Две тысячи лье по воде
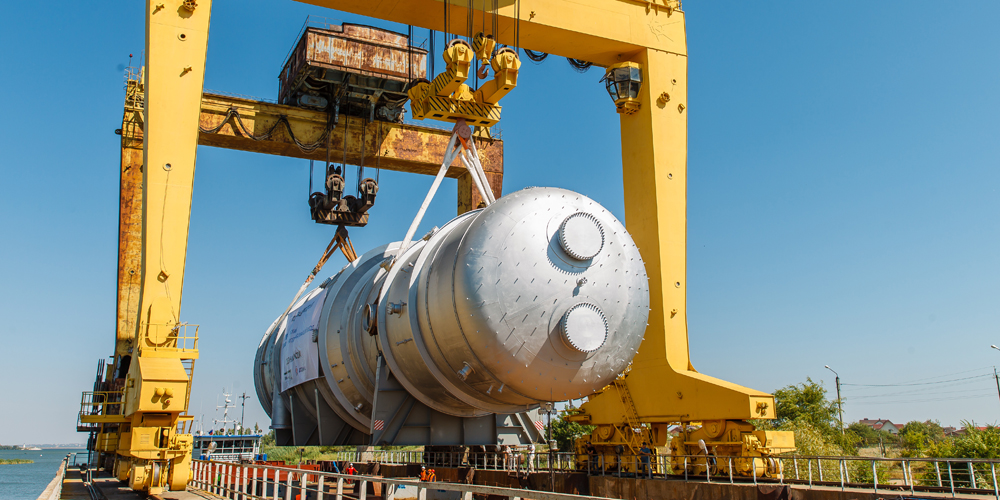
«Атомэнергомаш» сделал хет-трик в изготовлении оборудования для нефтепереработки. В конце июля с причала в Волгодонске по водному пути отправили новую колонну — в этот раз на Омский НПЗ. И хотя это уже третья отгрузка сверхгабарита за последние месяцы, событие вовсе не рядовое.
Сотрудничество «Атомэнергомаша» и «Газпромнефти» продолжается. Вакуумную и атмосферную колонны еще не успели смонтировать на Московском НПЗ, как в Волгодонске уже грузят на баржу новый супергабарит. Эта вакуумная колонна войдет в состав комплекса первичной переработки нефти Омского НПЗ, а именно установки атмосферно-вакуумной трубчатки, на которой обезвоживается и обессоливается нефть. Аппарат предназначен для разделения мазута на легкий вакуумный газойль, тяжелый вакуумный газойль и гудрон. После разделения в вакуумной колонне полученное сырье поступает на установки вторичной переработки нефти.
Колонны для перегонки нефти — сверхгабаритные устройства. Чтобы представить масштаб, их сравнивают ни много ни мало с ракетами-носителями. Вакуумная колонна «Атоммаша» для МНПЗ была уникальна по габаритам. Нынешняя, для ОНПЗ, немногим меньше (длина — 52 м, диаметр — 11 м), но самая тяжелая — 518 т. Это в 1,5 раза больше, чем вес корпуса реактора ВВЭР-1200.
Чтобы доставить эту махину от производственной площадки до Цимлянского водохранилища, временно демонтировали троллейбусные провода и даже линии электропередачи в Волгодонске. Передвигались только ночью — таковы требования безопасности дорожного движения. Водный маршрут следования грузового состава включает Волго-Донской канал, Волгу, Белое море, далее Северный морской путь, а затем — реки Обь и Иртыш. Общая протяженность пути превысит 12 тыс. км — почти диаметр Земли. С учетом значи тельных весогабаритных характеристик колонны «Атоммашу» пришлось задействовать при ее производстве все свои технологические и инфраструктурные возможности. Отдельный разговор — это сварка. Например, сварка кольцевых швов изделия диаметром более 8 м требует автоматизации — таковы стандарты. Но традиционными консольными установками такую колонну не сварить. Есть альтернатива — самоходный сварочный трактор.
Но предназначен он для сварки продольных швов, а не кольцевых. И чтобы его применить, нужно было синхронизировать скорость вращения колес трактора и ведущих роликов установки, крутящей само изделие. Пришлось изобретать синхронизатор скоростей. Специалисты «Атоммаша» закрепили синхронизатор на тракторе и подключили его к пульту управления роликоопорой. В результате сварка и наплавка кольцевого шва идут с постоянной скоростью, благодаря чему в три раза выросла производительность процесса, повысилось качество сварки швов и наплавок.
С другим вызовом «Атоммаш» столкнулся при термообработке днища колонны. Деталь не проходила в печь ни стоя, ни лежа. Специалисты придумали сложную оснастку высотой с трехэтажный дом, поддерживающую днище под определенным углом.
Всего изготовление колонны заняло 21 месяц, производственный процесс насчитывал 850 этапов. Только для сварочных работ было использовано около 40 т электродов и проволоки, а общая длина сварочных швов составила 2 км. Колонна прошла ультразвуковой и радиографический контроль, а также проверку передовым дифракционно-временным методом (TOFD). В проекте в качестве инженера-технолога участвовал и чемпион WorldSkills Hi-Tech — 2015 Александр Дуймамет. «Мы принимали море технических решений, чтобы проводить все операции на одном заводе. Объем работ настолько большой, что работали круглосуточно, в несколько смен,— комментирует он.— Работа была интересной, требовала высокой квалификации, быстрых решений. Сложной была плакирующая наплавка — нержавеющий слой. Не могу сказать, что это супертрудно и мы таким не занимались. Но вот в таком объеме… Тут же километры швов!»