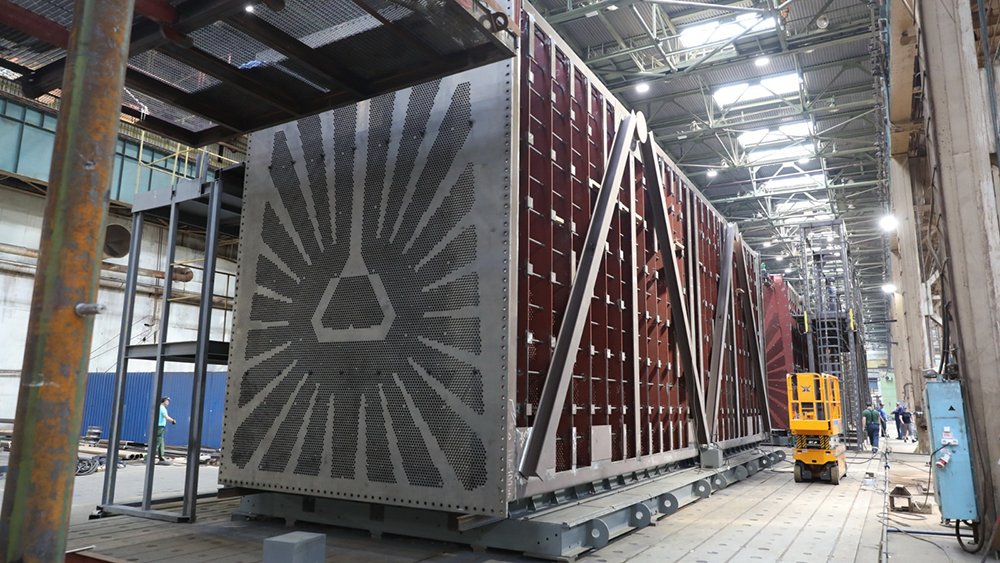
По титановым трубкам модуля трубных систем прокачивают морскую воду для охлаждения и конденсации пара, прошедшего через турбину. Оборудование установят в машинном зале второго энергоблока АЭС «Аккую». Установка способна выдержать подземные толчки интенсивностью до 8 баллов по шкале MSK‑64 — для станции в Турции, только что пережившей землетрясение, это важный показатель.
Нетривиальная задача
Подготовку к производству модуля трубных систем (МТС) на «Атоммаше» начали в 2021 году: создали новый участок в производственном корпусе № 4, освоили технологию сварки титана и развальцовки трубок в трубных досках (деформирование трубы в отверстии трубной доски для создания герметичного соединения). Для проверки на герметичность изготовленного модуля разработали новое оборудование и технологию контроля изделия.
«Эта задача активизировала нас, инженеров. Когда работаешь с привычными заказами, сложности редко возникают. Нетривиальные задачи заставляют мозг работать иначе. Мы знали, что справимся, но каким будет путь до финиша, никто не мог предсказать», — отмечает ведущий инженер-конструктор Валерий Старшинов.
