Руками инженеров: как улучшить закись-окись урана
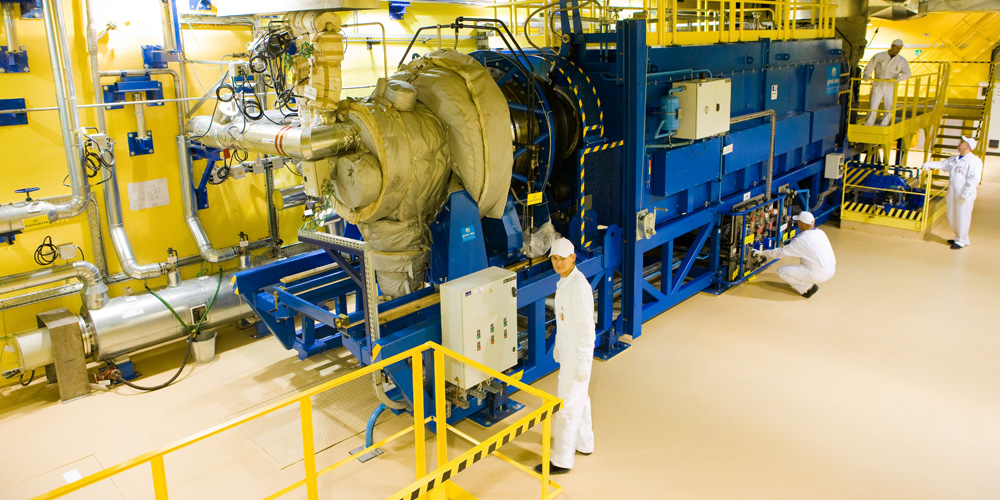
В финал конкурса топливного дивизиона «Технологические лидеры ТВЭЛ» вышли 25 человек. В их числе два сотрудника Электрохимического завода (ЭХЗ). Разработки Александра Лысакова и Константина Куимова, как и других финалистов, воплотят в жизнь на предприятиях дивизиона. Атомщики рассказали «СР», как улучшить закись-окись урана и зачем печатать газоанализаторы на 3D-принтерах.
Программа «Технологические лидеры ТВЭЛ» стартовала в январе. В ней приняли участие 157 атомщиков дивизиона, из них отобрали 72 человека. Это люди, генерирующие идеи по развитию технологий и улучшению качества продукции, авторы ПСР-проектов. По итогам многоступенчатого отбора, заключающегося в анализе личных достижений конкурсантов, мобильности и готовности менять сферу деятельности, прохождении интервью по компетенциям и проч., в заключительный этап конкурса прошли 45 атомщиков.
Актуальные задачи
Финалистам предложили решить реальные производственные задачи, сформированные предприятиями топливного дивизиона. Конкурсанты выбирали их, исходя из своих умений и интересов. Так, ведущий инженер-технолог по подготовке производства, руководитель проекта ЭХЗ Константин Куимов остановился на проблеме повышения качества закиси-окиси урана.
«С января 2023 года введена обновленная редакция технических условий на закись-окись урана, — рассказывает специалист. — Одним из дополнительных требований данной редакции в части содержания примесей является необходимость определения количества алюминия в закиси-окиси. Технологический процесс на ЭХЗ не обеспечивал стабильного достижения установленной нормы содержания алюминия. Повторное растворение не удовлетворяющей требованиям технических условий закиси-окиси урана с повышенным содержанием алюминия приводило к увеличению времени протекания процесса и себестоимости получаемой продукции».
Ведущий инженер по контрольно-измерительным приборам и автоматизации метрологической службы Александр Лысаков решил поработать над проектом с потенциалом на тиражирование. Он выбрал проблему, актуальную не только для ЭХЗ, но и для других предприятий разделительно-сублиматного комплекса.
