Лучшие производители и разработчики — о реалиях и возможностях российского рынка композитов
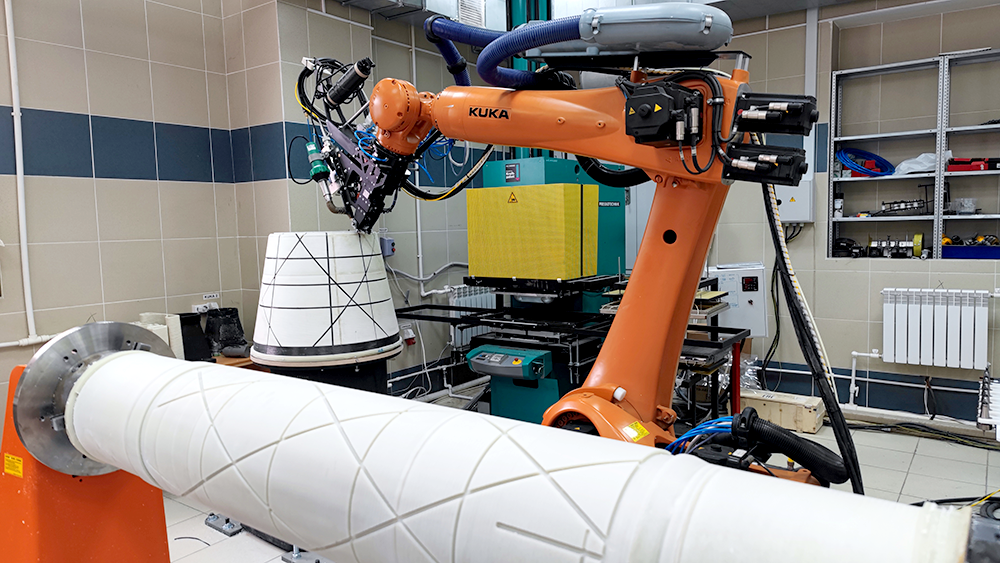
В рамках X Форума «Композиты без границ», организованного компанией «Юматекс», прошла церемония вручения одноименной премии. Мы расспросили представителей организаций-лауреатов, чем они занимаются, в каком направлении развиваются и с какими проблемами сталкиваются.
«СТОИТ ДИЛЕММА — ПРОИЗВОДИТЬ САМИМ ИЛИ ИМПОРТИРОВАТЬ ИЗ КИТАЯ»
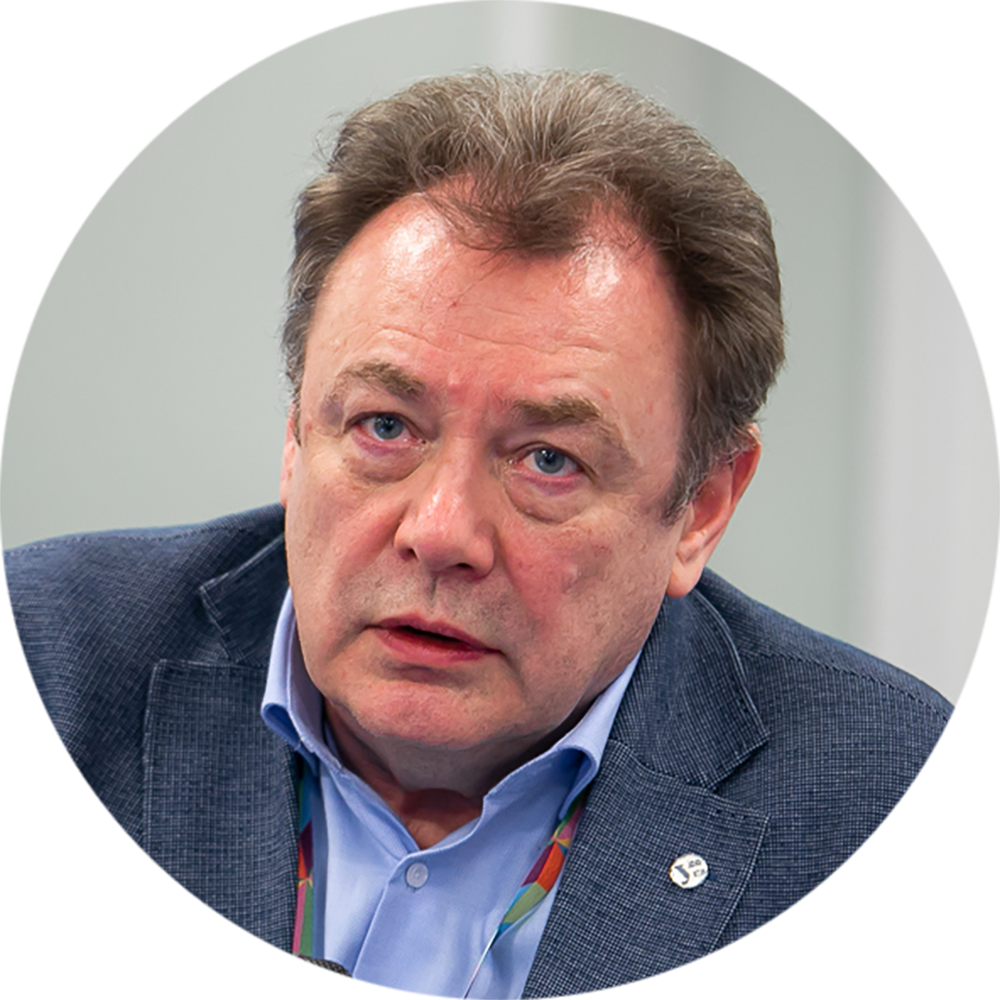
Михаил Колобов
Учредитель НПО «Фотополимер», номинация «Лидер в композитном импортозамещении»
— Наша компания занимается фотополимерными материалами. Это смолы, у которых под воздействием ультрафиолетовых волн распадается фотоинициатор, высвобождаются активные радикалы, в результате чего смолы становятся твердыми.
Поскольку основные производители ушли и российский рынок лишился смол для 3D-печати, фотополимерных лаков, фотоотверждаемых композитных материалов, которые используют в производстве препрегов, и т. д., мы решили открыть компанию, которая возьмет на себя это направление. Уделили много времени обратному инжинирингу и вывели свои разработки.
Следующая задача — начать производство нескольких изделий и материалов.
Это фотоотверждаемые препреги, которые используют для изоляции трубопроводов, и композитные фотоотверждаемые трубы для доставки нефти с офшорных платформ на берег. Другие направления — оксидные лаки, полиэфиркетонкетоны — изоляционные материалы для проводов электромобилей.
Проблемы, с которыми мы сталкиваемся, — нехватка исходных материалов для полиуретановых эмульсий, эпоксидных смол и оксидных лаков. Синтезировать их несложно, но стоит дилемма — производить самим или импортировать из Китая. В некоторых случаях китайские дешевле. Создание собственной производственной базы — это вопрос к Минпромторгу и Минфину, потому что требуется значительное финансирование. Я считаю, нужно по максимуму развивать малотоннажный синтез. Иначе мы все время будем вынуждены что-то закупать. А развив собственное производство, повысим рентабельность следующих переделов и значимость России на мировом рынке.
