«Росатом» запустил первый завод по производству композитных ветролопастей
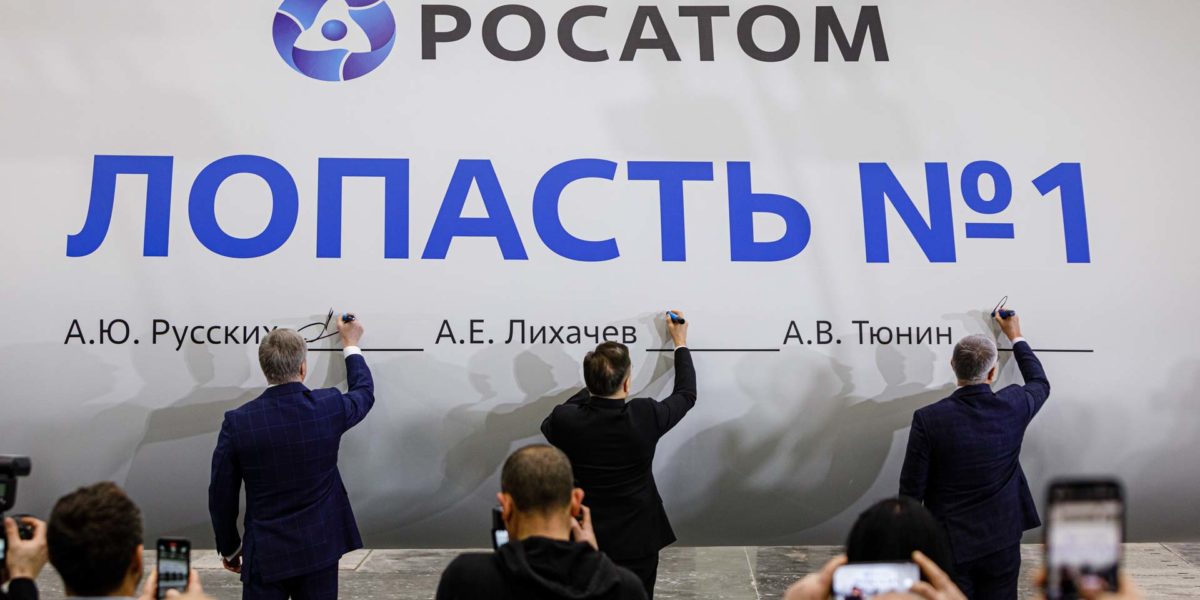
26 декабря 2024 года компания «Русатом Ветролопасти» открыла в Ульяновске завод по производству композитных лопастей. Ветроэнергетический дивизион «Росатома» будет использовать их для строительства ветропарков в России, а в перспективе и за рубежом.
Предыстория
До весны 2022 года ветропарки в России строили две компании: финская Fortum и российская «Новавинд» (недавно переименована в «Росатом Возобновляемая энергия»). Лопасти длиной 62 м для Fortum изготавливали на предприятии датской Vestas в Ульяновске. Лопасти длиной 49 м для «Новавинда» производила в Индии датская LM.
Когда в 2022 году западные компании начали массово сворачивать у нас бизнес, Vestas ушла. «Мы сделали все, чтобы закрытие «Вестас Мэньюфэкчуринг Рус» прошло в интересах России, а не акционеров, — вспоминает бывший гендиректор ульяновского завода, сейчас руководитель компании «Русатом Ветролопасти» Сергей Федченко. — Мы добились поэтапного увольнения сотрудников с выплатой более высоких, чем предполагалось, компенсаций. Закрытие означало и расторжение специального инвестконтракта, поэтому все налоговые льготы были отменены, а деньги возвращены в бюджет». Vestas перевезла оборудование на склад и ликвидировала юрлицо. В том же году композитный дивизион «Росатома» решил открыть свое производство лопастей (LM прекратила поставки в Россию) и пригласил Сергея Федченко возглавить новый завод.
Площадка «Вестас Мэньюфэкчуринг Рус» идеально подходила по параметрам и была свободна. 15 июня 2023 года создали юрлицо, в тот же день на работу приняли топ-менеджеров по ключевым направлениям: кадры, технология, производство, логистика, качество, финансы. За год и четыре месяца команда нашла поставщиков оборудования и сырья, проработала все вопросы по изготовлению и снабжению. В январе 2024 года сделали на площадке вендоров тестовую лопасть, проверив работоспособность оборудования. Ее отправили в сертификационный центр на комплексные испытания по международным стандартам. В декабре испытания завершились. Сырье и оборудование начали привозить в Ульяновск в июне 2024 года, в октябре производство запустили.
