Рычаги изменений: как внедрение каракури оживило инженерное творчество в отрасли
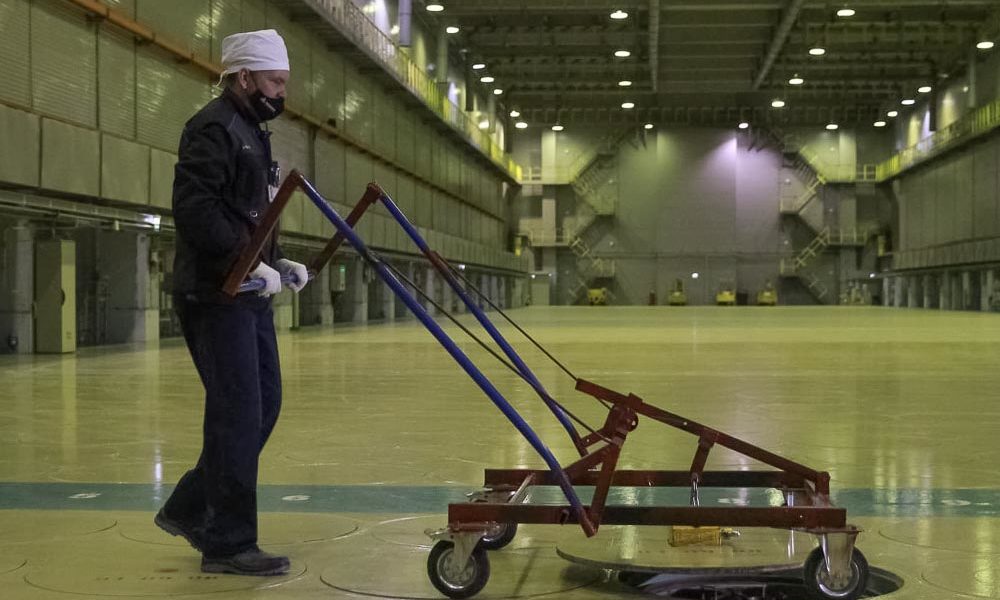
Сегодня японским термином «каракури» в госкорпорации уже никого не удивишь. Устройства для упрощения работы внедряют в отрасли пять лет, с 2018 года. Вместе с экспертами Корпоративной академии «Росатома» мы выбрали пятерку самых эффективных механизмов, созданных в 2021 году, и обсудили с авторами—каракуристами пользу их изобретений.
Устройство для выгрузки и загрузки заготовок на станок. Внедрено на Чепецком механическом заводе
«С проблемой обратились работники цеха по производству технологических каналов для АЭС. В этом цеху обрабатывают заготовки для штуцеров, предназначенных для реакторов большой мощности канального типа, — рассказывает Александр Пойлов, работник цеха, специалист по комплексной оптимизации производства. — Заготовки цилиндрической формы перемещали от станка к станку вручную или на тележках. Вес каждой — 38 кг, к тому же после подрезки у них острые кромки. Сотрудники перчатки рвали, рисковали получить травму. Как облегчить им работу?
Мы с коллегами разработали эргономичную расстановку оборудования и внедрили каракури. От ленточнопильного станка идет наклонный рольганг, по которому изделие попадает в накопитель для заготовок. Заказчик просил, чтобы заготовка, перемещаясь по рольгангу, лежала на боку, а в накопителе вставала на торец. Чтобы этого добиться, придумывали противовесы, разбирались, как заготовки падают. Но оказалось, что просто нужен верный перепад высоты на роликовом конвейере, и заготовка стабильно приземляется на торец. Чтобы поднять заготовку к другому станку, где изделие обрабатывают, нужен был еще один механизм. Долго решали какой. Думали даже о покупке манипулятора. Но решили использовать рычаг. Рольганг поднимается с помощью механических связей на 60 см вверх, и вновь по роликам изделие перекатывают уже в токарный станок.
Благодаря устройству сократили риск получения травм, что и было главной задачей. Кроме того, снизили трудоемкость в 1,5 раза — теперь каждый сотрудник может потратить высвобожденное время на управление сразу тремя станками».
Устройство для подъема крышек гнезд хранения ОЯТ. Внедрено на Горно-химическом комбинате
«При регламентном контроле герметичности на нашем участке хранения отработанного ядерного топлива требуется за смену вскрыть до 80 крышек гнезд хранения, — поясняет изобретатель Андрей Поляковский, аппаратчик сухого хранилища завода регенерации топлива. — Крышки весят от 80 до 100 кг. Штатное приспособление — электротележка — очень неудобное: у нее проблемы с маневренностью, чудовищное количество переключений и 30 м кабеля, который надо разматывать и сматывать. Двум аппаратчикам приходилось распределять нагрузку на три смены.