«НАШИ КОЛЯСКИ ПРОЧНЫЕ, НО ЛЕГКИЕ»
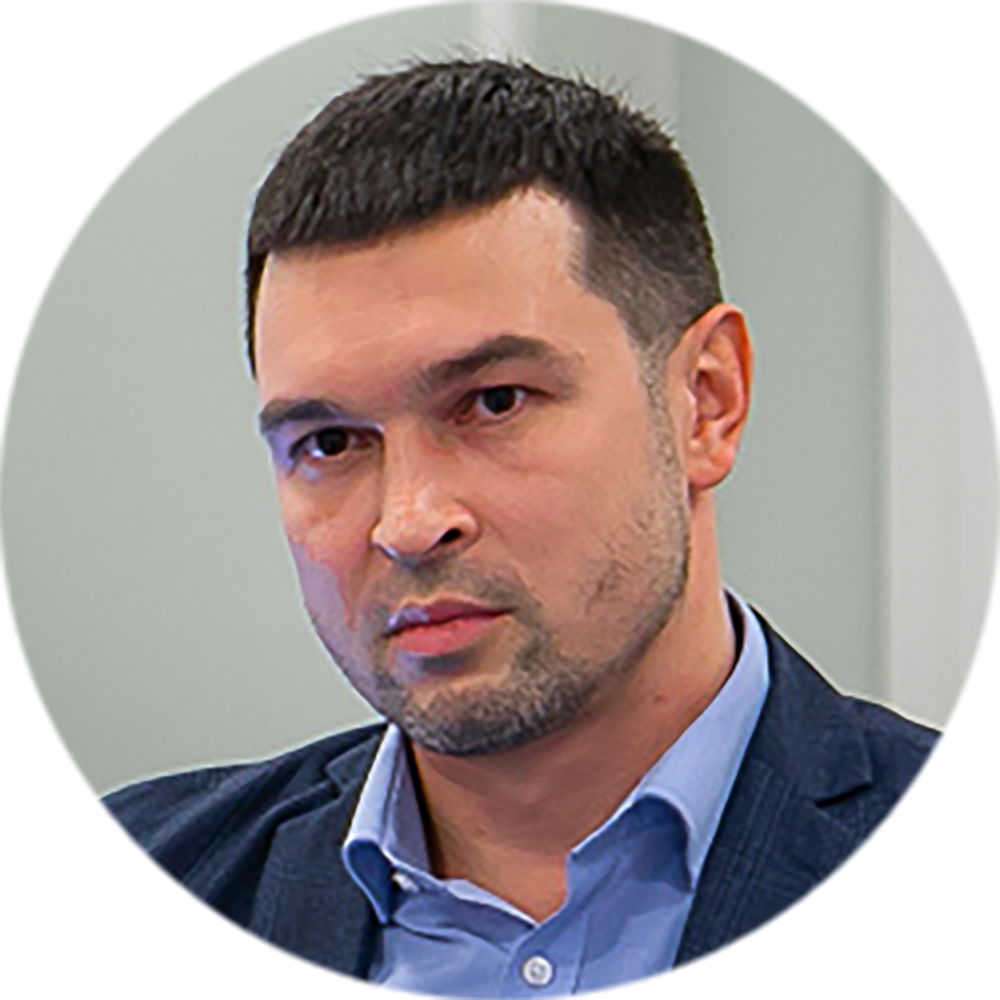
Руслан Валиев
Директор по производству, «Факир», номинация «Серийные изделия из композитов»
— Мы выпускаем инвалидные кресла-коляски из карбона российского производства, базируемся во Владивостоке. Наш руководитель, сам инвалид-колясочник уже 23 года, хорошо изучил, какие коляски наиболее комфортны.
Благодаря композитам наши коляски прочные, но легкие: вес рамы — не больше 5 кг. Мы ведем серийное производство по индивидуальным параметрам. Цена сопоставима с ценой западных аналогов, а делаем мы коляску быстро, всего за 30 дней. Конкуренты — дольше.
Ближайшая задача — достигнуть стопроцентной локализации производства. Пока шасси мы закупаем в Китае, но в этом году хотим приобрести оборудование для их производства. Также планируем разработать детскую линейку.
К сожалению, пока цена на композитные коляски кусается — в базовой комплектации 250 тыс. рублей. Обращаемся к правительству с просьбой сделать так, чтобы инвалиды получали их бесплатно.