«Получение фтора и измерение его концентрации — одна из главных задач наших предприятий, поскольку фтор используется в производстве изотопов металлов, — объясняет он. — На последней дивизиональной конференции главных метрологов мы с коллегами обсуждали, чем нас не устраивают газоанализаторы ФА‑01 и ФА‑04, которыми мы измеряем содержание фтора в анодном газе. Измерять надо вручную, результат получается с большой погрешностью. В устройстве используется герметичный реактор с ртутью. Примерно раз в полтора-два года ртуть нужно менять. Для этого приходится отправлять устройства в Новоуральск, а это 4 тыс. км в один конец. Поэтому я и решил усовершенствовать процесс измерения концентрации фтора, чтобы результат стал точнее, а затраты на ремонт снизились».
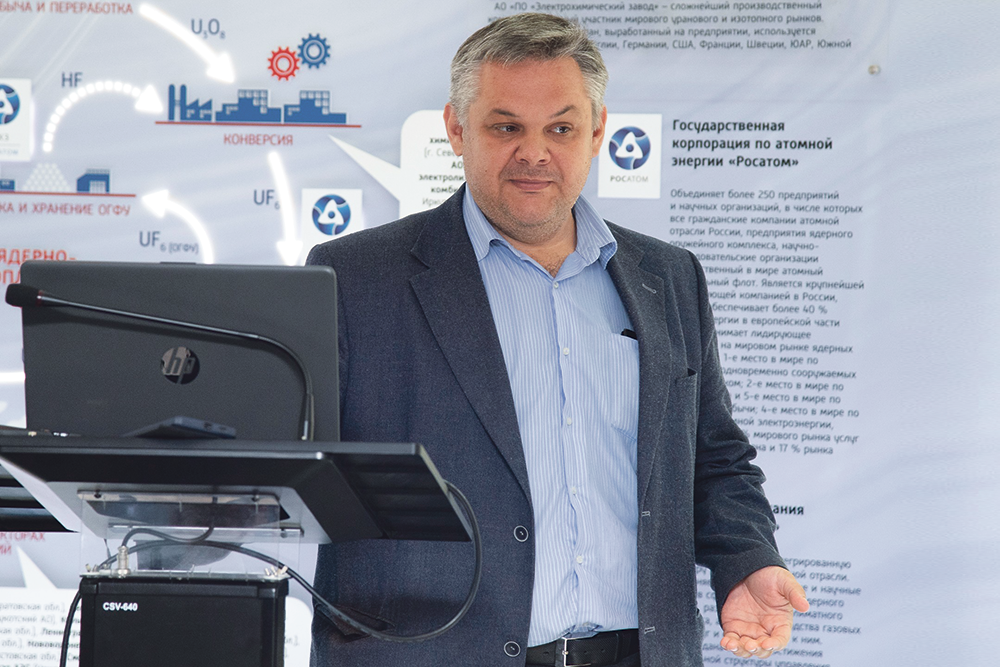
Обеспечили все условия для работы
Все лето конкурсанты работали над своими проектами. Константин Куимов собрал целую команду, привлек в нее коллег по заводу. Александр Лысаков команду не собирал, но обращался за помощью к экспертам центральной заводской лаборатории, метрологической службы, цеха по производству изотопов, производственно-технологической службы.
«Вместе со специалистами ТВЭЛ мы разработали рекомендации для достижения установленных техническими условиями значений содержания алюминия в закиси-окиси урана, — отмечает Константин Куимов. — Определили оптимальные режимы ведения технологического процесса, внесли изменения в аппаратурно-технологическую схему, перенастроили оборудование. В итоге достигли стабильных физико-химических параметров получаемой закиси-окиси урана, снизили количество производственного брака. Уменьшилось число повторных растворений не удовлетворяющей требованиям технических условий закиси-окиси. За счет этого сократились затраты на материалы, используемые при повторном проведении технологических операций. Электрохимический завод в сжатые сроки выполнил производственную программу по выпуску закиси-окиси урана, удовлетворяющей требованиям обновленных технических условий».
Печать на вырост
«В основе измерения концентрации фтора лежит химическая реакция — возможность поглощения фтора ртутью. Она упакована в герметичный реактор, внутри которого много разных механизмов. Точность работы прибора определяет вторичный датчик — манометр. Во время замера нужно много ручных операций, более-менее точные измерения могут сделать только очень опытные операторы, — говорит Александр Лысаков. — Я понял, что процесс надо автоматизировать, и придумал новую конструкцию датчика — из полиэтилена и пластика. Его можно напечатать на обычном 3D-принтере».
