Изнанка 110-го шва
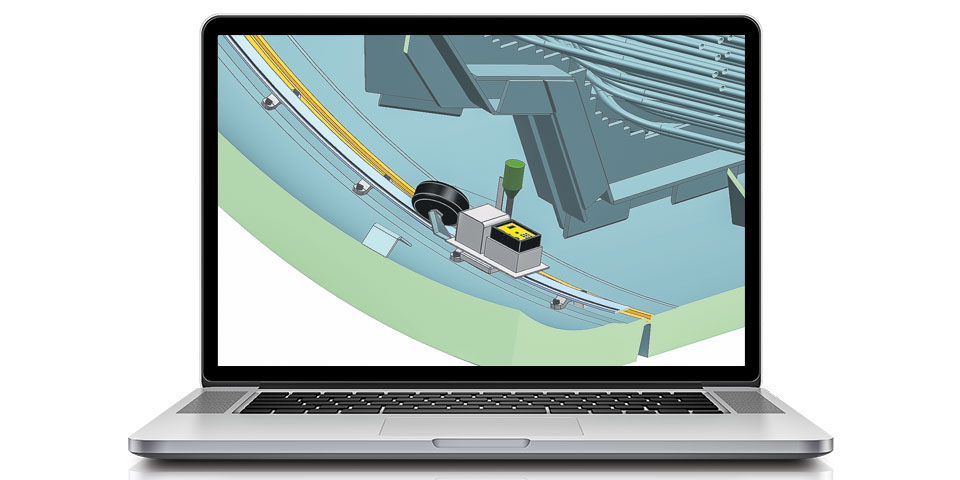
Алексей Романенко, инженер по сварке центральной сварочной лаборатории «Атоммаша», выиграл в конкурсе научно-исследовательских проектов «Умник», организованном Фондом по содействию инновациям. Молодой специалист рассказал «СР» о проекте, над которым работал последние три года и который должен значительно облегчить жизнь сварщикам.
Инженер разработал малогабаритный трактор для автоматической сварки под флюсом (специальным материалом, защищающим зону сварки от доступа кислорода). Устройство поможет оптимизировать процесс приварки днищ парогенераторов. До сих пор внутреннюю часть 110-го, замыкающего шва парогенератора варили вручную, теперь можно будет делать это автоматически.
«Забойный шов при приварке днища к корпусу парогенератора варят с двух сторон — снаружи идет автоматическая сварка под флюсом, изнутри сваривают вручную. Так как к этому моменту в парогенераторе уже размещены внутрикорпусные устройства, изнутри шов невозможно было заварить автоматической сваркой», — объясняет Алексей Романенко. При этом сварщику приходится работать в очень стесненных условиях, отдельные труднодоступные места варят лежа и практически вслепую. «Работа в таких условиях требует высочайшей квалификации и выносливости. На это способны единицы», — говорит изобретатель.
Механизировать сварку замыкающего шва парогенератора Алексей Романенко решил еще в 2015 году. «При ручной сварке по ГОСТу вероятность образования дефектов — до 10 %, это высокий показатель. Их выборка занимает время, а сложная работа в закрытом пространстве снижает производительность. Это приводит к денежным потерям. С коллегами решили попробовать автоматизировать процесс сварки, чтобы сократить дефектность, время и в целом повысить безопасность операции», — вспоминает Алексей Романенко.
Первым делом проконсультировались с опытными сотрудниками, работающими на заводе более 30 лет. «Оказалось, что попытки автоматизировать сварку 110-го шва уже были, но уровень технического развития тогда этого не позволял. Сейчас время другое, — говорит инженер. — Мы ни на шаг не ушли от классической технологии автоматической сварки под флюсом, просто смогли сделать миниатюрное устройство. Испытания проводили заводские сварщики-автоматчики, сложностей у них не возникло».
Неудачи приводят к победам
Стандартные сварочные тракторы имеют минимальные размеры 1×1×0,5 м. «Они в основном используются для сварки либо продольных швов, либо кольцевых швов крупногабаритных сосудов или обечаек диаметром до 10 м. Внутрь парогенератора в сборе такой попросту не поместится, слишком большой», — рассказывает Алексей Романенко. Поэтому нужно было уменьшать конструкцию. «Решили сделать трактор сами — 500 мм в длину, 250 в высоту, 200 в глубину. Компактная конструкция позволит варить в ограниченном объеме», — говорит инженер. Обычно, чтобы заварить швы в крупногабаритном оборудовании, в корпусе изделия приваривают рельсы, по которым передвигается сварочный трактор. «Любой дополнительный шов внутри ПГВ нежелателен — его нужно аттестовать, потом убирать и заново проверять основной металл. Это лишние трудозатраты», — объясняет Алексей Романенко. Поэтому его трактор ездит по рельсам, которые крепятся на магнитных прижимах.
Идею оформили, нарисовали эскизы и решили с этим проектом участвовать в конкурсе «Инновационный лидер атомной отрасли — 2015» в рамках молодежного форума «Форсаж». «Проект был сырой, мы едва успели подготовить презентацию, расчеты были приблизительные. Поэтому в финал не прошли», — вспоминает Алексей Романенко.