«НАШ РОБОТ МОЖЕТ РАБОТАТЬ КРУГЛОСУТОЧНО»
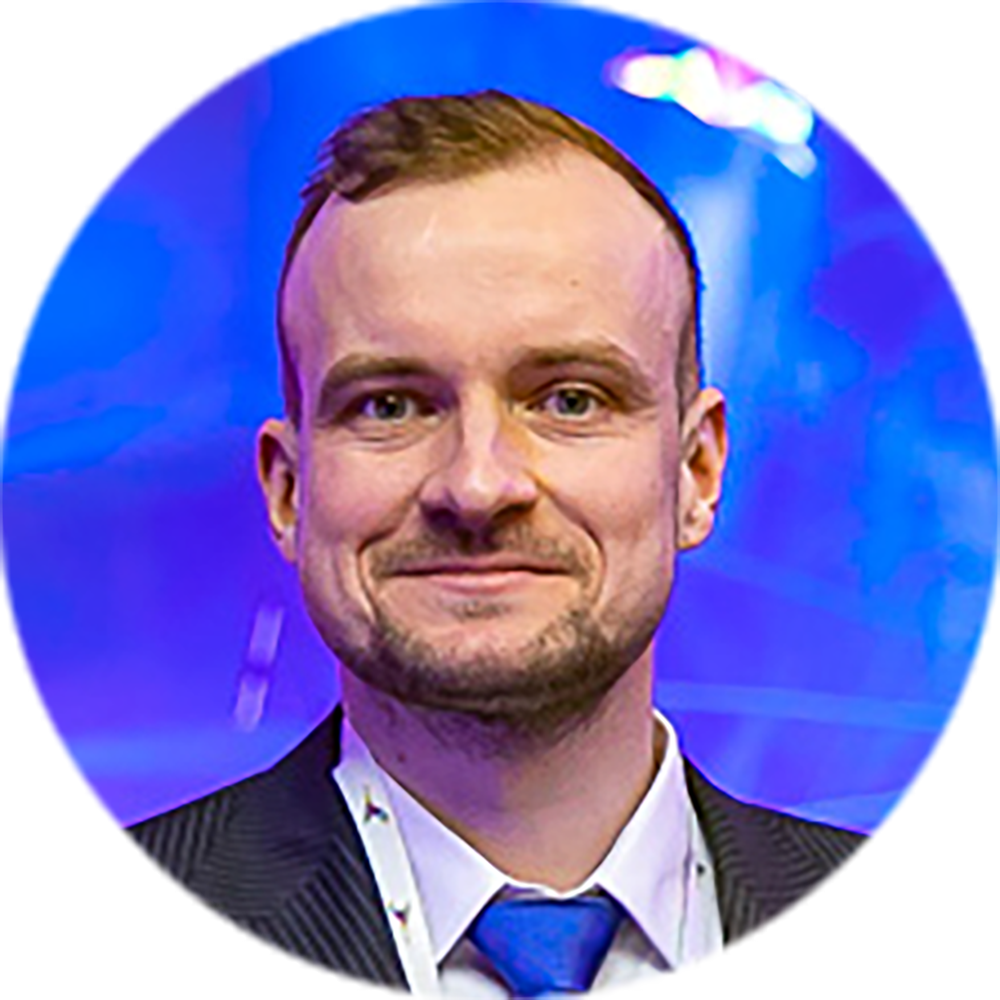
Леонид Шабалин
Ведущий научный сотрудник, Центр композитных технологий Казанского национального исследовательского технического университета, номинация «Уникальные композитные решения»
— Чтобы изготовить композитное изделие, нужна мастер-модель и композитная оснастка, которая придает форму будущему изделию. Наш роботизированный комплекс позволяет в автоматизированном режиме выполнить 3D-печать достаточно жесткой и прочной композитной оснастки, провести механическую обработку поверхности для формования композита и изготовить само изделие. Все манипуляции под контролем оператора выполняет робот. Он может работать круглосуточно без перерывов и имеет высокую повторяемость — это важный параметр при выкладке ленты из композитных волокон.
