Обвести вокруг байка: композиты «Росатома» нашли применение в спорте
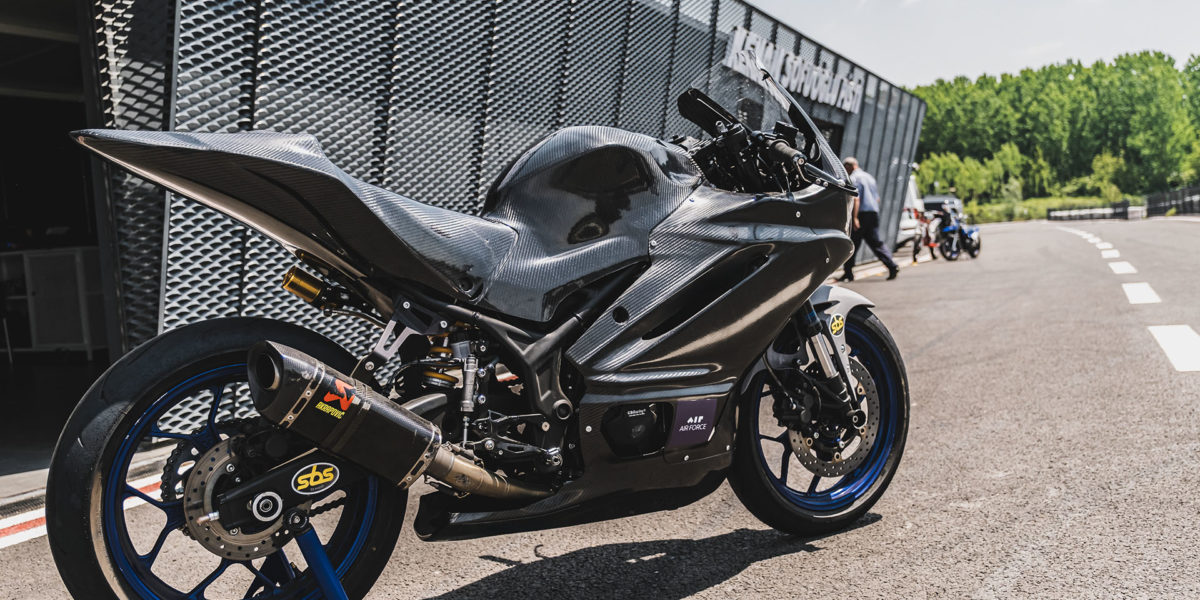
Одна из задач лидеров композитного рынка — продвигать композиты в массы, популяризировать новые материалы. Спорт — отличная для этого возможность. Как «Росатом» взялся за производство композитных обтекателей для супербайков и карбоновых сапбордов, выяснила корреспондентка «СР».
Как все начиналось
Соревнования на супербайках (разновидность кольцевых гонок на мотоциклах, находящихся в свободной продаже) проходят не только между пилотами, но и между механиками. Первые ведут байк по трассе, вторые колдуют над двигателем, чтобы сделать мотоцикл быстрее.
Модернизировать современные моторы очень дорого. К тому же на некоторых чемпионатах вводят ограничения по стоимости доработки одного двигателя. Дешевле установить на мотоцикл обтекатели, улучшающие его аэродинамику. Они должны быть легкими и прочными, чтобы быстрее разгоняться и не ломаться при падениях, которые нередки в этом спорте. В качестве материала для обвеса отлично подходит карбон.
«Сначала я сделал карбоновый шлем, показал спортсменам. Отвечают: «Это мы и в магазине купим, а ты нам сделай из карбона мотообвес (этим словом объединяют и обтекатели, и крылья, и выхлопные системы. — «СР»)». Сделал обвес, получилось намного интересней», — вспоминает Рафаэль Амерханов, руководитель проекта «Мотокомпоненты» композитного дивизиона «Росатома».
Рафаэль Амерханов всегда мечтал заняться мотоспортом. Ни спортсменом, ни тренером он не стал, зато его инженерные таланты пригодились в усовершенствовании техники. Сначала он делал детали на небольшом производстве в Химках с командой из пяти человек. Потом решил масштабировать бизнес и с идеей производства мотообвеса пришел в композитный дивизион.
«Все отнеслись скептически, кроме Александра Тюнина, гендиректора дивизиона. Он любит спорт и понимает, что участвовать в мировых кубках — это прикоснуться к чему‑то недосягаемому для обычных людей. Тем более никто, кроме нас, в России еще ни разу не производил ничего для профессионального мотоспорта. Это его зацепило», — рассказывает Рафаэль Амерханов.
