Вращение вокруг центрифуги: к 70-летию важнейшего изобретения атомщиков
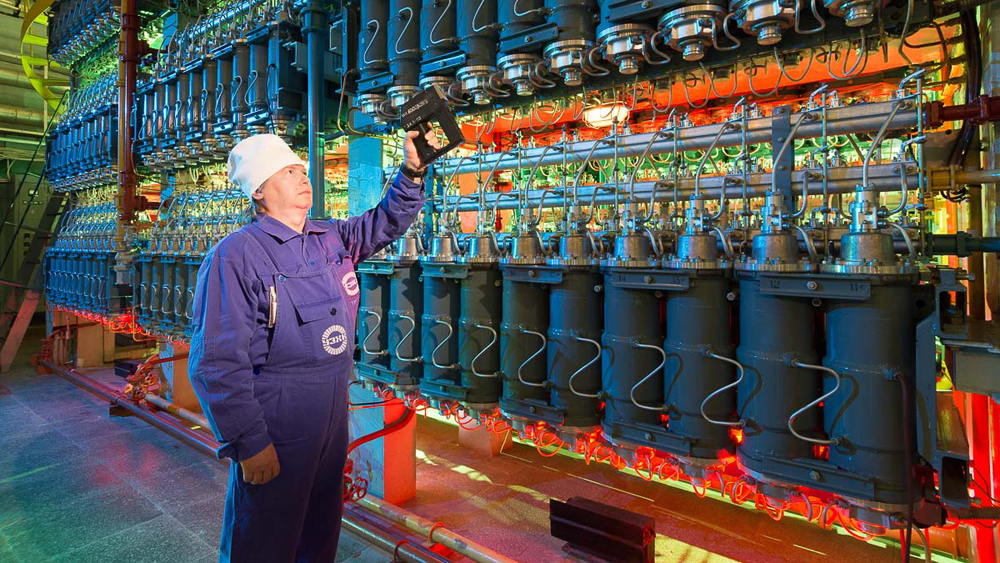
В этом году исполняется 70 лет одному из самых востребованных изобретений отечественных атомщиков — газовой центрифуге. Круглую дату мы отметим циклом публикаций: специалисты напомнят обо всех тонкостях создания и эксплуатации этого устройства для обогащения урана. Первым о лучших качествах юбиляра рассказывает научный руководитель ТВЭЛ по газоцентрифужным технологиям Вячеслав Козин.
Сокрушительное преимущество
70 лет назад все страны, обогащавшие уран, обладали технологией газовой диффузии, и СССР тоже. Но сегодня все газодиффузионные промышленные предприятия остановлены, их полностью вытеснила центрифужная технология.
Уже первые центрифуги потребляли в 20 раз меньше электрической энергии, чем газодиффузионное оборудование, и не занимали столько места. Потери рабочего продукта были намного меньше, быстрее устанавливался стационарный рабочий процесс.
Возьмем для примера диффузионное разделительное предприятие Eurodif, которое было построено во Франции в 1980‑е годы. Современный завод на российских центрифугах в три раза дешевле, в пять раз компактнее, а энергии потребляет в 50 раз меньше.
Но главное, я бы сказал, сокрушительное преимущество газовой центрифуги — ее энергоэффективность. А, соответственно, и экологичность, и экономичность. Себестоимость изотопной продукции, полученной на современных центрифугах, на порядок меньше, чем произведенной по газодиффузионной технологии.
30 лет минимум
Единственное, в чем первая центрифуга не выигрывала у диффузии, — это срок службы. У первых центрифуг он был всего два-три года. А диффузионное оборудование в 1960‑е могло работать без обслуживания до пяти лет, и общий срок его службы составлял несколько десятков лет. Но уже к пятому поколению срок эксплуатации центрифуг достиг 30 лет. С тех пор ко всем новым поколениям центрифуг мы на этапе разработки предъявляем требование: ресурс не меньше 30 лет.
Быстрее, длиннее, эффективнее
Направления НИОКР в развитии центрифужной технологии в широком смысле не изменились за последние 70 лет. Всегда стояла задача увеличить скорость вращения ротора, потому что производительность зависит от квадрата скорости. От поколения к поколению это удавалось сделать за счет новых материалов и конструкторских решений.
Также производительность зависит от длины ротора, но очень длинный ротор становится надкритическим — при разгоне вынужден проходить зону резонанса. Для обеспечения работы и надежности такого ротора мы внедряем специальные инженерные решения. Надкритическая центрифуга более сложная, но и более экономичная.
Три революции
В истории центрифуги я бы выделил три революционных момента. Первый — переход от металлического ротора к металлокомпозитному: достигнув определенного уровня, мы исчерпали прочность металла и взяли более прочные композиты. С тех пор меняются волокна, матрицы, технологии изготовления композитов для получения все большей прочности и надежности ротора, экономичности центрифуги.
Второе принципиальное изменение — переход от коротких подкритических роторов к длинным надкритическим. Эта революция свершилась в девятом поколении центрифуги, более 10 лет назад.
И третье — балансировка ротора. Вообще балансировка широко применяется в технике высокоскоростных машин вращения. Балансировке, например, подвергаются колеса автомобиля для снижения вредных вибраций. Особенность нашей балансировки в огромной частоте вращения ротора, в точнейшем измерении его вибраций, в микроскопической величине допустимого остаточного небаланса. Сегодня балансировка ротора центрифуги и с математической точки зрения, и с аппаратурной — одна из самых наукоемких частей разработки центрифуг.
Безальтернативный метод
Когда я поступал в институт, а было это 30 лет назад, уже существовали методы разделения изотопов помимо центрифужного и газовой диффузии.
