«Старт» показал, как сделать невозможное
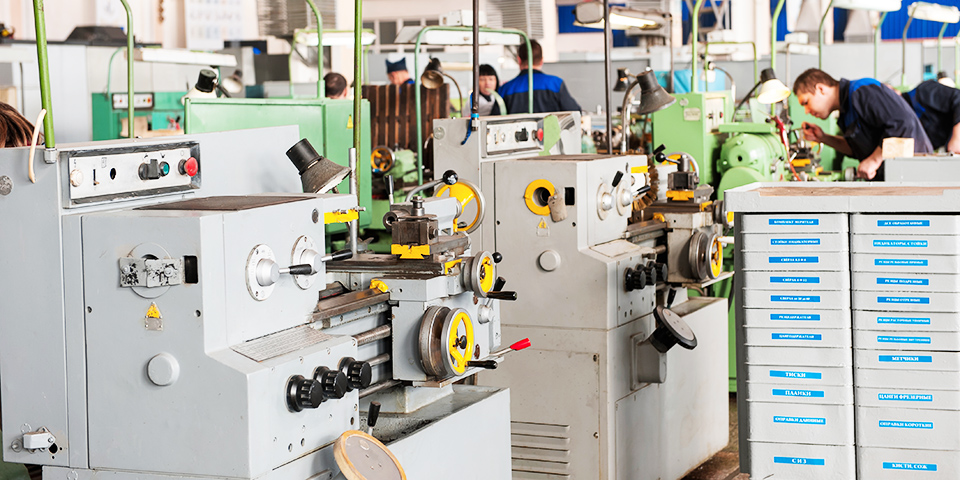
В основе любой системы бережливого производства заложен принцип постоянных изменений и совершенствования производственных процессов. Однако четкие правила, следуя которым можно и горы свернуть, несовместимы с консервативным настроем и отжившими свое схемами. Каких результатов можно добиться, просто кое-что изменив, увидел журналист «СР» в одном из цехов ПО «Старт».
В прошлом году на ПО «Старт» были выстроены три образцовых потока производства и несколько вспомогательных ПСР-проектов. Мне давно хотелось увидеть, как применяют инструменты производственной системы в ЯОК, но в цеха закрытых предприятий журналистов приглашают редко. К счастью, мне такая возможность представилась: на «Старте» проходило заседание управляющего совета «Комплексная оптимизация производства предприятий атомной отрасли». Перед совещанием директора предприятий дивизиона во главе с гендиректором «Росатома» Сергеем Кириенко проинспектировали четыре площадки. Мне удалось побывать только в одном цеху – механическом. Секретность, ничего не поделаешь.
По словам главы ядерного оружейного комплекса Ивана Каменских, за время развертывания производственной системы на «Старте» произошли масштабные преобразования: «Вспоминаю 2000 год, когда я приехал сюда впервые. Грустно было смотреть. Работы практически нет, зарплата маленькая. Но все изменилось: появились такие объемы производства, с которыми простыми методами не справиться. Выстроив поток единичных изделий, стали делать то, что раньше казалось невозможным».
Новый поток
У механического цеха № 7 огромная номенклатура, решить все проблемы сразу невозможно. Решили начать с насущного. Сотрудник АО «ПСР» Сергей Думчев обстоятельно рассказал мне историю одного эксперимента. Нужно было разобраться с несвоевременной поставкой волноводов. Из-за них вставало все сборочное производство. «Сначала, конечно, в цеху пробовали справиться своими силами, но не получилось, — рассказывает он. — Мы предложили помощь. Первым делом собрали рабочую группу: технологов, фрезеровщиков, слесарей, паяльщиков». Начали с постановки задач: повышение качества и снижение незавершенного производства, времени протекания процесса, трудоемкости. Проанализировали ситуацию. Выходила такая картина: производство деталей волноводов разбросано по всему периметру немаленького цеха, рабочие за день наматывают не один километр, а это потеря времени. Обрабатывать много заготовок при такой организации труда невыгодно. Количество задействованных рабочих постоянно варьировалось — от четырех до 10 человек разных специальностей: фрезеровщик, слесарь, шлифовщик, пайщик, что нарушало производственный ритм.
Специалисты по ПСР организовали производственную ячейку, расставили по-другому оборудование и разбили заказ на 300 заготовок на партии по 20 штук. Составили карту потока производства, проанализировали каждую операцию, выявили и устранили потери. При этом трудозатраты на каждую операцию в работе фрезеровщика и слесаря снизились.
На участке производства деталей волнореза по ПСР за четыре месяца объем НЗП в потоке снизился в два раза, трудоемкость на одну деталь — с 9,8 нормо-часа до 7,6, а время протекания процесса почти в два раза – с 4,46 дня до 2,74 дня.
Так как по трудоемкости все операции разные, ввели понятие «время такта» – темп, с которым человек работает. Построили график загрузки. Стало видно, кто часто простаивает, а кто не отходит от станка. На основе этого графика перераспределили нагрузку: если у фрезеровщика окно, он берет слесарную работу (об этом ниже). «Теперь весь поток подчинен единому темпу, производительность труда на участке стала максимальной. Раньше могли выпускать не больше 60 изделий в день, сейчас — 100 и даже 150, в зависимости от заказа», — поясняет руководитель рабочей группы начальник смены, старший мастер механического цеха №7 Николай Рожков. На стенде повесили подробный план на сутки и смену: что нужно каждому сделать, в какой последовательности и в каком количестве. Тут же начальник смены проводит анализ и контролирует выполнение работы. Если раньше партия сначала обрабатывалась, а через несколько дней объявляли, что был брак, сейчас это говорят сразу, так как партии теперь небольшие и выявить изъян можно при передаче заказа в цех сборки, не дожидаясь конца рабочего дня.