Дизайн и форму компонентов разрабатывали в Москве, а производство наладили на заводе «ЗаряД» в Набережных Челнах, также входящем в состав дивизиона. Основная сложность — в проектировании, ведь каждая деталь для байка индивидуальна. Сначала мотоцикл сканируют, в специальных программах моделируют обвес и просчитывают аэродинамику. Потом с помощью фрезерного станка и 3D-принтера формируют мастер-модель для литья, формуют всю конструкцию и крепят к мотоциклу.
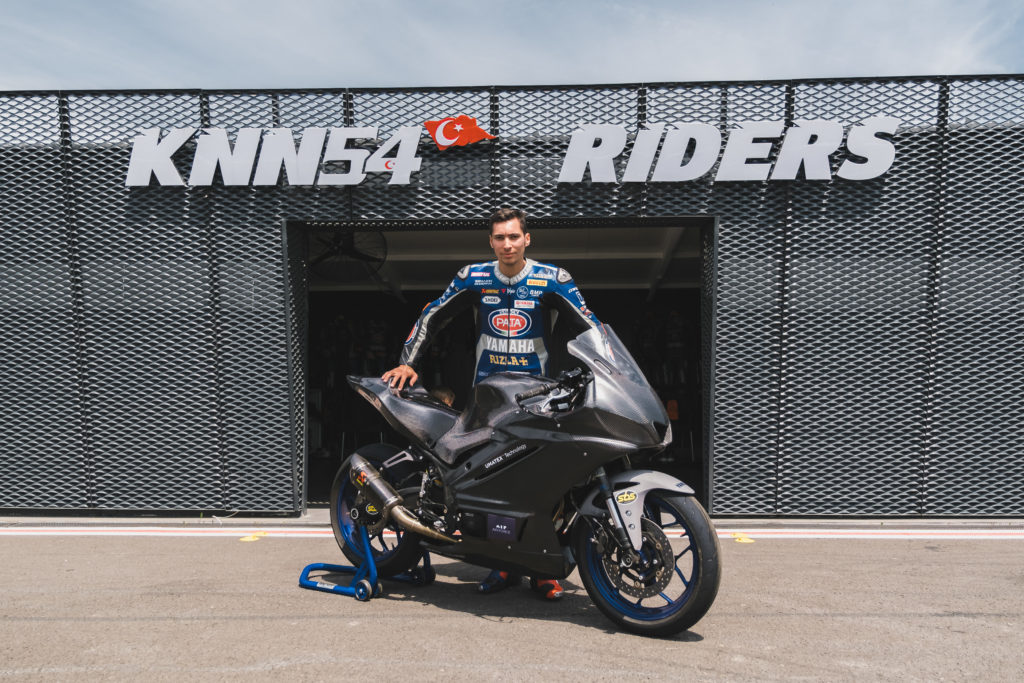
Победный дебют
Впервые карбоновый мотообвес производства «Росатома» испытали в 2019 году во Франции, на чемпионате мира по супербайку. На мотоцикле Kawasaki ZX‑10RR с композитным российским тюнингом выступал турецкий мотогонщик Топрак Разгатлиоглу. В чемпионатах участвуют команды известных производителей байков — Топрак выступал за команду Kawasaki Puccetti Racing. В первой же гонке он победил — впервые на этом состязании. Оказалось, что композитный обтекатель дает преимущество в 0,2 секунды за круг — это 4 секунды за заезд, что очень много для гонок. Применение аэродинамической схемы в изготовлении обвеса позволяло мотоциклу увеличивать скорость на 3–4 км/ч. Улучшение двигателя для такого же результата вышло бы намного дороже.
«Я достиг цели, которой мы с командой добивались на протяжении всего сезона. Хотел бы поблагодарить всех, кто верил в меня, и всю мою команду, поскольку они сегодня проделали исключительную работу. Используя обвес от наших партнеров из «Росатома», я смог разогнаться до большей скорости на прямых участках трассы», — сказал после гонки Топрак Разгатлиоглу.
С автотрассы на воду
Композитный дивизион продолжил работать с Kawasaki Puccetti Racing — он оснастил все мотоциклы команды. Позже компания начала сотрудничать еще с одной командой — Honda Racing Corporation. Но из-за санкций продавать обвесы гонщикам по всему миру стало сложнее, поэтому в 2024 году серийное производство пришлось временно приостановить.
Что касается спроса в России, то здесь пока все сложно: спорт недешевый, масштабных соревнований также пока нет, в результате среди спонсоров мотоспорт не популярен. Чтобы не стоять на месте, дивизион перепрофилировал производство в направление водных видов спорта, где для оборудования нужны те же характеристики: легкость и прочность. Сейчас команда работает над карбоновыми сапбордами для профессиональных соревнований.
Райдеры протестировали первый российский карбоновый сапборд: за счет формы он стабильно держит скорость и больше подойдет для длинных дистанций. Производственные мощности также расположены на заводе «ЗаряД», известном клюшками из карбона.
