Время ковать цирконий: 65 лет назад на Чепецком механическом заводе открыли цех № 60
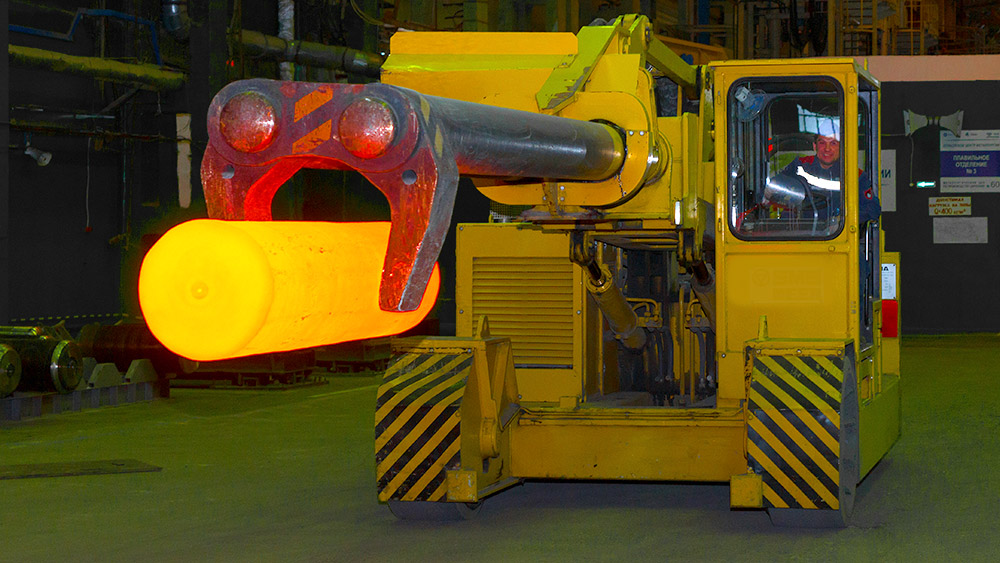
В приуральском Глазове расположено единственное в России производство циркония. На ЧМЗ в цехе № 60 из циркония делают слитки для оболочек топливных элементов, на которых работает каждый шестой реактор в мире. Зачем твэлы из циркония понадобились ледоколу «Ленин», почему кузнецы сильнее борцов и что еще изготавливают мастера завода — в нашей юбилейной подборке.
Как все начиналось
Для первых советских АЭС оболочки твэлов делали из аустенитных нержавеющих сталей. В 1950‑е годы, когда приняли решение строить суда с атомными реакторами, для твэлов понадобились новые материалы. Нержавеющие стали не годились: под действием напряжения в них происходит коррозионное растрескивание, что влечет разгерметизацию твэлов. На ледоколе, где сложнее обеспечить безопасность, такой инцидент недопустим. Началась разработка сплавов на основе циркония, обладающего высокой коррозионной стойкостью.
25 февраля 1958 года вышел приказ о создании металлургического цеха по производству циркония. Сегодня это цех № 60. Первые твэлы с оболочками из особо чистого йодидного циркония установили в реакторе первого в мире атомного ледокола «Ленин».
Рождение слитка
Цех № 60 огромен: два футбольных поля, не меньше. Здесь работают порядка 400 человек. Все начинается с гидрометаллургического передела, где из сырья получают циркониевый порошок. Его прессуют в брикеты, брикеты сваривают между собой и плавят в вакуумно-дуговой печи. Из печи выходят слитки весом до 3,5 т. Их нагревают до 1,1 тыс. °С и перемещают к ковочному комплексу. Пресс с усилием 1,2 тыс. т опускается на слиток, придавая ему необходимую геометрию и механические свойства. Следующий этап — цирконий отправляется на прокатный стан. Всего за четыре минуты сечение 3,5‑тонной заготовки уменьшается с 450 до 260 мм. Длина, соответственно, увеличивается. Затем раскаленную циркониевую колбаску режут на части, которые идут на изготовление оболочек твэлов и элементов ТВС.
Ручная ковка
Работа в цехе в первые десятилетия была очень тяжелой. До 500 т металла в день ворочали и обрабатывали вручную. Загружали брикеты в печь, вынимали слитки, расковывали, вытягивали и рубили кузнечным топором на мерные части. Потом грузили на тележку, снова волокли к печи, загружали… За смену кузнец обрабатывал минимум 10 слитков по 40 кг. «Требовалась и физическая сила, и выносливость, и сноровка, — рассказывает ветеран цеха Павел Ткаченко. — К нам приходили здоровые ребята, борцы, хоккеисты, но даже они надолго не задерживались. Помню, обращаюсь к одному: «Ты ж борец». Отвечает: «Ну и что? Там работают одни мышцы, здесь — другие». Очень тяжело, говорили. А мы привыкли. Хотя у нас ребята были не сказать что здоровяки — щуплые, худощавые. Но опыт был и сноровка».