Бригада!
Шесть человек – оптимальное количество сменщиков, нужно только сбалансировать нагрузку. «Традиционно как? – улыбается Николай Рожков. — Токарь только точит, фрезеровщик только фрезерует. Мы доучили рабочих, чтобы никто не простаивал. Скажем, фрезеровщик-слесарь полностью осуществляет фрезерную операцию и в промежутках выполняет слесарную обработку». Организовали буферы деталей — расположили заготовки в одном месте, чтобы они были всегда под рукой, НЗП было минимальным, а производственный поток не останавливался и двигался максимально плавно.
Важным фактором стала материальная мотивация. На участке применили бригадную форму оплаты труда. Если раньше каждый получал деньги в соответствии со своей ставкой и ни от кого не зависел, то сейчас на всю бригаду выписывается общая сумма, которая делится в зависимости от вклада каждого, по определенному коэффициенту. Так как работа сдельная, за счет выросшего темпа и увеличения объема производства, зарплата выходит больше. Появился стимул, и теперь сослуживцы выравнивают работу друг друга, чтобы не терять деньги. «Однако этот принцип применим не везде. Где-то производство организовано не так, и люди не готовы к изменению формы оплаты труда. Нет универсального решения», — разводит руками Николай Рожков.
Главное — втянуться
Сергей Думчев говорит: «Нам нужно было не просто предложить решение и уйти на другой участок. Завтра же все развалится из-за того, что никто не понял технологию. Нужно было обучить людей, дать им попробовать инструменты ПСР, чтобы они увидели разницу».
В 2016 году план по изготовлению деталей волнореза изменился. Исходя из этого, в цеху самостоятельно модернизируют ячейку — регулируют количество, расстановку и загрузку рабочих в смене. В ближайшее время на участок добавят токарный станок под еще одну деталь.
ПСР-предприятия 2016 года
Лидеры ПСР
1. КМЗ
2. Балаковская АЭС
3. УЭХК
4. ОКБМ
5. Смоленская АЭС
6.«Старт»
7. МСЗ
Кандидаты ПСР
1. ИРМ
2. ЦКБМ
3. «РосСЭМ»
4. НЗХК
5. СХК
6. ЧМЗ
7. НПО «Луч»
8. НИАЭП
9. Ленинградская АЭС
10. «Электрохимприбор»
11. ЭХЗ
12. «Атоммаш»
13. «Радон»
ПСР для обычных людей
Следить за тем, как развивается производственная система целой отрасли, очень увлекательно. Конечно, самое главное происходит в цехах и офисах, но дискуссии о настоящем и будущем ПСР тоже познавательные. На февральском заседании управляющего совета одной из центральных тем стало отношение к изменениям рядовых сотрудников.
10 предприятий к концу прошлого года должны были стать образцовыми с точки зрения основного производственного потока. Но десятка пилотов превратилась в семерку лидеров ПСР – три предприятия до этого статуса недотянули, хоть и были уверены в победе до последнего. Решающим стал фактор вовлеченности. В лидеры вышли те, у кого минимум половина персонала поддерживает принципы бережливого производства. В 2016 году планка поднимется – не менее 75 % сторонников ПСР, и работа с людьми выдвинется на первый план.
Лидер ПСР не просто красивое название. Те, кто занял первые три места в рейтинге, получают по 10 млн рублей на развитие производственной системы. Всем семи предприятиям вручили пакет привилегий: бизнес-тренинги, командировки по обмену опытом на российские и зарубежные предприятия, семейные путевки, сертификаты Корпоративной академии и так далее. На всех, конечно, не хватит, но лиха беда начало.
Ни для кого не секрет, что на местах от новой политики не в восторге – по разным причинам. Некоторые считают, что ПСР – это такой способ уволить людей. Логика вроде понятная: производительность труда растет, рабочих рук нужно меньше. Но это если портфель заказов неизменный, а это не наша история: рост объемов — задача каждого предприятия. Вспомним, что сохранить конкурентные преимущества можно только через повышение эффективности производства.
Скептики меняют свое мнение после того, как пробуют инструменты ПСР на практике и получают первые результаты. Те, кто сопротивлялся системе, становятся ее приверженцами, проводниками. Таких примеров немало.
Мотивировать на «взять и попробовать» можно, если каждый сотрудник будет четко понимать, к чему это приведет и к чему вообще стремится его предприятие. На «Старте» на многих участках висят стенды с целями. Цели разбиты на этапы, результат которых выражен в цифрах. Если благодаря предложению по улучшению удалось сэкономить столько-то, ясно, сколько пойдет на премию, сколько на улучшение условий труда и на социальные блага.
Еще нюанс. Изменение культуры производства не может произойти по команде. Важен личный пример руководителя. Следующую десятку претендентов на звание ПСР-предприятия выбирали по этому критерию: готов ли гендиректор стать лидером внедрения производственной системы и повести за собой людей.
Одного дня руководителям отрасли не хватило, чтобы обсудить все аспекты развития ПСР. Дискуссия продолжится в конце марта на ежегодном совещании топ-менеджеров «Росатома».