Предложения по улучшениям помогли ЭХЗ сэкономить 115 млн рублей
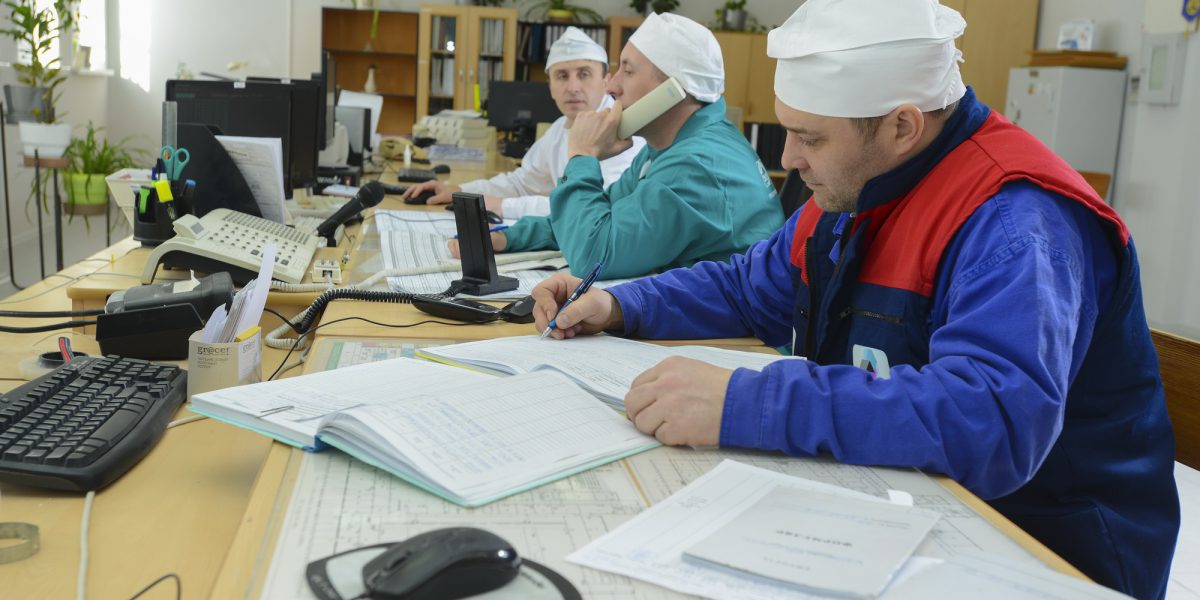
Почти 9 тыс. рацпредложений внедрили на Электрохимическом заводе в прошлом году. Экономический эффект от реализации ПСР-проектов составил 115 млн рублей. Это в очередной раз позволило заводу подтвердить статус ПСР-предприятия по итогам развивающей партнерской проверки, прошедшей в конце января. О самых успешных проектах рассказывают заводские лидеры ПСР-движения.
ЭКОНОМИМ ВОДУ
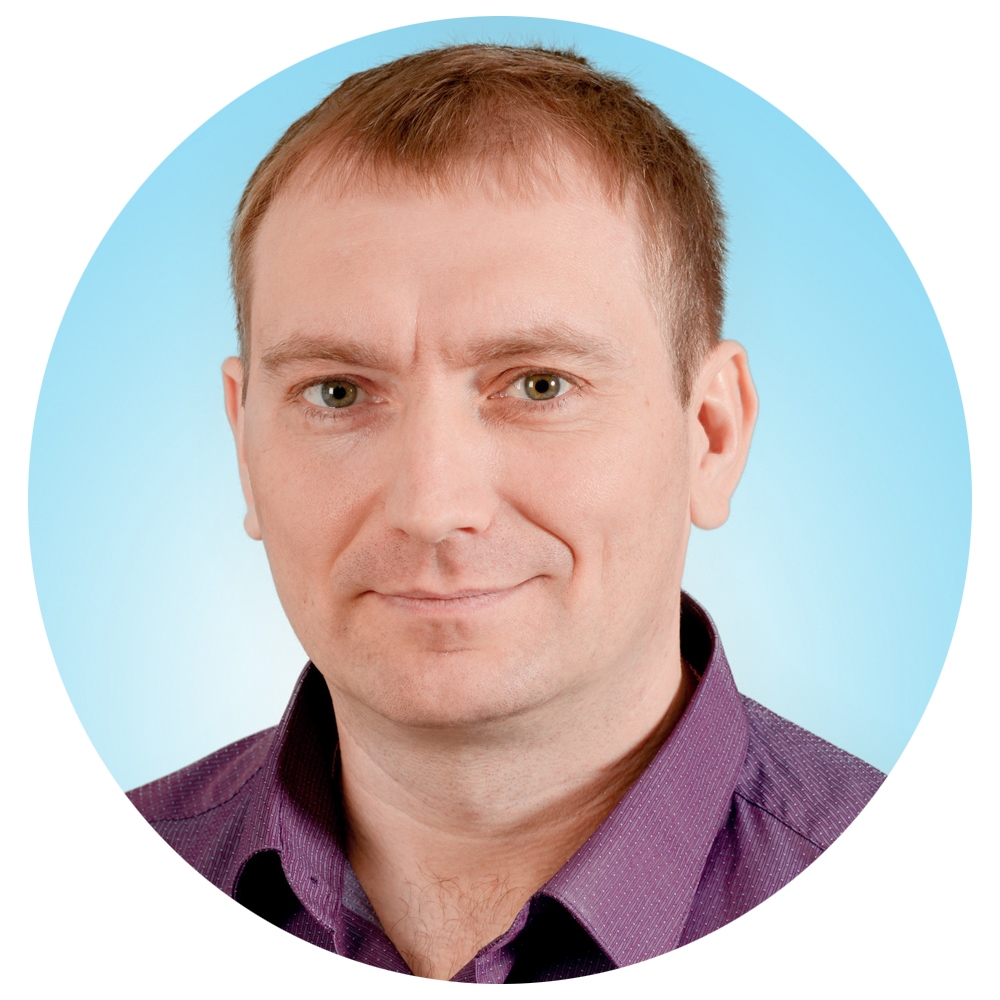
Главный эксперт службы главного энергетика Евгений Родин — рекордсмен по числу ППУ на заводе. Только за прошлый год он подал 86 предложений по улучшениям. Его конек — ремонт энергетического оборудования и экономия энергоресурсов.
«Мои предложения обычно распространяются в масштабах всего предприятия. В каждом цехе огромное количество оборудования, технологических систем и схем. Мне нравится размышлять над их работой и придумывать, какие изменения внести, чтобы сэкономить энергоресурсы или повысить производительность основной технологии», — говорит Евгений.
Одной из самых удачных своих идей за прошлый год он считает ППУ по изменению режимов работы насосного оборудования холодильных зданий и промышленной насосной станции. Проект был с нулевым бюджетом, все работы выполнил персонал подразделений. «Мы с коллегами поменяли гидравлический режим схемы подачи промышленной воды на предприятие и режимы подачи захоложенной воды к теплообменным аппаратам корпусов, — рассказывает Евгений Родин. — Техническими методами изменили производительность насосного оборудования и насосной станции. В результате мощность, потребляемая насосными агрегатами, сократилась на 200–300 кВт·ч. Если перевести в денежный эквивалент, то 500–700 рублей. Также мы снизили потребление промышленной воды, повысили надежность работы насосной станции, перекачивающей воду для завода, увеличили общую производительность станции. В условиях, когда бурно растут мощности основного технологического производства и заводу постоянно нужно много воды, это важное достижение».
Рацпредложения по экономии энергоресурсов завода Евгений Родин внедряет с 2013 года. Благодаря этим идеям ежегодно удается экономить не менее 60 млн рублей. «Изначально завод строился для другой технологии, газодиффузионные машины потребляли гораздо больше энергоресурсов, чем современные центрифуги, — объясняет Евгений. — У них другие режимы работы, отличаются температурные параметры. Но вспомогательное оборудование в основном осталось прежнее. Мы адаптируем его под новые реалии, инструменты ПСР нам в этом помогают».