Электромагнитный метод придумали до газодиффузионного, но он был еще более энергозатратным и капиталоемким. Обсуждался лазерный метод. Атомы разных изотопов различаются не только массой ядра, но и спектром поглощения излучения. Если воздействовать на них лазерным излучением со строго определенной длиной волны, то можно возбудить атом одного изотопа, а целевой изотоп не возбуждать, или наоборот. И потом уже, пользуясь разницей в характеристиках возбужденных и не возбужденных атомов или молекул, как-то их разделять. Метод и поныне разрабатывается в лабораториях США и Австралии, но пока ни о каком промышленном внедрении речи не идет. Слишком много технических сложностей. Мы отслеживаем эти работы по публикациям в открытых СМИ и на профильных научно-технических ресурсах, и я могу точно сказать, что у центрифуги серьезных конкурентов не появилось и в ближайшие лет 30 не предвидится.
Нет предела совершенству
Наши конструкторы раз за разом находят способы повысить скорость ротора, улучшить параметры вспомогательного оборудования, увеличить срок его службы. Важное направление — автоматизация: человеческий глаз не такой острый, рука не такая точная, реакция не такая быстрая, как у современных высокотехнологичных роботов.
Завершается разработка центрифуги десятого поколения. И мы добиваемся увеличения скорости ротора. Улучшения основаны на новых материалах и оптимизации конструкции. Естественно, при сохранении срока службы 30–35 лет — здесь мы не хотим делать шаг назад ни в коем случае. Думаю, уже в следующем году мы увидим первую опытно-промышленную партию центрифуг десятого поколения, а через два-три года выйдем на серийное производство.
Стратегия у нас прежняя, мы сохраняем конструкторские коллективы и намерение продолжать создавать новые, еще более эффективные модели центрифуг. Мы видим потенциал, возможность роста и экономическую целесообразность этих разработок и внедрений.
ДОСЬЕ
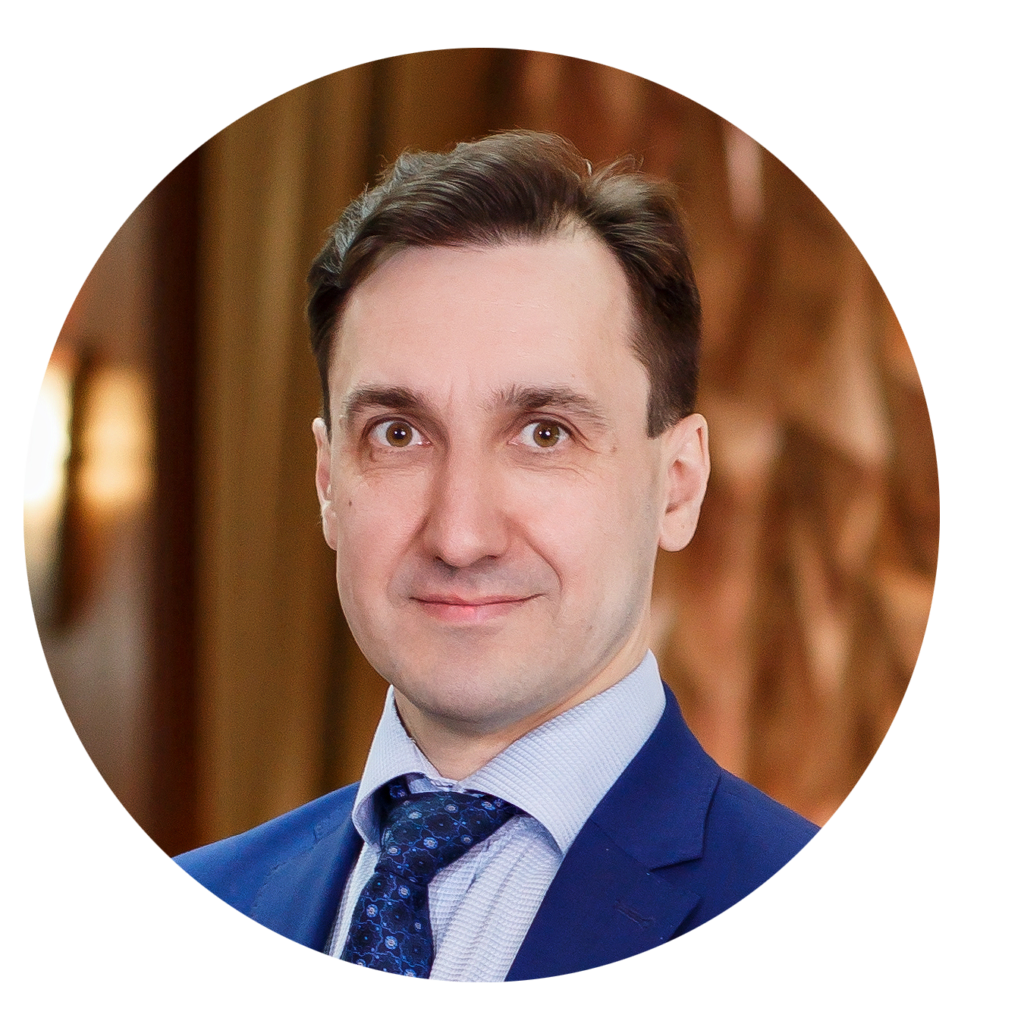
Вячеслав Козин родился в Новоуральске. Окончил физико-технический факультет Уральского политехнического института им. Кирова (сейчас Уральский федеральный университет им. Ельцина) по специальности «разделение изотопов».
С 1996 по 2010 год работал в опытном цехе разделительного производства УЭХК, где создают новые поколения центрифуги. Затем перешел в ТВЭЛ: был директором департамента по газоцентрифужным технологиям, затем — генеральным конструктором, сейчас — научный руководитель.