«Атомэнергомаш» готов делиться опытом
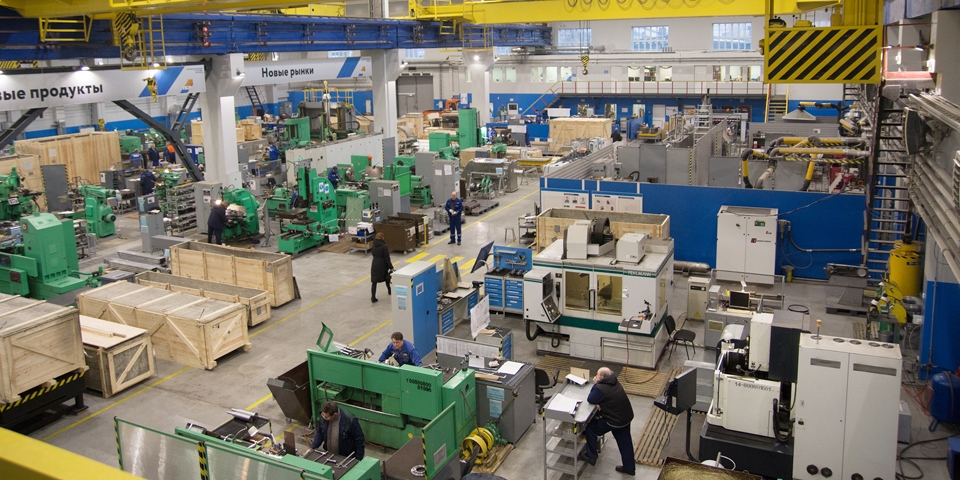
Атомное машиностроение меняет конфигурацию: производственные площадки получают специализацию, площади высвобождаются. Растет эффективность, сокращаются сроки производства основного оборудования. Теперь опыт дивизиона хотят перенять и другие отрасли.
Яркий пример успешной реконфигурации — питерское Центральное конструкторское бюро машиностроения (ЦКБМ). Это единственный в России разработчик и изготовитель главных циркуляционных насосов для всех типов отечественных реакторов. Среди прочего предприятие владело огромным, 57 тыс. м², комплексом возле Охты: здания удалены друг от друга, площадь избыточна. Первый заместитель гендиректора по стратегии и организационному развитию «Атомэнергомаша» Ксения Сухотина рассказывает, что в 2014 году было принято решение о релокации ЦКБМ. Уже через полтора года сотрудники переехали в новый офис (5 тыс. м²) на набережной Обводного канала. Производство частично перенесли на площадку ЦКБМ в Сосновом Бору, частично — на Кировский завод, где у ЦКБМ тоже своя площадка. В результате снизились постоянные затраты на коммунальные услуги, ремонты и налоги, сократились потери в технологических и транспортных потоках, а также запасы на переделах. Производственные потоки были выстроены в соответствии с требованиями ПСР и лучшей мировой практикой. «В Boeing есть система визуального контроля: руководители наблюдают за производством прямо из своих кабинетов. Мы пошли по их стопам — построили в новом цеху антресоли с кабинетами. Начальник смены постоянно видит, что происходит в цеху», — рассказывает директор департамента управления персоналом «Атомэнергомаша» Сергей Бедниченко (до недавнего времени — первый заместитель гендиректора ЦКБМ). Рабочие других предприятий, расположенных на территории Кировского завода, ходили в новый цех как в музей — посмотреть, говорили даже, что не прочь перейти в ЦКБМ.
В новый цех перевезли 37 станков с Охты. «Чтобы их расставить в производственном потоке, мы советовались с японскими консультантами. Вырезали имитации из картона и раскладывали на полу», — рассказывает Сергей Бедниченко. Работать стало гораздо удобнее. «Станки стоят в логичной последовательности. В старом цеху где место находили, там станок и втыкали», — вспоминает токарь Михаил Кибирев.
Улучшились и условия труда. «В старом цеху зимой было холодно, летом — жарко. А сейчас круглый год комфортно», — отмечает оператор склада Светлана Кукуева. «Раньше от сварки постоянно помещение задымлялось. Теперь работать одно удовольствие — есть климатконтроль, вытяжные системы. С внедрением ПСР стало меньше беготни: все под рукой», — рассказывает сварщик шестого разряда Евгений Альбин.
По итогам 2015 года уровень вовлеченности персонала в ЦКБМ достиг 80 %. Значит, сотрудники восприняли изменения в целом позитивно. В апреле этого года предприятие получило статус «Лидер ПСР». На 2017–2018 годы намечена модернизация оборудования. «Монтаж начнется в мае — без остановки производства», — говорит начальник цеха Андрей Васильев. И добавляет: удалось даже нарастить производственные мощности — организовать линию по сборке уран-плутониевых твэлов для реактора БРЕСТ ОД-300. Заказов сейчас столько, что цех работает в три смены.
Пример ЦКБМ — только часть большой программы. За последние годы АЭМ освободил 650 тыс. м² земель и зданий. Три промплощадки компактизированы и изменили локацию, в частности, произошло объединение «ЦНИИТмаша» и ВНИИАМ. Общая выручка от компактизации за 2012–2016 годы составила 4,1 млрд рублей, а производительность труда за этот период выросла на 54 % — до 3,7 млн рублей на человека. Cократились сроки изготовления оборудования: парогенераторов — с 877 до 488 дней, выемной части ГЦНА — со 126 до 113 дней. А проекты АЭМ по реконфигурации уже готовы использовать в других отраслях.
ПРЯМАЯ РЕЧЬ
Илья Тарасенко
Генеральный директор «МиГа»
— В условиях жесткой конкуренции с иностранными авиастроителями перед нашей корпорацией стоят масштабные задачи по повышению эффективности, сокращению временных издержек, поддержанию конкурентоспособной себестоимости производства. В этой связи мы внимательно изучаем лучшие практики в сфере организации производственных процессов, в том числе в других отраслях. Опыт «Росатома», в частности машиностроительного дивизиона, представляется нам достаточно востребованным и возможным для внедрения в нашем производственно-конструкторском комплексе.