«Атомэнергомаш» внедрил новую систему мониторинга оборудования
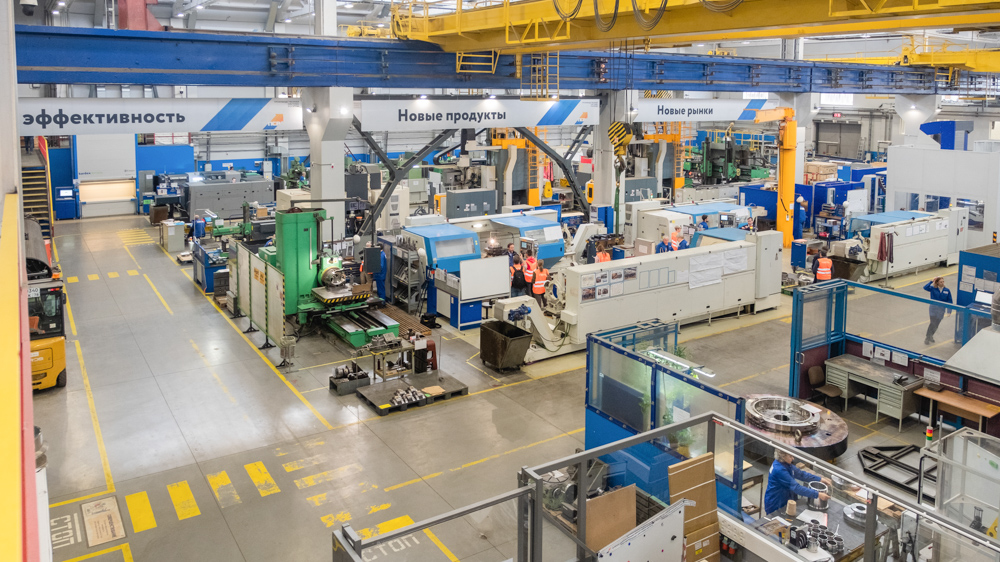
«Атомэнергомаш» представил результаты первых девяти месяцев работы системы мониторинга производственного оборудования. Построенная на базе российской АИС «Диспетчер» и адаптированная под запросы предприятий дивизиона система собирает данные со станков — пока чтобы увеличить производительность. Но потенциал у ИТ-комплекса гораздо больше.
В опытно-промышленную эксплуатацию систему ввели в декабре прошлого года. Первый месяц собирали и анализировали данные. С января начали постепенно менять производственные процессы. Сегодня к системе подключены 407 станков на семи площадках «Атомэнергомаша». Лидирует во внедрении Центральное конструкторское бюро машиностроения — 130 станков на Кировском заводе и в филиале в Сосновом Бору. «Мы должны быть в курсе, что происходит с оборудованием и изделием каждую минуту», — говорит первый заместитель гендиректора, директор по производству ЦКБМ Алексей Кузьмин.
Подход к станку
Раньше на каждом участке секундомером замеряли, сколько времени уходит на ту или иную операцию. Сбор данных явно нуждался в автоматизации. ЦКБМ начал тестировать оборудование и софт российских и зарубежных производителей еще три года назад, но затраты на установку оказались слишком велики.
Два года назад ИТ-компания «Цифра» и фонд «Сколково» предложили «Атомэнергомашу» поучаствовать в пилотном проекте федеральной программы по внедрению отечественных аппаратно-программных комплексов при софинансировании государства. «Удачно совпала наша стратегия цифровизации и государственная инициатива», — отмечает заместитель гендиректора, директор по экономике и финансам «Атомэнергомаша» Сергей Бондаренко.
«Атомэнергомаш» открыл дивизиональный проект и предложил своим предприятиям протестировать продукт «Цифры». «Мы сравнили «Диспетчер» с другими АИС по удобству, функционалу и возможностям интеграции в информационные системы предприятия и согласились, что это самое интересное решение», — рассказывает Алексей Кузьмин. В ходе внедрения «Диспетчер» модифицировали под запросы предприятий дивизиона, так что в итоге его стали называть системой мониторинга производственного оборудования — СМПО.