Проблему решили с помощью внедрения мобильного устройства открытия и перемещения крышки. Оно устроено по принципу гвоздодера. Придумал я это на даче, выдергивая гвозди. Тогда и смекнул: если два гвоздодера соединить перемычкой внизу и на эту перемычку подвесить захват, получится приспособление, которым легко поднять крышку.
В нашем подразделении нашлись списанные в металлолом леса, их и использовали для изготовления устройства. Два рычажных механизма соединили перемычкой, на которую опирается балка с магнитным захватом для поднятия и установки крышки на гнездо хранения. Но одно дело — приподнять, другое — откатить. И тогда я решил поставить это приспособление на четыре колеса. После начали наладку: отмеряли, приваривали, что-то отрезали, делая устройство удобным для использования.
Когда закончили, продемонстрировали коллегам, как оно работает. Вдвоем с напарником за пять часов открыли 100 крышек, при этом совсем не устали. Дело ведь даже не в скорости работы, а в том, как ты потом выполняешь другие задания — без усталости, со светлой головой. При подъеме крышки воздействие на рычаг — всего 10 кг. При этом рычаг опускается вниз, используя вес рабочего. Как следствие, снижается травматичность, а после работы у коллег остаются силы на общение с семьей и увлечения».
ГДЕ ОТТОЧИТЬ МАСТЕРСТВО
В «Росатоме» сформировалось сообщество специалистов, которые не только создают механические устройства, но и оттачивают инженерное мастерство на соревнованиях, вовлекают в это направление школьников и студентов.
Для участия в соревнованиях по каракури на чемпионате AtomSkills обратитесь в отдел кадров предприятия и пройдите первичный дивизиональный отбор. После победы на отраслевом конкурсе можно побороться за победу в национальном Кубке по рационализации и производительности. Сотрудники предприятий «Росатома» уже второй год побеждают в соревнованиях кубка в компетенции «Инженерное мышление. Каракури». Есть и соревнования для всей семьи — фестиваль изобретателей «Каракураж».
Устройство для снятия крышек транспортного упаковочного комплекта. Внедрено на Ростовской АЭС
«Топливо поступает на атомную станцию в кассетах, которые упакованы в контейнеры. Крышки контейнеров откручивают, достают кассеты, крышки устанавливают обратно, — рассказывает эксперт АЭС по каракури Руслан Арьков. — Все эти операции приходилось делать на вытянутых руках: оператор стоит перед ограждением, на площадке обслуживания, к контейнерам надо тянуться. При этом каждая крышка весит 38 кг, и спины сотрудников страдали при их поднятии.
Начали прорабатывать варианты, рисовали эскизы устройств. Работали командой. В нее вошли и сами операторы из цеха централизованного ремонта, и ведущие инженеры этого же цеха Владимир Пискунов и Алексей Ермак, и сотрудники отдела подготовки проведения ремонта, которые помогли собрать устройство по эскизам, и я, как куратор направления «Каракури». В итоге сделали конструкторскую документацию, согласовали ее. Несколько раз тестировали и налаживали, ведь устройству придется взаимодействовать с атомным топливом, все должно быть надежным. Теперь операторы простым движением рычага поднимают крышку, свободно достают топливо. И легким движением руки крышку возвращают на место. Таким образом, мы в восемь-девять раз сократили нагрузку на оператора, исключили риск падения этой крышки. И значительно увеличили скорость всей операции».
Самозажимной захват для перемещения контейнеров. Внедрен Ленинградским отделением филиала «Северо-Западный территориальный округ», ФЭО
«С чего все началось? У нас была задача разработать контейнер для сбора, транспортировки, хранения и захоронения радиоактивных отходов, — вспоминает Дмитрий Дрозжин, главный специалист-эксперт. — Мы сделали свой контейнер ЗМК‑3.0Ц. Он прошел сертификацию в области использования атомной энергии. А следующей целью стала разработка полуавтоматического захвата, чтобы можно было эти контейнеры размещать в хранилище без ручной строповки. Для захвата разработали конструкторскую документацию, изготовили и испытали опытный образец, а потом уже сделали несколько грузозахватных приспособлений для других филиалов ФЭО.
