Как расположить оборудование, чтобы рабочие не делали лишних движений
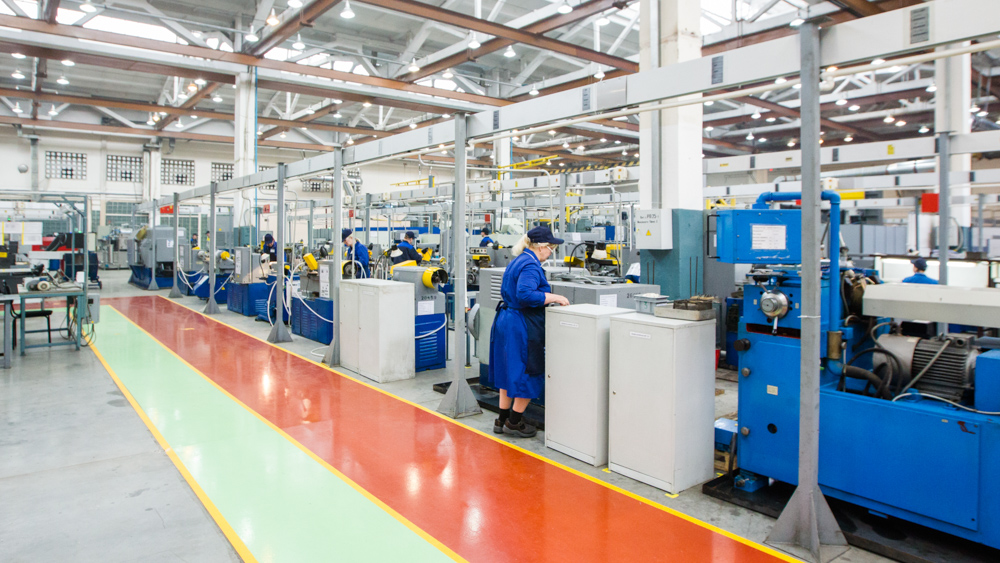
В качестве показательного примера компактизации на вебинаре Корпоративной академии «Росатома» привели проект повышения эффективности производства одного из участков «Точмаша». Мы выяснили подробности.
В 2019 году офис ПСР получил от президента ТВЭЛ Натальи Никипеловой заказ повысить эффективность участка механической обработки «Точмаша». Работа проходила в рамках перевода части мощностей из Владимира в Ковров.
Механический участок, переехавший в Ковров, был бутылочным горлышком в производственной цепочке. Главной целью проекта обозначили увеличение производительности участка в 2,5 раза и повышение качества на 20 %. Начали с создания рабочей группы. В нее вошли представители производства, имущественной и вспомогательных служб, ПСР-специалисты предприятия, дивизиона и госкорпорации. Возглавил группу гендиректор «Точмаша». «Каждый понимал свою роль и ответственность. Директору я мог в любой момент позвонить, договориться встретиться на производстве, чтобы обсудить сложные вопросы, оперативно найти решение. Слаженная работа стала одной из основных составляющих успеха нашего проекта», — рассказал «СР» руководитель проекта в ПСР-офисе «Росатома» Михаил Уренев.
Работа без избытков
Силы распределили по трем направлениям: повышение производительности оборудования, персонала и сокращение брака и возвратов на доделку.
Оценили состояние 11 станков — до целевой производительности недотягивали шесть. Казалось бы, самое простое решение — поставить дополнительное оборудование. Но покупать новое дорого и долго, а снимать оборудование с других участков возможности не было. Да и участок занял бы слишком много места, потребовалось бы больше операторов — опять же незапланированные затраты.
Всесторонний анализ показал, как достичь цели без дополнительных ресурсов. Прежде всего сократить холостые ходы, исключить избыточную обработку и подобрать оптимальную последовательность действий. Действия можно запараллелить: пока станок работает в автоматическом режиме, без участия оператора, тот готовит к обработке следующую партию деталей или выполняет слесарные операции на обработанных деталях. Усовершенствовали приспособление для крепления — установка заготовки стала быстрее, повысилась точность позиционирования. Все это тоже сыграло на увеличение производительности.
К самому «медлительному» станку применили перебалансировку. Часть простых операций перевели на соседний станок — производительность отстающего дошла до нужных параметров.
10 вариантов планировки
Чтобы повысить стабильность выхода качественной продукции, разработали несколько стандартов: прописали в деталях, кто, что и когда должен делать, приложили фото операций, обучили персонал работе по этим стандартам.
Затем занялись производительностью сотрудников. Анализ показал, что станки размещены нерационально, не по порядку выполнения операций: путь изделия от станка к станку достигал 66 м. Чтобы лишний раз не ходить, операторы накапливали 5–10 изделий и только потом грузили их на тележку и везли на следующую операцию. Рос запас и общее время производства.
Группа разработала 10 вариантов планировки, которые крутились вокруг одного станка на специальном фундаменте, перезаливать его было бы слишком дорого. Обсудили, выбрали, утвердили. Прежде чем перемещать, решили проверить, соответствуют ли реальные габариты оборудования и оснастки заявленным. И правильно сделали: оказалось, что размеры трех станков больше, чем указанные в документах, поэтому планировку пришлось поменять. Потом перешли в цех. На полу мелом обозначили контуры станков и попросили операторов пройти по маршруту, чтобы выяснить, есть ли неудобства или преграды. Снова внесли правки. В конечном варианте зону входа заготовок и выхода готовой продукции разместили рядом с проездом, чтобы транспортировщик не заезжал на электрокаре в рабочую зону. Там же поставили контейнеры для стружки, чтобы операторам станков не мешал персонал, который ее вывозит.
Перестановка в одно касание
Заодно улучшили эргономику рабочих мест — сделали полки для набора клейм и других нужд, подставки для заполнения документов, удобно разместили инструмент, нанесли контрастную разметку на рабочие столы и др. Придумали стружкоуловитель, который во время обработки заготовки собирает стружку и подает в рукав, идущий к контейнеру. Нововведение в разы сократило время на уборку цеха.
Также досконально продумали, в какой последовательности переставлять станки, чтобы не двигать их по несколько раз. Изначально на перемещения станков отводилось три месяца (один-два станка за выходные), в итоге справились за три недели.
Площадь участка сократилась в 2,3 раза, перемещения по нему — в 4,5 раза, а производительность и качество достигли заданных значений.
ЦЕЛИ КОМПАКТИЗАЦИИ
Офис ПСР сотрудничает с департаментом имущественного комплекса «Росатома» по проектам компактизации и оптимизации с 2011 года. Целей две. Первая — высвободить площади для новых производств. Вторая — минимизировать перемещение сотрудников, чтобы повысить производительность. За 2011–2021 годы выполнены 22 проекта. Сейчас реализуются 18.
Один из ярких примеров — переезд Московского завода полиметаллов в Электросталь, на промплощадку МСЗ. Оборудование из пяти корпусов разместили в одном. Площадь сократилась вчетверо, а маршрут движения продукции — в 15 раз.
В прошлом году сотрудничество решили расширить. Если раньше специалисты ПСР проводили только экспертизу на этапе защиты проекта компактизации и оптимизации у его куратора, то теперь они подключаются на самом раннем этапе — анализе потенциала, и участвуют в проекте до его завершения. Еще одно новшество — эксперты не просто исследуют потоки (компонентов, готовой продукции и отходов), но и занимаются их оптимизацией. На 2022–2024 годы запланировано проработать 34 таких проекта — потребность в них на предприятиях отрасли растет.