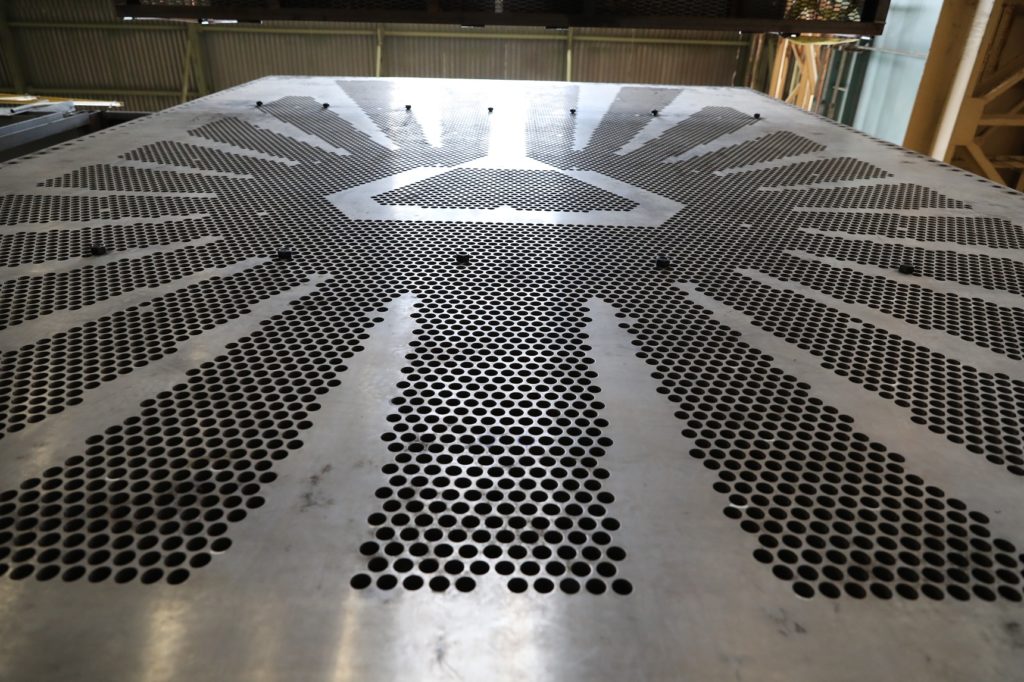
800 швов в день
Конструкцию собирали на стапеле. Сначала подготовили каркас, состоящий из стальных балок и перегородок, испещренных круглыми отверстиями. По торцам установили трубные решетки из биметалла — композитного материала из слоев стали и титана. Затем в каркас поместили теплообменные титановые трубы толщиной всего 0,5–0,7 мм. На заводе отмечают, что это был их первый и успешный опыт работы со столь тонкими изделиями. Обычно в парогенераторах «Атоммаша» установлены теплообменные трубки из нержавеющей стали толщиной в три раза больше — 1,5 мм. Но коррозионная стойкость титана выше, чем у нержавейки.
Габариты МТС впечатляют: длина — 16 м, высота — 6 м, ширина — 4 м. Вес — 125 т. Срок службы оборудования — 60 лет, при этом модуль может выдержать подземные толчки интенсивностью до 8 баллов.
«Перед сварщиками стояла ответственная задача — развальцевать и приварить к решеткам эти тонкие титановые трубки — более 28 тыс. мест сварки, — рассказывает ведущий инженер-конструктор Владимир Толочный. — Специалисты использовали метод орбитальной сварки: в каждое отверстие вручную вставляли аппарат, который автоматически выполняет сварной шов по кругу (по орбите). Одновременно использовали четыре таких аппарата. За смену сварщики выполняли около 800 сварных швов».
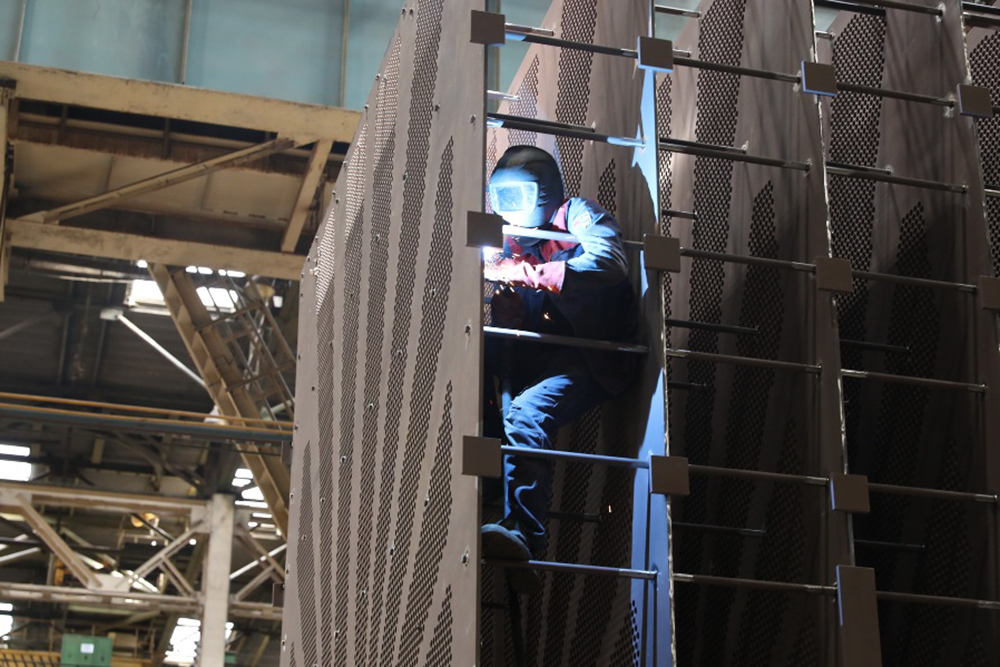
14 тысяч трубок
Готовый модуль должен пройти испытания на герметичность каждой трубки и каждого сварного шва. «Из-за санкций мы столкнулись с трудностями при закупке импортного оборудования для контроля герметичности. Но справились: в сжатые сроки разработали и изготовили свое устройство для контрольных операций. Российских аналогов у него нет», — говорит Валерий Старшинов.