КИЛОМЕТРЫ ПОРЯДКА
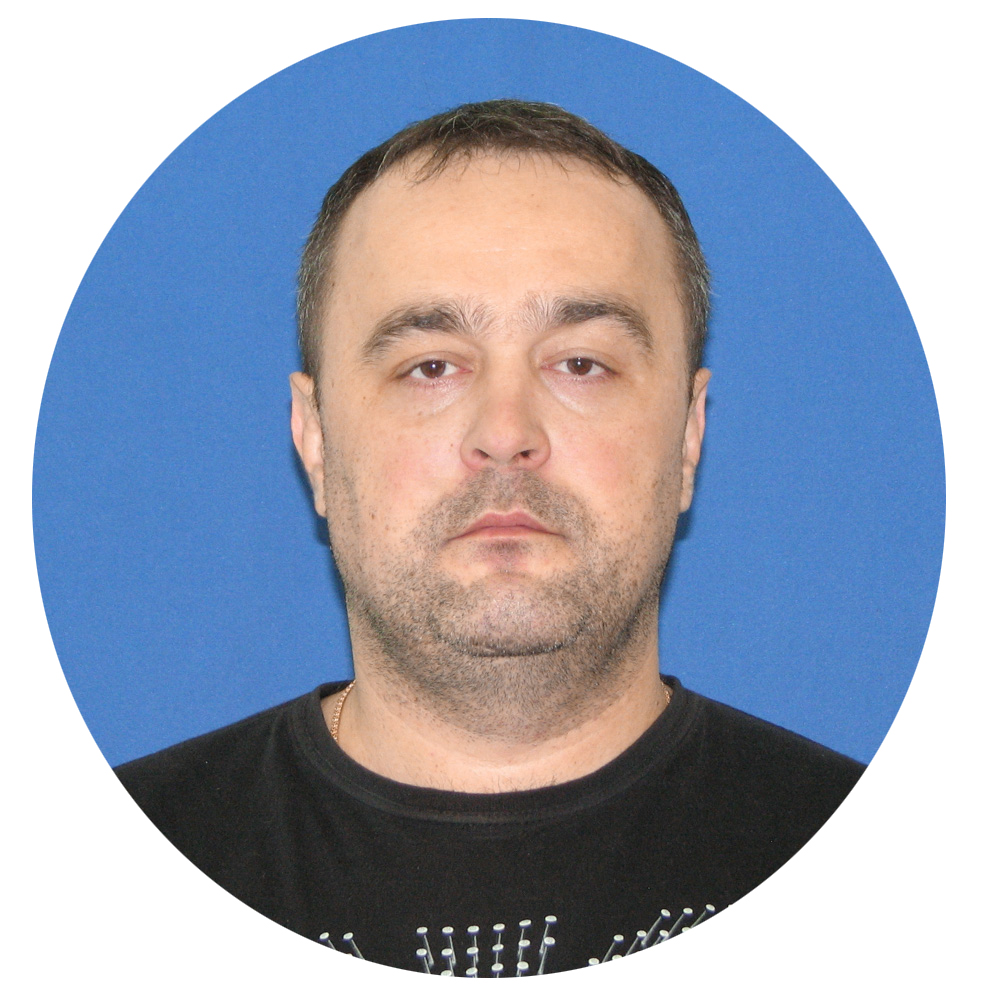
Малая группа, которой руководит инженер-технолог цеха обогащения урана Вячеслав Подосинин, заняла первое место в конкурсе завода по организации рабочего пространства по системе «5С». Коллектив набрал пять баллов из пяти возможных.
«Наш цех состоит из трех корпусов, каждый протяженностью почти километр, в одном из них работает наша малая группа, — рассказывает Вячеслав. — А это сотни регуляторов давления и подкачивающих компрессоров, тысячи датчиков, десятки тысяч клапанов. Мы обслуживаем километры трубопроводов и газовых центрифуг. Раньше оснастка, приборы и инструменты для проверки герметичности металлорукавов, которые необходимы для введения в эксплуатацию газовых центрифуг и других работ, были рассредоточены по разным участкам нашего корпуса. Часто аппаратчикам технологического участка приходилось метаться по разным местам в поисках оснастки».
В начале прошлого года коллектив Вячеслава Подосинина решил реорганизовать рабочий процесс. Инструменты, приборы и оснастку перенесли в одно помещение. «Сортировка, соблюдение порядка, содержание в чистоте, стандартизация, совершенствование, — перечисляет Вячеслав примененные принципы системы «5С». — Мы использовали метод теней, визуализацию, адресную маркировку. Определили минимум и максимум расходного материала, который должен быть в быстром доступе. Обозначили места хранения инструмента, электроприемников и приборов. Сюда же перенесли вакуумный пост для проверки на герметичность металлорукавов и клапанов небольших размеров. Время подготовки к любым работам на технологическом оборудовании сократили приблизительно на 20 минут. А время проверки металлорукавов на вакуумную плотность уменьшили в три раза».