Весь следующий год молодой инженер совершенствовал свою разработку. Прототип трактора собирал из подручных средств, некоторые узлы переделывал десятки раз, а испытывал сварочный агрегат на макете парогенератора. «Я живу этим проектом, мне интересно его развивать», — подчеркивает Алексей Романенко.
На следующем «Форсаже», в 2016 году, он был уже во всеоружии — имел детальные расчеты и готовый макет. «На этот раз вышел в финал и победил. На выигранные деньги собрал рабочую модель самоходного трактора в железе со всеми ключевыми узлами. Сваренные швы успешно прошли все виды контроля», — гордится Алексей Романенко.
50 финалистов
Летом прошлого года Алексей Романенко решил участвовать в конкурсе научно-исследовательских проектов «Умник», организованном по инициативе общественного совета «Росатома» в Волгодонске. Конкурс направлен на поддержку коммерчески ориентированных проектов молодых исследователей (от 18 до 30 лет). Всего пять направлений: информационные технологии, медицина будущего, современные материалы и технологии их создания, новые приборы и аппаратные комплексы, биотехнологии. Для участия нужно было заполнить подробную анкету. Алексей Романенко рассказывает: «Почти три месяца ушло на заполнение, так как занимался этим в свободное от работы время, которого было не так много».
В октябре его пригласили представлять свой проект на отборочном этапе в Волгодонске, по итогам которого он получил шанс защитить свою разработку в финале конкурса. Проекты оценивали представители бизнес-сообщества, поэтому в презентации нужно было делать упор на конкурентоспособность и экономическую целесообразность разработки. На доработку презентации было меньше месяца — финал проходил 1 декабря в Ростове-на-Дону, но подготовить экономическую часть проекта Алексей Романенко успел.
В Ростов-на-Дону приехало много участников, 50 финалистов из разных городов, поэтому время на презентацию ограничили: пять минут на защиту. «Волнение, мандраж, голос срывался — все было, но я держался уверенно, помог опыт выступлений на «Форсаже». После выступления жюри рукоплескало. Поэтому свои шансы на победу оценивал высоко», — признается Алексей Романенко.
После экспертизы, 8 февраля, объявили победителей — авторов 34 проектов. Алексей Романенко получил грант — 500 тыс. рублей на два года. За это время он должен доработать изобретение и вывести его на рынок. Пока аналогов в России нет.
«Можно было обратиться к крупным производителям сварочного оборудования, чтобы они разработали для нас нечто подобное. Но тогда заводу пришлось бы оплачивать НИОКР, а это дорогое удовольствие», — говорит Алексей Романенко. Кстати, с помощью этого трактора можно варить швы не только парогенератора, но и других изделий. «Использовать наш мини-трактор можно при сварке оборудования не только для атомной отрасли, но и в нефтегазохимии, например», — отмечает Алексей Романенко. По его словам, внедрение на производстве миниатюрного трактора поможет «Атоммашу» в 2,5 раза снизить трудоемкость приварки днищ к корпусу парогенератора.
Как только трактор обкатают на «Атоммаше», его начнут использовать и на других предприятиях машиностроительного дивизиона. «Пока трактор проходит процедуру патентования. Но для развития проекта требуются дополнительные инвестиции. Выигранного гранта не хватит — нужно порядка 2 млн рублей. Также нужны люди, которые могли бы этим заниматься. Работы предстоит еще очень много», — заключает Алексей Романенко.
УМНИК ИЗ ВОЛГОДОНСКА
Алексей Романенко учился в волгодонском филиале МИФИ по специальности «оборудование и технологии сварочного производства», окончил вуз в 2013 году. «При выборе профессии особо не задумывался. Мой отец — сварщик с 30-летним стажем, он еще в советское время начинал строить первый блок Ростовской АЭС. Я пошел по стопам отца. Только он рабочий сварщик, а я решил стать инженером по сварке. Когда шел в институт, знал, что без работы не останусь, профессия востребованная», — рассказывает Алексей Романенко.
На пятом курсе участвовал в турнире молодых профессионалов, «ТеМПе‑2013». Решал актуальную на то время производственную задачу по сварке парогенераторов от «Атоммаша», дошел до финала с проектом по автоматической приварке косых патрубков к корпусу парогенератора. «Так я в боевых условиях познакомился с автоматической сваркой под флюсом», — говорит Алексей Романенко. Его заметили и пригласили работать на «Атоммаш».
Дипломный проект был связан с оборудованием для АЭС «Куданкулам». Защитился на отлично. Буквально через пять дней после защиты диплома уже вышел на работу. На заводе занимается входным контролем и испытаниями сварочных материалов. «Электроды, проволока, флюс обязательно должны пройти через центральную сварочную лабораторию, где мы проводим полный цикл испытаний. Качество и безопасность — наши главные приоритеты на заводе, — подчеркивает Алексей Романенко. — Поэтому сто раз перепроверяем».
Сейчас он участвует в «ТеМПе» как эксперт, разрабатывает производственные задания и приглашает талантливых участников работать на заводе.