Изобретение специалистов «Атоммаша» внешне напоминает пистолет. Оно создает вакуум внутри каждой теплообменной трубки, используя энергию сжатого воздуха. Если вакуум сохраняется 15 секунд — значит, трубка или сварной шов герметичны. Несмотря на высокую скорость проверки, процесс испытаний занял четверо суток — нужно было проверить более 14 тыс. трубок.
Еще один способ подтвердить прочность и герметичность модуля — гидравлические испытания. Готовиться к ним начали еще во время сборки МТС: создали специальный стенд и необходимую к нему оснастку. Модуль трубных систем под наклоном поместили на опоры, установили массивные заглушки размером 4 × 6 м, зафиксировав каждую с помощью 200 шпилек. После этого изделие около шести часов наполняли подготовленной очищенной и обессоленной водой, насосами постепенно нагнетали давление до максимальных 7,5 атмосферы и выдерживали его в течение часа. На поверхности труб не появилось ни капли — первые испытания прошли на отлично.
В 2023 году на «Атоммаше» планируют собрать второй и третий комплекты МТС для АЭС «Аккую».
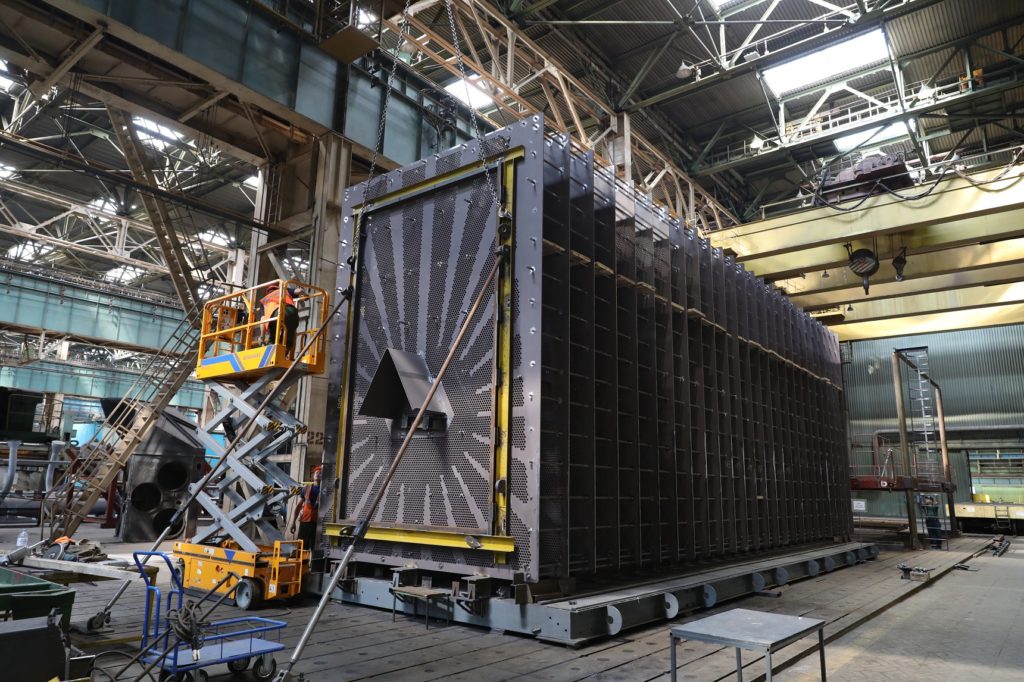