Покупку программного обеспечения и оборудования, монтаж, организацию обучения персонала и проч. взял на себя «Атомэнергомаш». Инвестиции составили 195 млн рублей, из них 95 млн — грант Минцифры. Предприятия вложились трудозатратами: на ЦКБМ, например, на внедрение СМПО уходило до четверти рабочего времени управленцев-производственников.
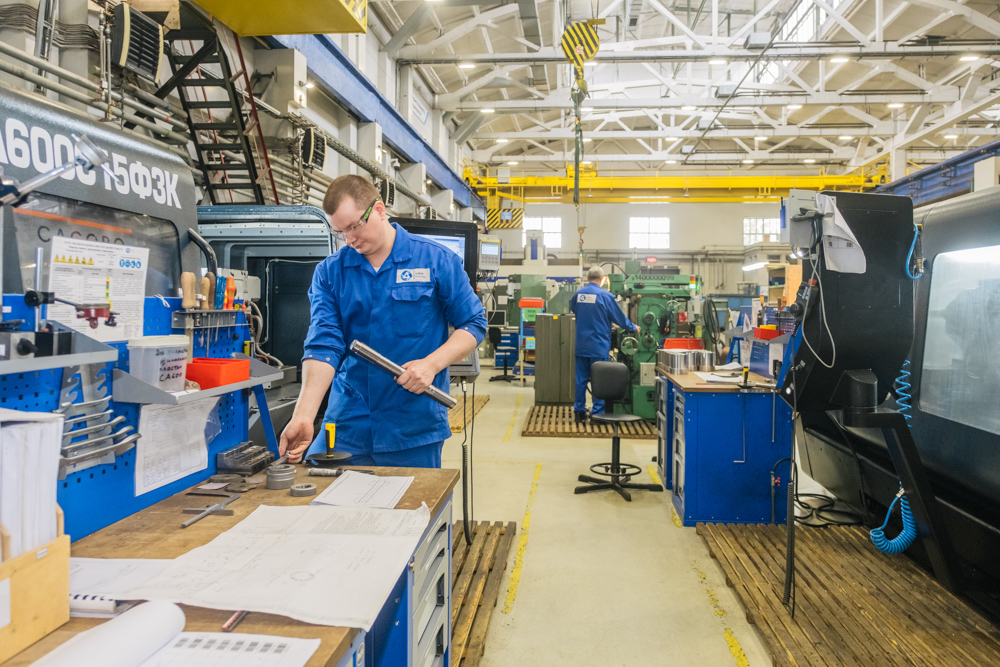
Как это работает
На станки установили терминалы ввода-вывода информации и минимальный набор датчиков (станки с ЧПУ часть параметров фиксируют самостоятельно). Некоторые станки по запросу производственников оснастили специализированными датчиками. Весь аппаратный комплекс подключили к СМПО.
С датчиков в систему поступают первичные данные: включен ли станок, обрабатывает ли деталь, какая это деталь, сколько времени проходит между включением и началом обработки. В терминалы операторы вводят причины простоев и проч.
На станки поставили колонки-«светофоры», как на кассах в супермаркете. Сигналы переключаются по команде с СМПО: зеленый — все в порядке, желтый — требуется внимание оператора, красный — аварийная остановка. Операторы, которые обслуживают несколько станков, контролируют положение, просто окидывая взглядом участок.
Программно-аппаратные комплексы переданы предприятиям в аренду. ЦКБМ, например, платит 650 тыс. рублей в месяц.