Специалист рассчитывает, что опытный образец напечатают коллеги из компании «Русатом — Аддитивные технологии», а в будущем устройство можно будет печатать непосредственно на предприятии, где оно эксплуатируется. По предварительным расчетам, себестоимость нового устройства составит около 20–30 тыс. рублей за штуку, а это примерно в 20 раз ниже, чем стоимость существующего. Тем более что потребность ЭХЗ в таких приборах постоянно растет из-за расширения изотопного производства.
«Новое устройство будет полностью автоматизированным, оно станет частью цифровой среды предприятия, — продолжает Александр Лысаков. — Данные измерений можно будет интегрировать в автоматизированные системы управления технологическими процессами. А сам способ измерения я оставил прежним, он дешевый и удобный. Ремонт же теперь и вовсе не нужен. В одноразовых реакторах есть механизм, позволяющий бесконтактно извлекать емкость с ртутью и быстро менять ее на новую. Использованные емкости мы планируем отправлять на утилизацию в рециклинговую компанию в Зеленогорск».
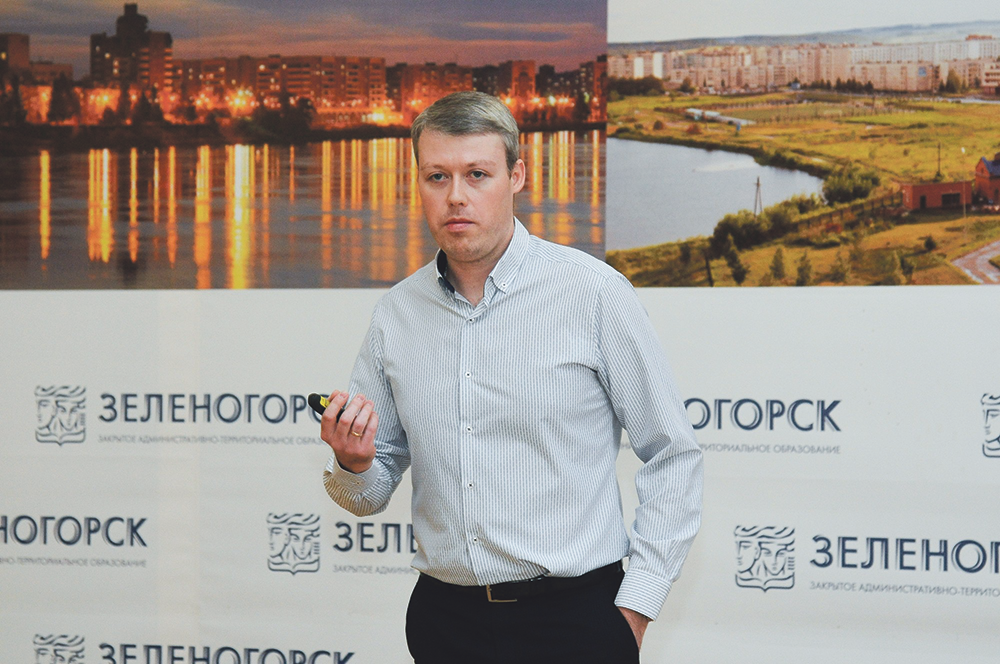
От идеи до образца
В конце сентября авторы презентовали свои идеи конкурсной комиссии под председательством старшего вице-президента по производству ТВЭЛ Михаила Зарубина и генерального директора ЭХЗ Сергея Филимонова. Обе идеи получили одобрение на дальнейшую разработку. Константин Куимов продолжит работу над проектом в масштабах своего предприятия, а новые датчики Александра Лысакова, если все пройдет удачно, появятся на всех газоанализаторах предприятий разделительно-сублиматного комплекса ТВЭЛ. Сейчас идет работа над созданием опытного образца и конструкторской документации прибора.