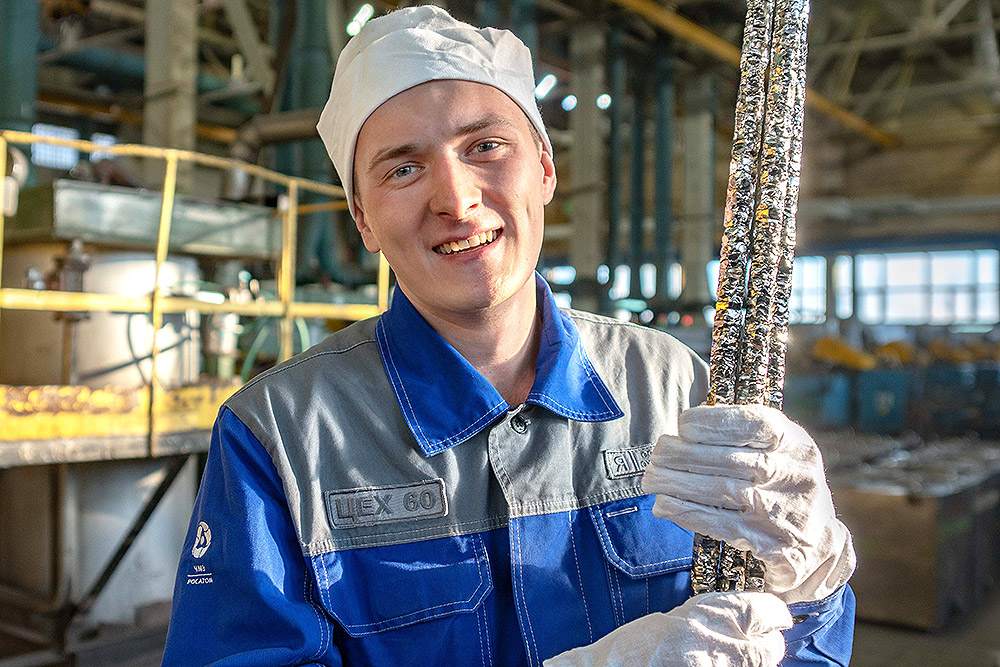
Новое время
В 1990–2000-е годы цех технически перевооружили. Большую часть оборудования разработали специально — например, автоматизированный ковочный комплекс, благодаря которому ковка перестала быть исключительно ручным трудом. Слесарь-ремонтник ветеран завода Вячеслав Лумпов участвовал в пуске сложного кузнечно-прессового оборудования, за что был отмечен государственными наградами — медалью ордена «За заслуги перед Отечеством» сначала II, а потом I степени.
В следующем году на завод поступит самый мощный в истории цеха вертикальный пресс усилием 6 тыс. т. Он разрабатывается в России специально для ЧМЗ.
Красота и здоровье
Рекламу чудодейственных свойств циркониевых браслетов из 1990‑х помнят многие. В те годы и зародился новый бизнес ЧМЗ. Сейчас «Прибор-сервис», дочернее предприятие завода, выпускает сувениры: браслеты, стопки, чарки, подносы с разной символикой.
Наладили в Глазове и производство медицинских изделий из циркония — этот металл обладает высокой устойчивостью к коррозии и не вызывает аллергии. На ЧМЗ разработали технологию, которая позволяет серийно производить дентальные керамические имплантаты. Изделие проходит сертификационные испытания для получения регистрационного удостоверения Росздравнадзора.
Металл на экспорт
В 1959 году на заводе разработали собственную фторидную технологию производства циркония из электролитического порошка. Сырьем служат минералы циркон и бадделеит. Этой технологией пользуются до сих пор. В 2021 году внедрили технологию, тоже собственную, производства из циркониевой губки (за рубежом оболочки твэлов делают только из циркониевой губки). В ходе внедрения зарегистрированы 17 изобретений и патентов. Циркониевая губка может применяться в производстве топливных элементов для всех основных типов энергетических реакторов — и российского, и зарубежного дизайна.
ПОЧЕМУ ЦИРКОНИЙ
У циркония малое сечение поглощения (захвата) нейтронов — то, что нужно для активной зоны реактора: конструкционные материалы из циркония не задерживают нейтроны, их энергия используется максимально эффективно.
В России сосредоточено 10 % мировых запасов циркония. В природе он встречается в виде минералов бадделеита и циркона. В «Росатоме» добычей этого металла занимается АРМЗ.