«В композитном дивизионе это уже 17‑й завод, и его запуск означает переход к производству крупногабаритной продукции», — отметил на церемонии открытия гендиректор «Росатома» Алексей Лихачев.
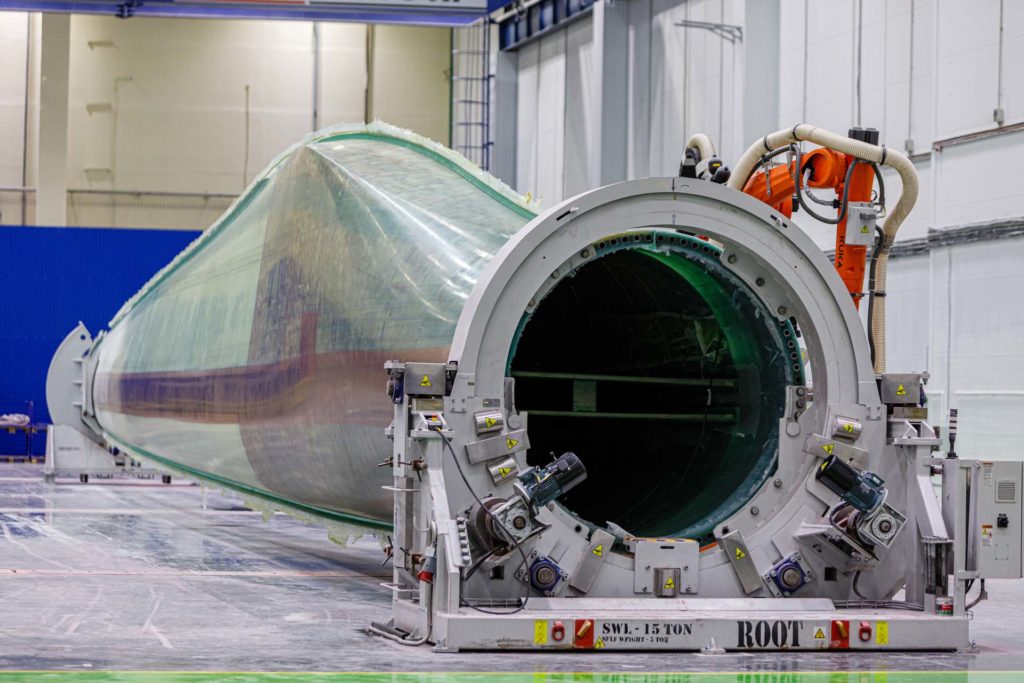
Место силы ветра
Три лопасти из первой партии отгрузили заказчику «Росатом Возобновляемая энергия» для испытаний на Кочубеевской ВЭС. Одну оставили для торжественного открытия — на ней расписались Алексей Лихачев, губернатор Ульяновской области Алексей Русских и глава композитного дивизиона Александр Тюнин.
«С производством ветролопастей мы сможем удовлетворить потребности наших ветроэнергетических проектов и повысить долю локализации оборудования с нынешних 68 до 85 %. Ветролопасти, которые вы видите, поедут в Дагестан, на новолакскую площадку. Это будет самая крупная в стране ветростанция. У нас есть и контракты за рубежом, в первую очередь в Киргизии: партнеры по Евразийскому экономическому союзу ждут от нас экспорта технологического суверенитета в части ветроэнергетики. Мы будем отправлять лопасти на их станции. Ряд других стран прорабатывают строительство не только АЭС, но и зеленых энергетических кластеров, куда входят ветро- и солнечная генерация», — заявил Алексей Лихачев.
Проектная мощность завода — 450 лопастей в год. Для Новолакской ВЭС в этом году понадобится около 400. В среднем же потребности ветроэнергетического дивизиона «Росатома» будут составлять 360 лопастей в год.