Импортных составляющих в нашем комплексе немного. Даже такой сложный элемент, как лазерная головка, отечественный.
Робот существует в единственном экземпляре, но мы и не собираемся становиться серийным производителем. Наша задача — предоставить технологию предприятиям. В течение года будем дорабатывать ее, чтобы можно было с уверенностью сказать, что она применима для изготовления определенной номенклатуры изделий. Затем — сервисное сопровождение предприятий. Мы намерены разрабатывать новые конструкции и оснастку на основе нашей технологии. Это будет не просто технология, а решение для полного цикла создания изделия.
Сейчас самая большая проблема — найти композитным материалам применение в промышленности. Конструкторы должны быть готовы закладывать эти материалы в свои решения. А мы должны подкрепить их уверенность в эффективности решений с точки зрения стоимости и технологичности. Для этого нужны финансовые вливания в производство роботов-манипуляторов, экструдеров (машин для непрерывной переработки полимерного сырья. — «СР»), а главное — в подготовку кадров. Наш университет готов взять на себя обучение и отработку технологий вплоть до серийного производства.
Из проблем еще отмечу отсутствие армированных высокотемпературных термопластичных материалов и широкой номенклатуры углеродных лент на основе термопластичных и термореактивных материалов. Их необходимо разрабатывать. «Юматекс» движется по этому пути, и, надеюсь, совместно мы сможем внедрить эту технологию в серийное производство.
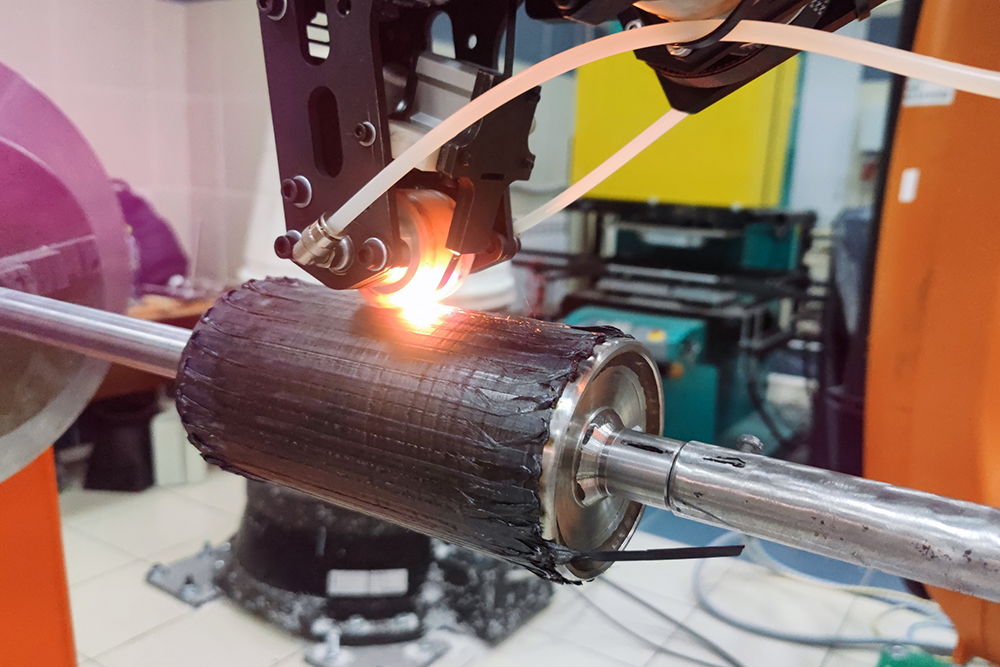
«СКОРО МЫ УВИДИМ КОМПОЗИТНЫЕ СУДА, СОЗДАННЫЕ НА НАШЕМ ПО»
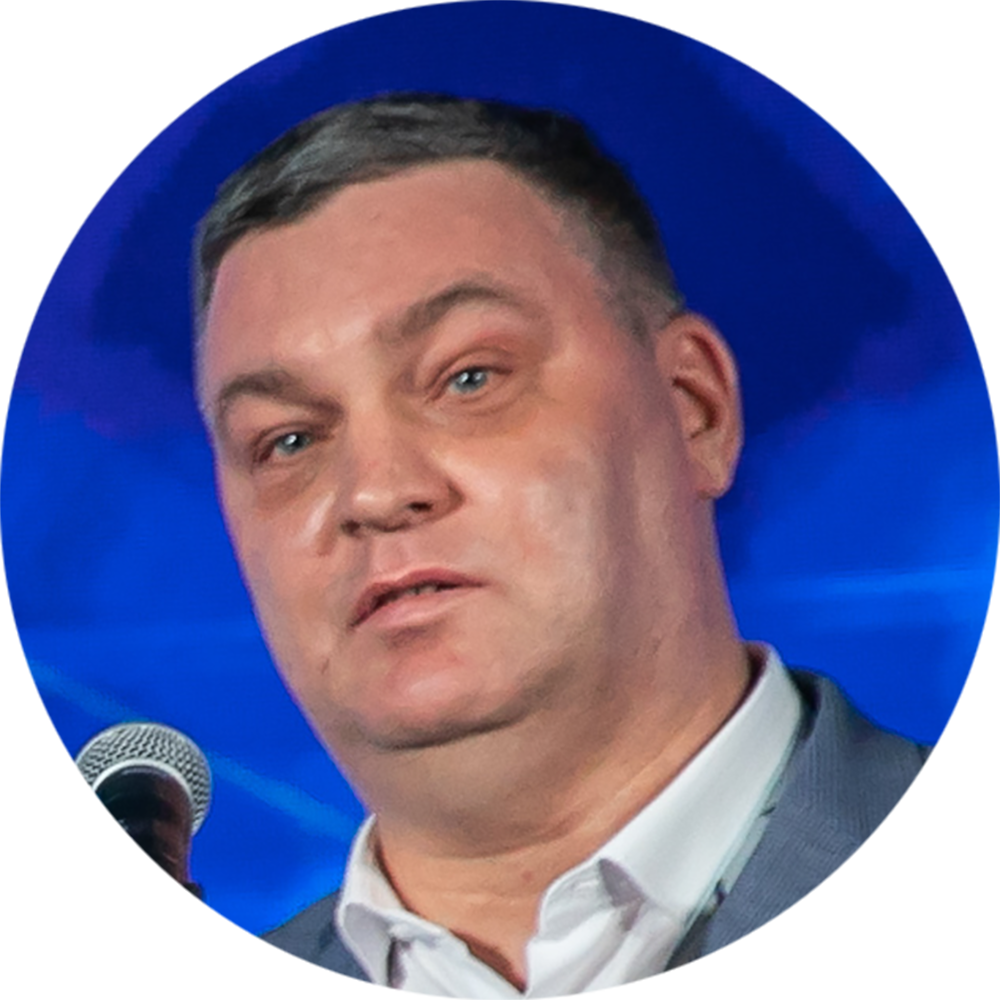
Альберт Назаров
Учредитель «АН Марин Консалтинг», номинация «R&D-разработки в области композитов»
— Мы разрабатываем программное обеспечение для расчета композитных конструкций в судостроении. Оно подходит для всех судов, где применяются композиты. В настоящее время композитное судостроение — это суда до 70 м, но в перспективе, думаю, будут и более габаритные. Мы знаем, что за рубежом экспериментируют с композитами на транспортных крупнотоннажных судах. Полагаю, в ближайшее десятилетие значительная доля судов и компонентов для них будут из композитов.