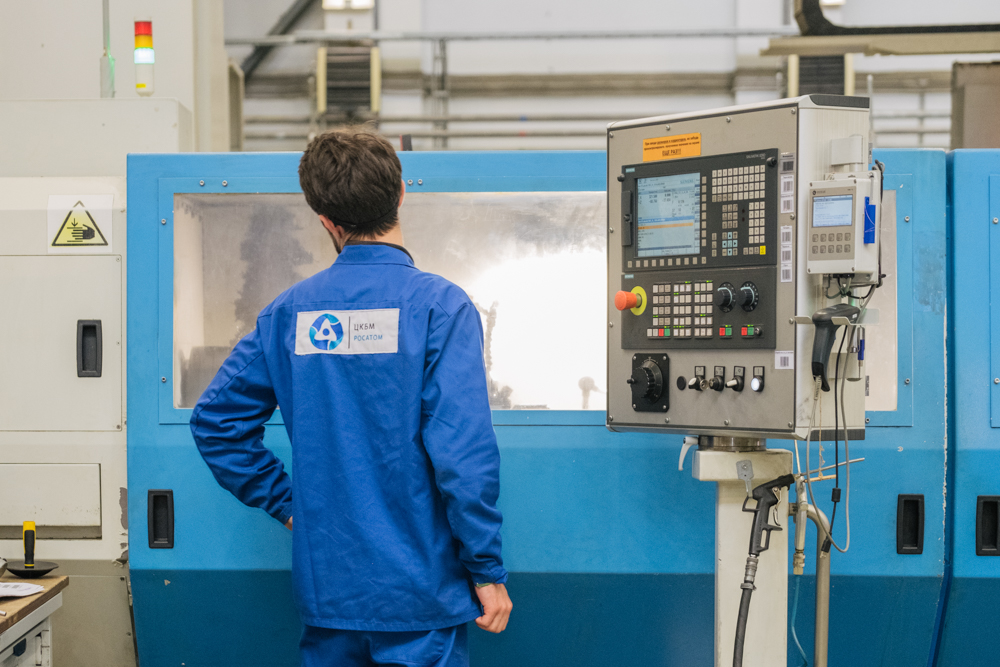
Первые результаты
Простои типа «ожидание» стали управляемыми. Например, на ЦКБМ в одном цеху станков много, а кранов, которые перемещают заготовки, всего два. Циклы изготовления деталей скорректировали, чтобы рабочим не приходилось долго ждать следующую партию.
Ускорилась реакция на аварии. Раньше было так: оператор сначала пытается сам понять, что произошло (иногда многостаночник отключает для этого остальные свои станки), потом вызывает мастера, тот — главного механика, слесаря. В общей сложности поиски занимали около 25 минут. С внедрением СМПО время реагирования сократилось на порядок. Оператор сообщает об аварии через систему, которая отправляет оповещения на рабочие места сотрудников и мобильные устройства. Ремонтом сразу занимаются профильные сотрудники, и оператор не отвлекается.
Еще один эффект — рост культуры производства. «Если на первых порах у рабочих было ощущение, что за ними следят и поэтому надо быть аккуратными, то сейчас они не просто работают аккуратно, но и относятся к системе как к партнеру, который передает объективную информацию о том, что происходит на участке», — говорит Сергей Бондаренко.
В терминал оператор вводит причину простоя: подготовка к обработке, ожидание новой заготовки, поломка и т. д. Раньше причину указывали постфактум, из объективных данных был только объем производства. «Теперь в ЦКБМ еженедельно автоматически формируются отчеты по каждому цеху, станку и сотруднику. Обозначены все ключевые показатели, а у простоев зафиксированы «фамилия», причины и время. На мониторы в цехах транслируется информация о состоянии оборудования. Таким образом, вся цепочка выполнения работ стала прозрачной», — комментирует гендиректор ЦКБМ Игорь Бурцев.
В бюро внедрили систему оперативного премирования, привязали премию к производительности, которую отслеживает система мониторинга. Рабочие видят, как растет их производительность, а вслед за ней и премия, так что выгоду получило и предприятие, и люди. «Мы сейчас все успеваем и контролируем, от этого и премия зависит», — подтверждает оператор станков с программным управлением 4‑го разряда Юрий Васильев.