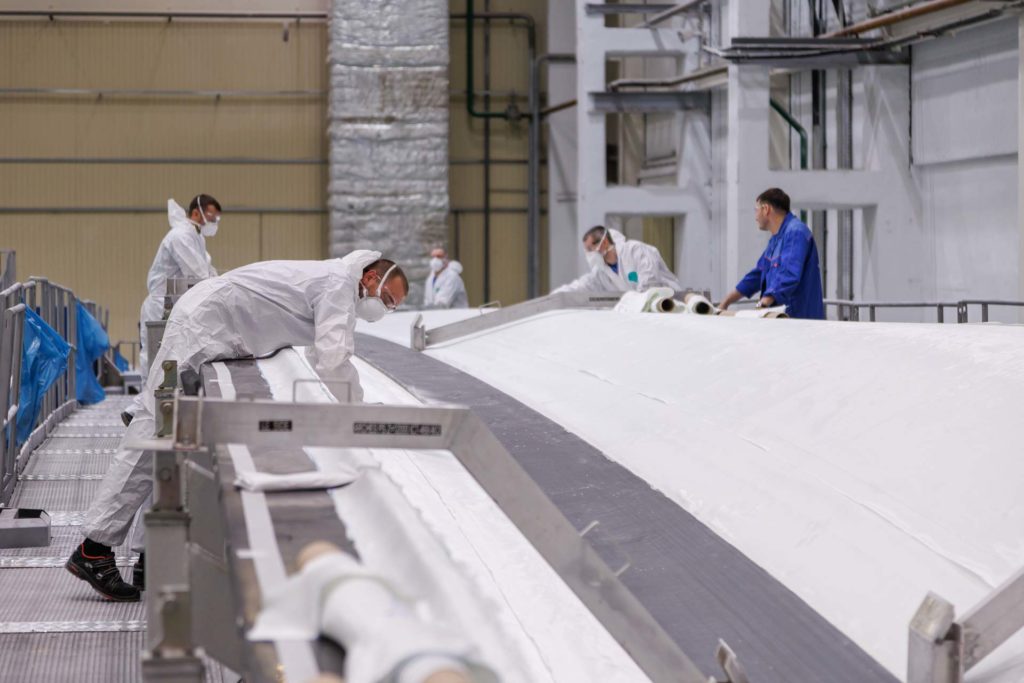
Особенности лопасти
Завод в Ульяновске выпускает лопасти длиной 51 м. Они подходят для турбины мощностью 2,5 МВт, которую использует «Росатом Возобновляемая энергия», и лучше 49‑метровых лопастей LM по КПД. Лопасти длиной 62 м, которые делала в России Vestas, были рассчитаны на турбины мощностью 4,2–4,5 МВт. Если возникнет потребность, новое предприятие сможет производить и такие.
Весят лопасти 8,5 т и на 90 % состоят из стеклокомпозита, на 10 % — из углекомпозита. В изготовлении используют ткани композитного дивизиона «Росатома», бальзовое дерево, эпоксидный и полиуретановый клей и листы из поливинилхлорида.
Стеклоткани нарезают на раскройном комплексе, скручивают в рулоны и сортируют: часть идет на наветренную сторону лопасти, остальное — на подветренную, они отличаются по геометрии. Параллельно изготавливают полки лонжеронов. Полка — это полоса из нескольких слоев углеткани, идущая по всей длине половинки лопасти. Полки закладываются в оболочки, на них опираются сдвоенные лонжероны из стекловолокна — основные силовые элементы, позволяющие конструкции выдерживать ветровую нагрузку в сотни тысяч килограммов.
Затем формируют половинки лопастей: в форму выкладывают стекловолокно, полки лонжеронов, элементы крепления лопасти к хабу генератора (гондоле), сетки, трубки и проч. Все укрывают пленкой, вакуумируют и подают смолу. После отверждения, установки лонжеронов и системы защиты от молнии половинки примеряют и склеивают. Качество шва проверяют дефектоскопом и термографической камерой. В собранной лопасти фрезеруют втулки крепления, ламинируют клеевые швы, чтобы укрепить их, оценивают геометрические параметры, покрывают шпатлевкой, красят, взвешивают, балансируют и отправляют на склад готовой продукции.
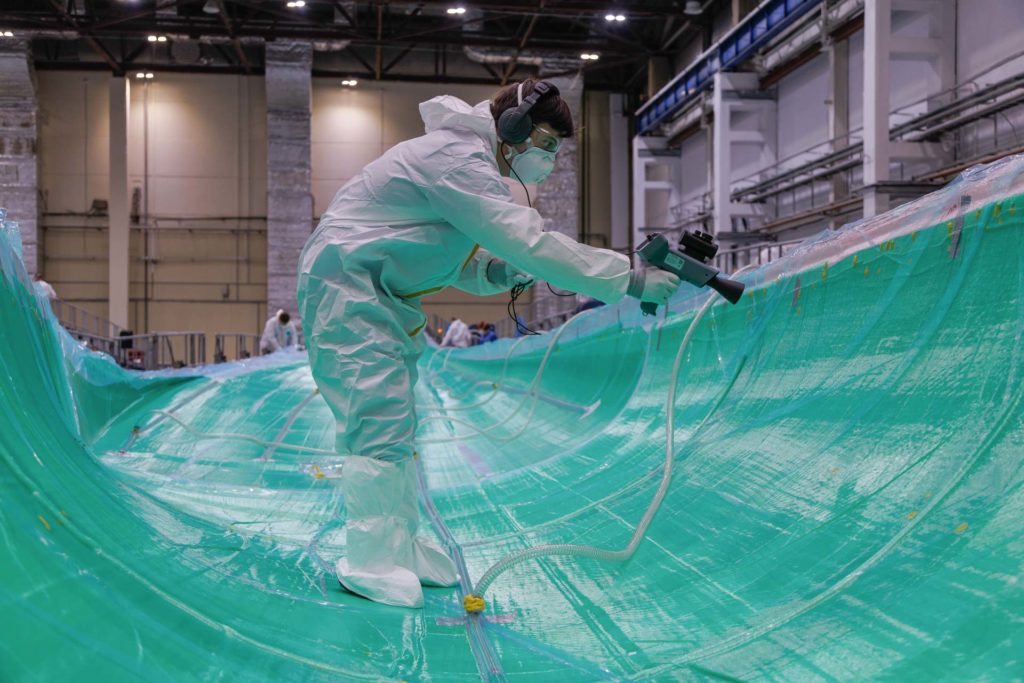
Композитные кадры
В Ульяновске завод считается хорошим работодателем, туда переходят из других мест на более высокую зарплату. Едут не только из Нового города — района вокруг авиастроительного комплекса, но и из старой части Ульяновска, хотя добираться оттуда довольно долго: по мосту с правого на левый берег Волги.