Для судостроения необходимы программные средства расчета, соответствующие специальным нормативным требованиям. Морская индустрия регулируется правовыми документами, имеющими статус международных конвенций. Российские регулирующие органы, которые занимаются сертификацией и классификацией судостроения, ориентируются прежде всего на требования конвенций. Мы разработали ПО в партнерстве с Морским регистром (Российским морским регистром судоходства. — «СР») и Российским классификационным обществом, а также компанией «Юматекс», идеологом этой разработки. В конце декабря прошлого года получили сертификат Морского регистра, в январе — Российского классификационного общества в судостроении. Наше ПО уже применяют, есть и перспективные заказчики. Полагаю, скоро мы увидим композитные суда, созданные на нашем ПО.
Одна из проблем, которую необходимо решать, — российская нормативная база заточена под стальное судостроение. Те люди, которые писали правила, не думали о композитах или не хотели, чтобы их использовали. Но мы над этим работаем — в прошлом году подали пять нормативных предложений в Морской регистр, три уже приняты. Надо отдать должное регуляторам: они постепенно совершенствуют и адаптируют нормативную базу к композитам.
Второй момент — доверие заказчиков, судоходных компаний. Им надо объяснять преимущества этого материала, тогда мы увидим больше композитных судов. Думаю, что кто-то просто должен начать, и запустится цепная реакция. Пока шаги очень робкие. В странах Азии же — в Индии, на Шри-Ланке, в Австралии — композиты используются повсеместно. Например, в Японии весь промысловый флот — из композитных материалов. Они дают огромное преимущество в массе корпуса.
Зарубежные классификационные общества присваивают композитам ледовый класс, и я думаю, мы сможем убедить использовать композиты для арктического флота. Тем более что ледовый класс для композитов существовал в ледовых правилах — для стеклопластиков, но потом исчез. Думаю, что нужно его вернуть, и мы над этим работаем.
«МЫ ЭКСПОРТИРУЕМ КОМПОЗИТНЫЕ И МЕТАЛЛОКОМПОЗИТНЫЕ НАКЛАДКИ В 22 СТРАНЫ»
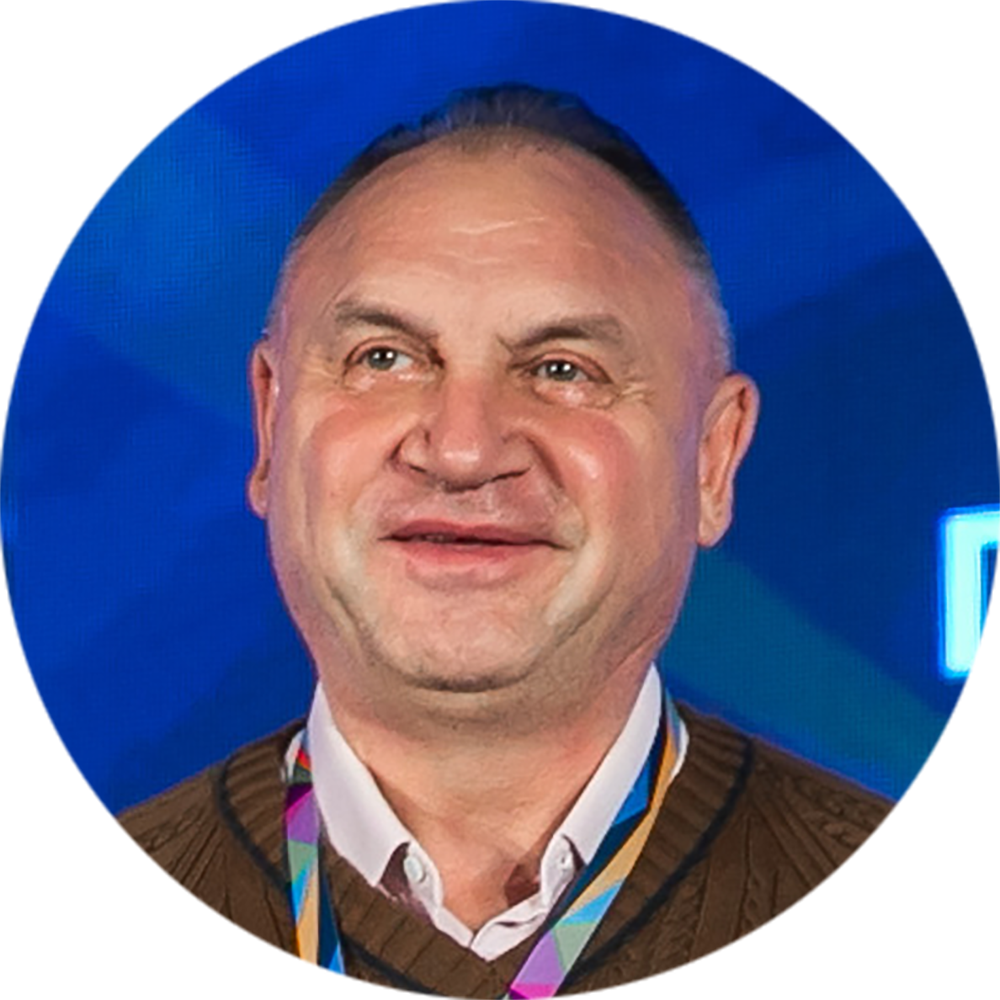
Андрей Ушаков
Гендиректор НПП «АпАТэК», номинация «Лидер в экспорте композитов»