Как эта операция выполнялась раньше? В цех по обращению с радиоактивными отходами поступали контейнеры весом около 7 т. Для их перемещения работник вручную крепил стропы к проушинам контейнера. На перемещение контейнера из-за наличия ручных операций по его строповке и расстроповке тратили до 44 минут. Теперь оператор крана перемещает контейнер без дополнительной помощи: подводит захват к контейнеру и при опускании позиционирует его относительно контейнера с помощью щупов. Поднимаясь, захваты фиксируют контейнер за счет системы рычагов. Чтобы установить контейнер на место хранения, оператор опускает захват до крайнего нижнего положения, после чего он открепляется. Время перемещения контейнера сократилось до 24 минут».
Устройство передачи заготовок между рабочими местами. Внедрено на Ковровском механическом заводе
«На участке изготовления статоров поочередно проводят две операции — токарную подрезку статора и пайку электровывода, — объясняет Сергей Кучин, руководитель кайдзен-команды КМЗ. — Участок, где происходит пайка, отделен от оператора токарного станка по технике безопасности. Однако между ними нужно перемещать заготовки. Обработав статоры на станке, оператор складировал заготовки в тележку. Накопив шесть штук, перемещал заготовки ко второму станку и возвращался обратно. Эта операция проводилась 14–16 раз за смену с потерей времени на транспортировку.
Для оптимизации работы мы внедрили каракури — контактный склиз с возвратной тягой и противовесами. Сделали нишу между двумя рабочими местами. Оператор после токарной подрезки ставит заготовку в тару, и по наклонной поверхности статор едет к оператору пайки электровывода. Заготовку забирают, и тара под воздействием противовеса возвращается обратно к оператору токарного станка. Операция может проводиться непрерывно, и запас заготовок у оператора первого станка не образуется.
Благодаря внедрению этого устройства мы уменьшили объем незавершенного производства в шесть раз и снизили время ожидания оператора пайки. А главное — ушли от операции перевозки заготовок и сэкономили время сотрудников».
558
устройств внедрили отраслевые каракуристы за пять лет
>300 тыс.
человекочасов сэкономили эти механизмы
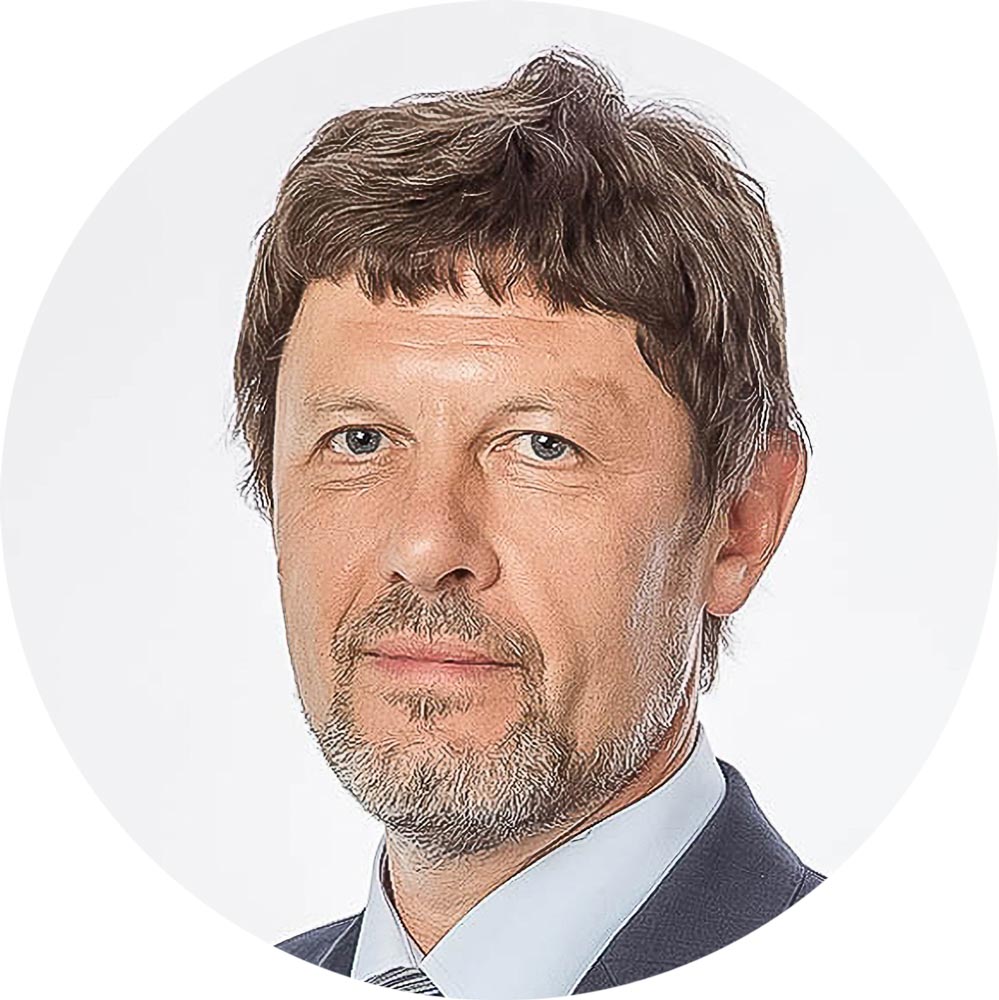
Сергей Обозов
Заместитель гендиректора по развитию Производственной системы «Росатом»
— Самое сложное в оптимизации процессов — увидеть проблемы и потери в собственной работе, к которой мы привыкли. И какая бы тяжелая она ни была, это кажется нам нормой. Каракури помогают устранять потери и реализовать свой инженерный потенциал.