Композитный дивизион еще в 2022 году открыл на базе Ульяновского государственного технического университета (УлГТУ) центр компетенций «Технология композитов». Там готовят студентов и доучивают пришедших на завод специалистов, испытывают новые материалы и отрабатывают технологии. «Те, кто учился здесь, не беспокоятся, что их знания через какое‑то время обесценятся. Все, что связано с композитным производством, — это надолго», — уверена ректор УлГТУ Надежда Ярушкина.
Студенты приходят, потому что им интересно. В лаборатории хорошее оборудование, проводится много экспериментов и исследований. Вот Иван Габин в конце первого курса побывал в лаборатории — и устроился туда на работу, уже два года изготавливает штампы для оснастки, исследует материалы. Например, для деталей крепления грузов на железных дорогах в лаборатории подбирали материал из реактопластов с разными рублеными волокнами. Нашли оптимальный вариант и сделали опытную партию.
И конечно, в лаборатории можно услышать множество шуток и удивительных фактов. Например, что при испытаниях самолеты обстреливают из пушек морожеными курами. Эффект примерно тот же, как от столкновения с настоящими птицами в воздухе. Проверили — композитные компоненты самолета МС‑21 выдерживают.
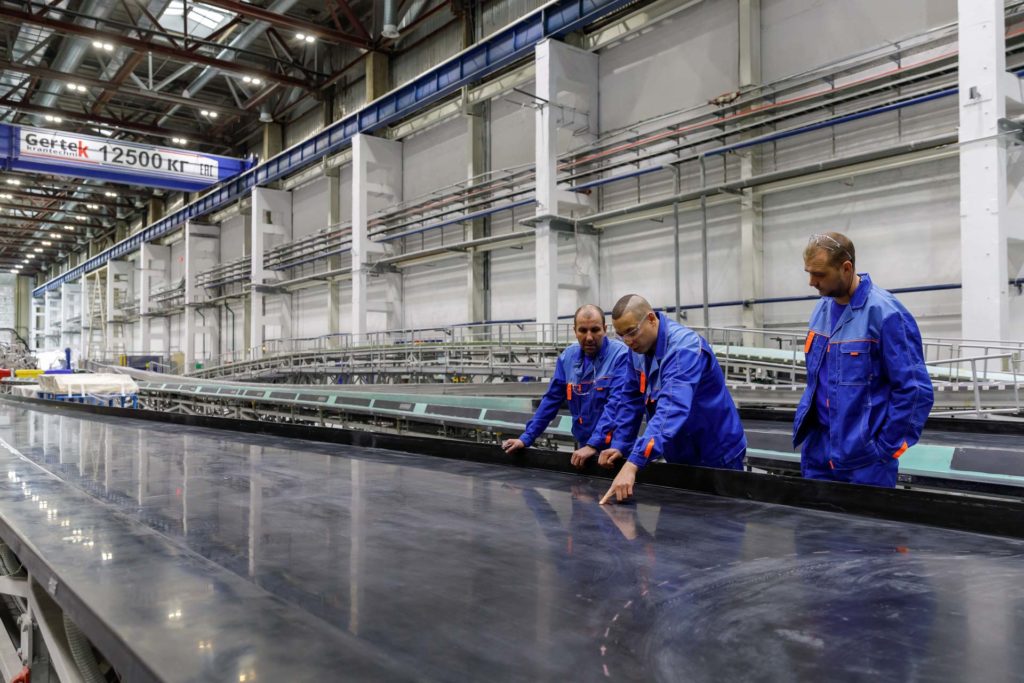