— Мы более 30 лет занимаемся разработкой, производством и внедрением высокоответственных конструкций из полимерных композиционных материалов, ПКМ, в дорожном, железнодорожном и городском хозяйстве. И мы одни из немногих, кто сделал прорыв в новых технологиях и материалах. Четырежды получали Гран-при JEC Awards — самой престижной глобальной премии в нашей области. Впервые — в 2002 году за внедрение композитных накладок на сети железных дорог России и стран Балтии. Другие Гран-при — за водоотводные лотки, кузов вагона-хоппера и первый в мире железнодорожный мост из ПКМ. Очень рады, что в 2023 году нам вручили российскую премию на форуме «Композиты без границ» за внедрение накладок для изолирующих стыков железнодорожных рельсов.
Мы экспортируем композитные и металлокомпозитные накладки в 22 страны. Первые применяются на участках со средней и невысокой интенсивностью движения, вторые — на участках высокоскоростного движения и с большим объемом тяжеловесных перевозок. Композитные накладки легкие, их просто монтировать, а металлокомпозитные обладают повышенной надежностью и обеспечивают большую плавность движения состава. В России наши накладки используются примерно на 65 % железнодорожной сети. Это порядка 120 тыс. км путей — три оборота по экватору.
У нас широкая номенклатура, и, если говорить о накладках, мы разработали и сертифицировали высокопрочную магнитопроводную накладку для участков, где сейчас используются композитные накладки и где нужно снижать намагниченность рельсов.
Чтобы расширить использование композитных конструкций в разных отраслях, необходимо решить три ключевые задачи. Во-первых, ускорить сертификацию продукции из ПКМ, чтобы сократить цикл внедрения до трех — пяти лет, уменьшить себестоимость в два-три раза и вовлечь в производство как можно больше малых и средних предприятий. Во-вторых, нужно разрабатывать и внедрять технологии автоматического производства крупногабаритных конструкций из ПКМ для транспортной инфраструктуры, машино- и судостроения, что позволит снизить себестоимость продукции на 10–15 %. В-третьих, — уточнить значения коэффициентов запаса для конструкций из ПКМ в сводах правил и стандартов, чтобы снизить массу готовых изделий на 25–35 % и, как следствие, их себестоимость на 20–25 %.
СПРАВКА
«Композиты без границ. Awards» проводился в пятый раз. Было подано 50 заявок — вдвое больше, чем на предыдущий конкурс. Жюри состояло из пяти экспертов: замминистра науки и высшего образования РФ Дарьи Кирьяновой, гендиректора «Юматекса» Александра Тюнина, гендиректора ОНПП «Технология» Андрея Силкина, и. о. ректора РХТУ Ильи Воротынцева и заместителя гендиректора корпорации «Иркут» Анатолия Гайданского.