«На участке обработки деталей из силицированного графита мы увеличили загрузку оборудования с 40 до 67 % и ушли от сверхурочной работы и работы в выходные дни», — рассказывает начальник цеха Роман Сапилкин. На ЦКБМ подсчитали, что с СМПО по итогам года загрузка ключевого оборудования вырастет на 7 %.
В целом по «Атомэнергомашу» эффект от внедрения системы мониторинга и улучшения производственных процессов в этом году предварительно оценивают примерно в 80 млн рублей.
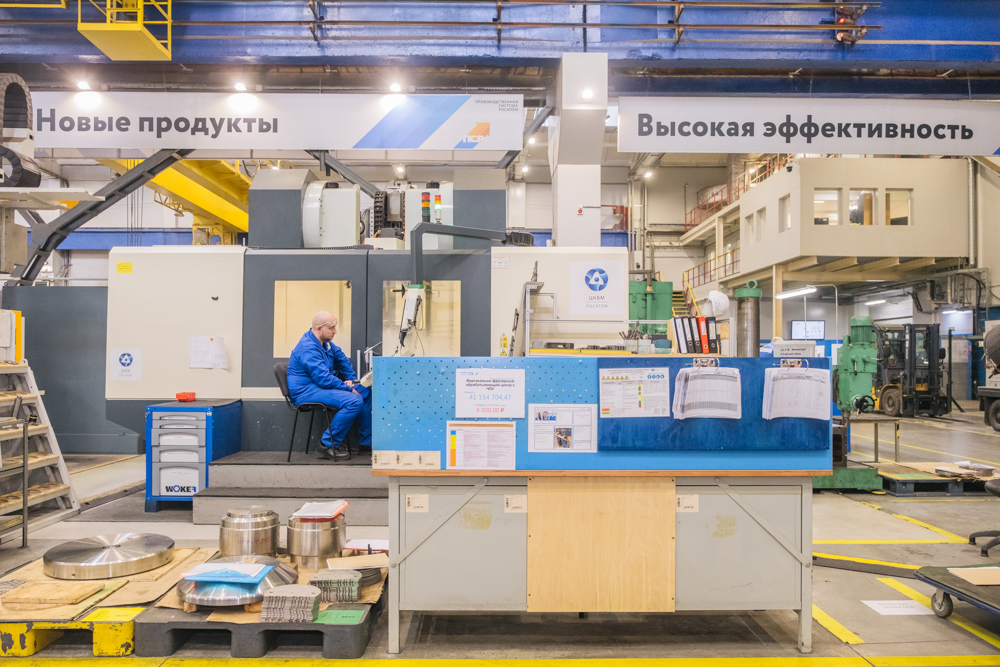
Новые мысли о данных
Сфера применение данных СМПО может и должна расшириться. Во-первых, эта информация нужна в предиктивной аналитике для подбора оптимального режима работы станков, чтобы минимизировать вероятность выхода из строя. Во-вторых, можно автоматически формировать паспорт изделия и передавать его в информационные системы полного жизненного цикла. В-третьих, можно совместить СМПО с системой видеонаблюдения для профилактики нарушения техники безопасности. Например, камера распознает человека в зоне действия крана и отправит сигнал в систему, а та — предупреждение человеку.
Следующая перспективная область — исследование эксплуатационных свойств изделий, обработанных в том или ином режиме. «Условно технология допускает обработку при скорости вращения шпинделя токарного или фрезерного станка в диапазоне 2–3 тыс. оборотов в минуту. Но на каких оборотах деталь получается лучшего качества — на 2,2 тыс. или 2,8 тыс.? На каких оборотах двигатель не греется? Влияет ли количество оборотов на время, за которое деталь будет обработана должным образом, и насколько значительно? И это далеко не все вопросы, которые можно задать», — поясняет руководитель направления департамента цифровизации и информационных технологий «Атомэнергомаша» Андрей Тимошин.
Наконец, возможно, главное приложение данных — более точное планирование в рамках дивизиона. Например, информация о загрузке — ценные сведения для коммерческого отдела, который будет понимать, какой дополнительный объем сможет пропускать через себя оборудование.
