Прогиб просчитан: на энергоблоках с реакторами РБМК внедрили систему контроля геометрии топлива
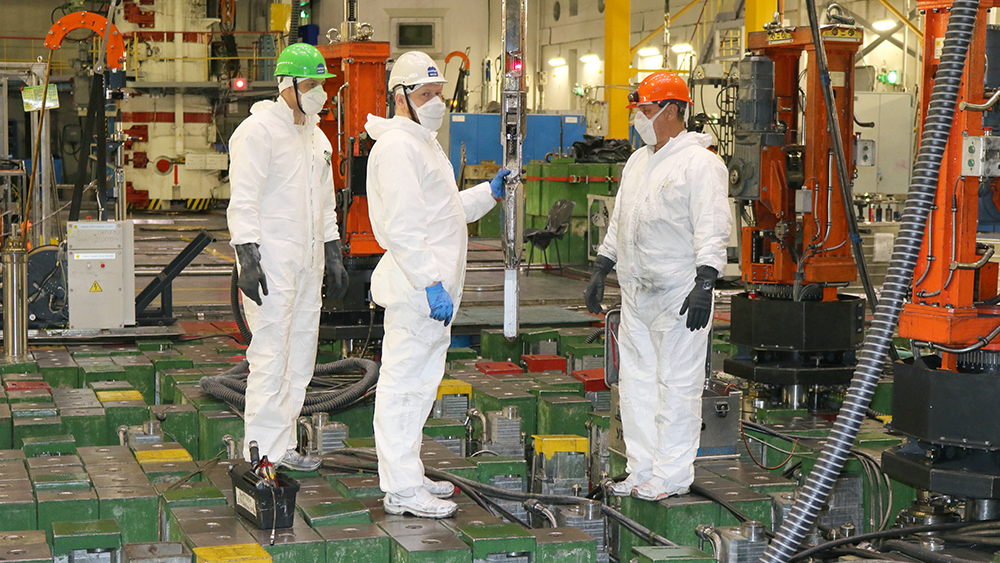
Система, не имеющая аналогов в мире, позволяет в ходе планово-предупредительного ремонта (ППР) существенно экономить время и деньги. В опытной эксплуатации новинка показала себя отлично, теперь такие устройства разрабатывают для первого в мире реактора четвертого поколения БРЕСТ-ОД‑300.
Решетки Брэгга
Сердце системы — оптоволоконные датчики Института радиотехники и электроники (ИРЭ) им. Котельникова РАН. «Парк реакторов РБМК довольно старый. Активная зона таких установок состоит из графитовой кладки, которая под воздействием температуры и радиации со временем разбухает, растрескивается. Из-за этого могут деформироваться каналы, в которые устанавливают тепловыделяющие сборки — ТВС, — объясняет заместитель директора ИРЭ по научной работе Олег Бутов. — Деформация канала, или так называемая стрела прогиба, — важнейший эксплуатационный параметр».
Сильное искривление графитовой кладки чревато повреждением ТВС, стержней систем управления и защиты, кожуха реактора. Чтобы проконтролировать деформацию, до недавнего времени нужно было останавливать и расхолаживать реактор, выгружать сборки. Со всеми этими манипуляциями диагностика занимала две-три недели. Уникальность датчиков ИРЭ в том, что они могут контролировать геометрию топлива без останова реактора и выгрузки ТВС.
Датчик представляет собой оптоволоконный стержень-световод особой конструкции. Внутри сердцевин световода излучением фемтосекундного лазера записана наноструктура, имеющая определенный период, — брэгговская решетка. «Работает световод за счет эффекта полного внутреннего отражения, — рассказывает Олег Бутов. — Двигаясь вдоль решетки, свет отражается, но только на определенной длине волны: например, зеленый и синий проходят, а красный отражается. Когда световод изгибается или нагревается, мы видим это изменение в спектре отражения».
Оптоволокно в реакторе
Раньше использовать оптоволокно в реакторах никому в голову не приходило, так как в условиях высокой радиации оно моментально мутнеет и перестает пропускать свет. Ученые выяснили, что причина в примесях: обычно волокно легируют германием, но волокно из высокочистого кварца обретает радиационную стойкость.
Конструкцию измерительной штанги с такими датчиками разработала обнинская компания «Пролог». Она же провела аттестацию системы и наладила промышленное производство. «В кварцевом стержне-световоде по всей его длине нужно 80 структур-датчиков, — рассказывает Игорь Шевцов, директор «Пролога». — Далее измерительная штанга помещается в специальную стальную оболочку. Сверху делается оптический разъем. От него оптоволоконный кабель идет к особому прибору — оптическому интеррогатору, который оцифровывает сигналы от датчиков. Далее программное обеспечение обрабатывает эти сигналы. Конечный продукт — профиль измерительной штанги и таблица с набором данных, показывающая прогиб в каждой ее точке».

Существенная экономия
Систему контроля геометрии топлива внедряют на всех российских реакторах РБМК. «На Смоленской АЭС, например, оптоволоконные датчики впервые были использованы в составе измерительной системы ИКС49 производства компании «Пролог» во время планово-предупредительного ремонта в 2018 году, — отмечает главный специалист отдела ядерной безопасности и надежности станции Алексей Леонов. — С тех пор ни один ППР не обходится без них».
Измерительную штангу устанавливают в центральный канал ТВС. «Надо отметить, что используют систему в тепловыделяющих сборках определенного типа — Сб.49, — добавляет Алексей Леонов. — В них, в отличие от ТВС Сб.50, есть гамма-полость — отверстие в центральной трубке».
На измерение одного канала уходит 15 минут, затем штангу переставляют в следующий. «Если показатель стрелы прогиба приближается к установленному регламентом, значит, необходимо приступать к работам по управлению ресурсными характеристиками графитовой кладки реактора. Именно такого вида работы проводятся с 15 июня на энергоблоке № 1 Смоленской АЭС», — говорит Алексей Леонов.
Измерения обычно проводят на остановленном, но еще не расхоложенном реакторе, до начала основных ремонтных работ. Это значительно сокращает срок ППР без потери качества и уровня безопасности. Как рассказал Алексей Леонов, в ходе текущего ремонта на первом блоке Смоленской станции применение датчиков позволило сэкономить 26 суток.
Контроль в перспективе
По словам разработчиков, систему можно адаптировать для реакторов любого типа. Причем она может отслеживать деформацию и других элементов реакторной установки. «Эти же датчики будут использоваться в реакторе БРЕСТ-ОД-300 для контроля формоизменений активной зоны, исследования вибрации парогенераторов и топлива», — сообщает Игорь Шевцов.
Олег Бутов уверен, что у разработки есть перспективы не только в атомной отрасли: «Датчики можно применить в строительстве для контроля сложных инженерных конструкций и сооружений, в нефтегазовой отрасли для внутрискважинного контроля, в геологии — например, для контроля оползней, анализа эволюции геологических разломов, а также во многих других областях».