ГИБРИДНЫЕ КЛАПАНЫ
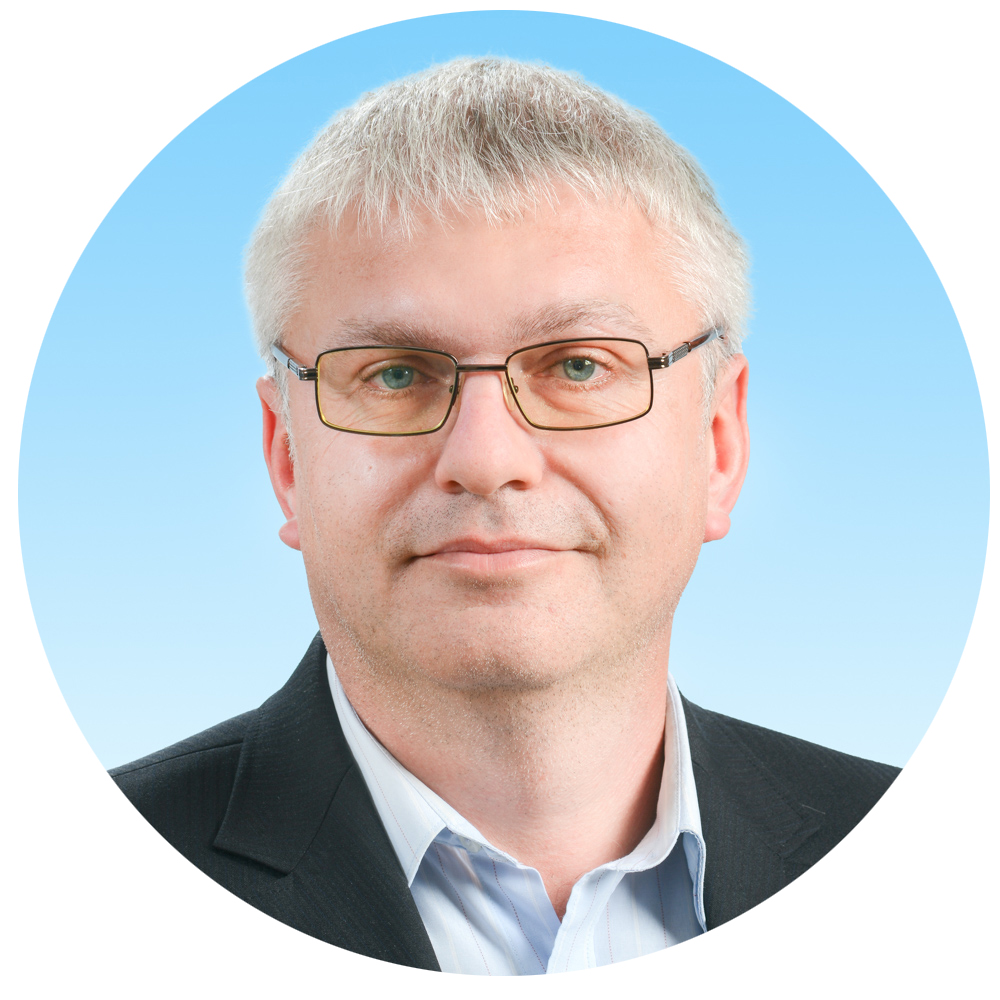
Инженермеханик службы главного механика Владислав Мустафаев — один из авторов самого прибыльного рацпредложения, внедренного на заводе в прошлом году. Его экономический эффект составил 19 млн рублей.
«Во время монтажа нового оборудования в цехах разделительного производства возник дефицит клапанов с нержавеющими сильфонами. Их корпуса после нескольких ремонтов выходили из строя. Приходилось утилизировать изделия целиком, несмотря на то что все остальные детали, кроме корпусов, были как новые, — рассказывает Владислав Мустафаев. — Мы решили скрестить их с другими клапанами, у которых корпуса были хорошие, а сильфоны плохие — латунные, ненадежные».
С советских времен на заводе остался большой запас клапанов с латунными сильфонами, их использовали в остановленном производстве. «Из двух клапанов с изъянами мы собрали один надежный, — продолжает Владислав. — Испытали пробный образец, он прекрасно себя зарекомендовал. Поняли, что надо запускать производство. Так у нас появился новый вид клапана. Теперь мы сможем закрыть потребность предприятия в клапанах на много лет вперед. И при этом ни копейки не потратить. Просто разбираем старые и делаем новые».
Этими устройствами на предприятии планируют заменить все старые клапаны. Модернизация займет несколько лет. Это позволит прилично сэкономить: новый клапан стоит порядка 75 тыс. рублей, в год предприятию требуется минимум 1 тыс. штук.