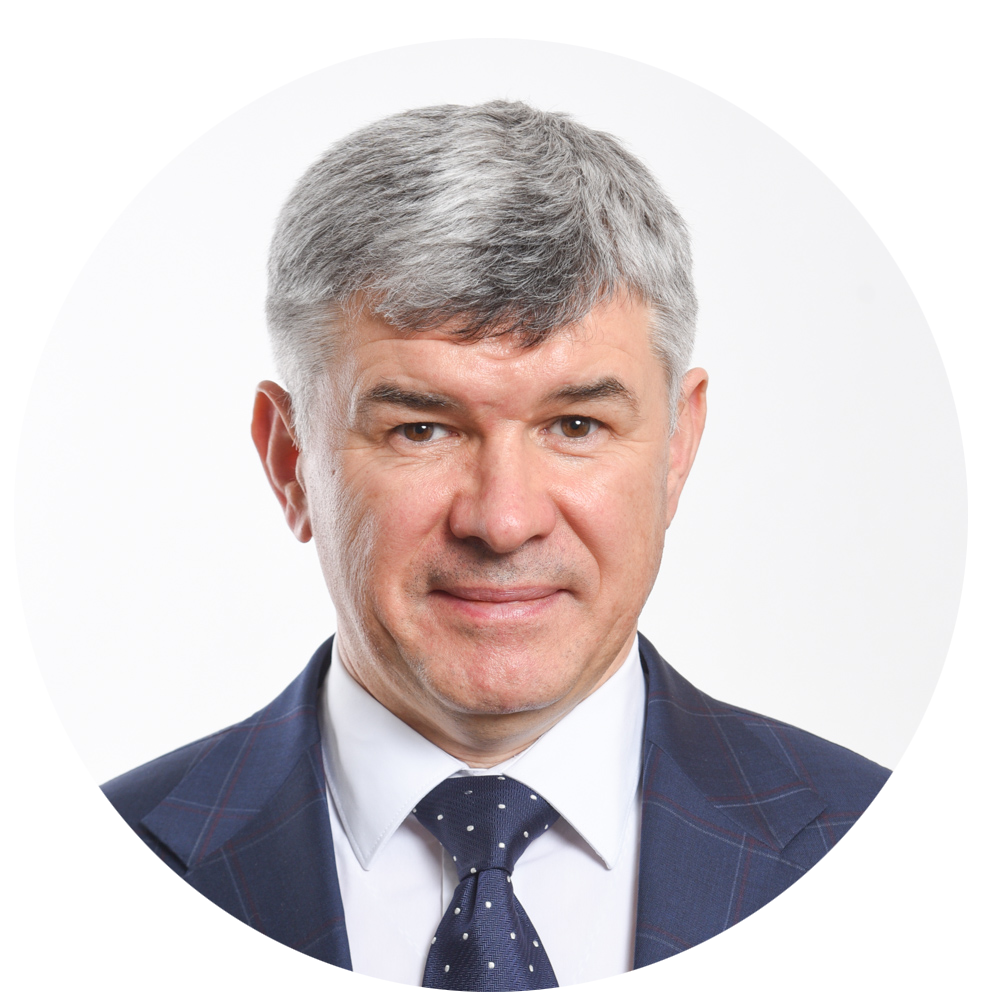
Андрей Никипелов
Гендиректор «Атомэнергомаша»
— Цифровизация предприятий для нас не самоцель. Цифровая инфраструктура — базовая вещь для планирования, которое задает такт работе производств. Закупочные службы, получая задания из производственного плана, должны обеспечить бесперебойное снабжение, конструкторы и технологи — выдавать вовремя проектную и рабочую документацию, эйчары — обучать и нанимать нужное количество сотрудников определенной специальности и квалификации и т. д. Но выполнение задач требует грамотного планирования не только на уровне дивизиона или предприятия, но и на уровне каждого ключевого станка. В этом нам помогает СМПО, поэтому мы будем расширять ее использование.