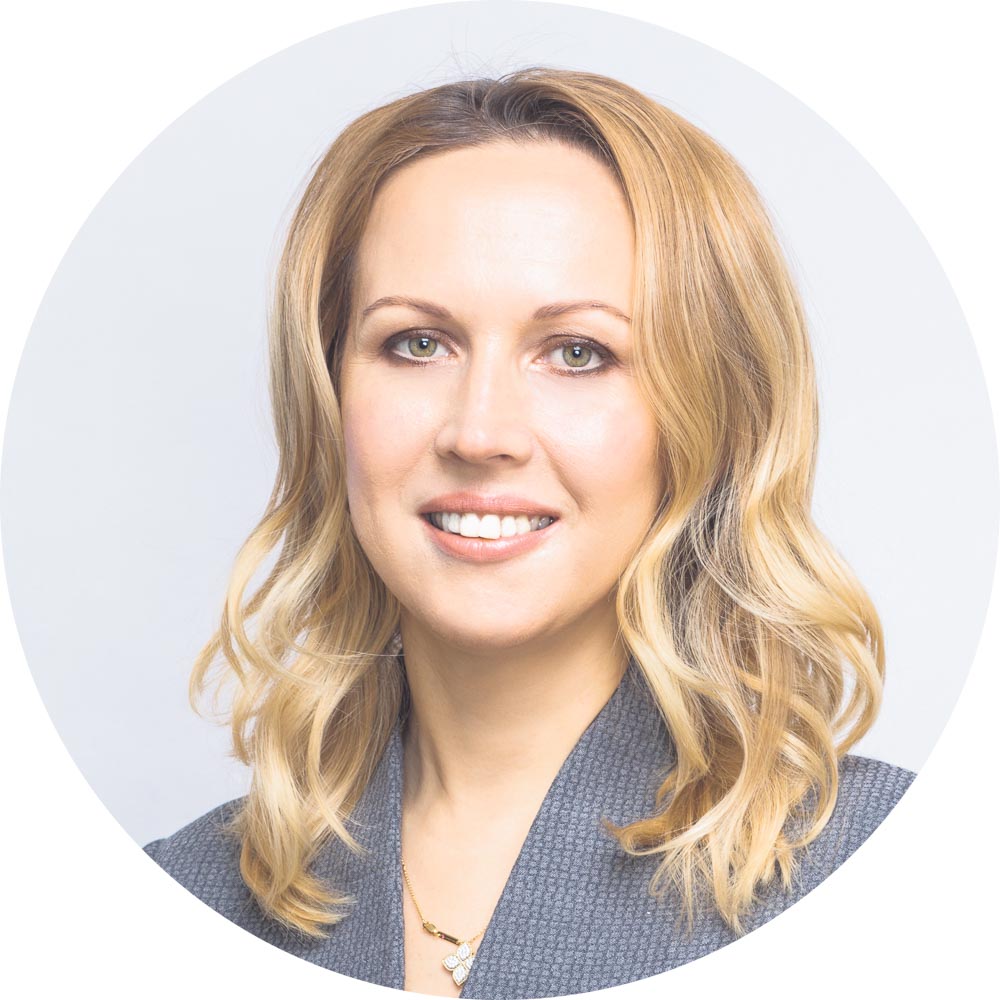
Татьяна Терентьева
Заместитель гендиректора «Росатома» по персоналу
— Каракури — это мощнейший инструмент для раскрытия потенциала. Они развивают креативность и нестандартное мышление, а это является основной компетенцией XXI века, как бы парадоксально это ни звучало. Каракури показывают, что могут сделать человеческие руки, насколько неограниченны потенциал и способности человека.