Как производят карбон
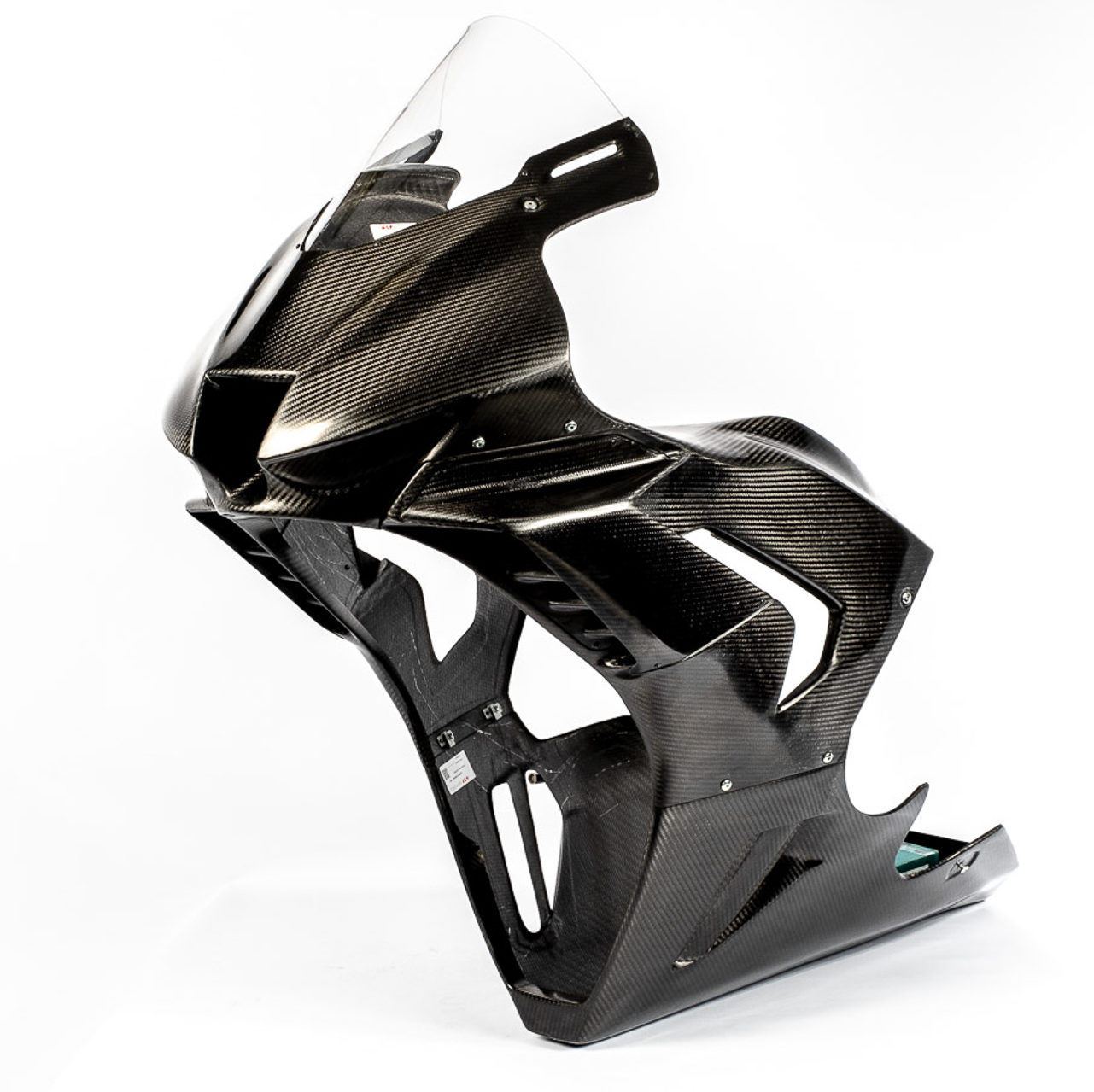
В промышленном производстве в качестве сырья используют полиакрилонитрильные, вискозные, пековые волокна. Сначала идет процесс окисления в воздушной среде при температуре порядка 300 °C в течении 60–90 минут. Следующий этап — карбонизация в инертной среде при температуре около 1500 °C, в ходе которой удаляются атомы таких элементов, как азот, кислород и водород. Доля атомов углерода в составе волокна доходит до 99 %. Есть также дополнительная, но необязательная стадия — графитизация при температуре до 3000 °C, которая позволяет получать максимально жесткие волокна. Далее на специальном заводе углеродное полотно буквально ткут на станках, потом прошивают или заливают эпоксидным связующим.