Предприятия отрасли помогут восполнить дефицит импортных комплектующих
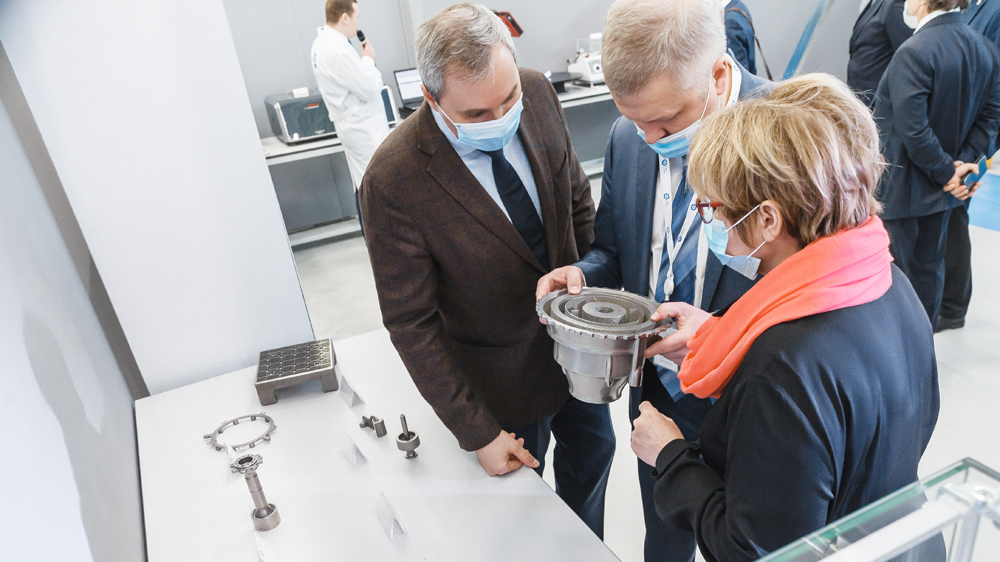
Отраслевой интегратор «Русатом — Аддитивные технологии» («РусАТ», входит в ТВЭЛ) открыл оперативную линию для компаний, столкнувшихся со сложностями из-за ограничений на импорт материалов и комплектующих. Часть деталей можно делать в России методом 3D-печати. Только за первую неделю работы оперативной линии «РусАТ» получил десятки обращений.
Многие промышленные предприятия столкнулись с проблемой поставок запасных частей и комплектующих для оборудования зарубежных производителей. По данным Российского экспортного центра, больше всего пострадали такие отрасли, как электроника, тяжелое машиностроение, энергетика, авиация, нефтегазодобыча, космос, судостроение и транспорт. Заместить часть зарубежных деталей можно силами «Росатома», в том числе интегратора по аддитивным технологиям — «РусАТа».
«Из-за прекращения поставок сильно пострадала гражданская авиация. Есть сложности у топливно-энергетического комплекса, станкостроительной и добывающей отраслей. Например, к нам на оперативную линию обратились сотрудники предприятия «Росатома», занимающегося добычей руд. Они работают на японских экскаваторах, расходные материалы к которым быстро изнашиваются — стачиваются коронки и режущие кромки ковшей. А привезти их сейчас невозможно. Попытаемся помочь», — рассказывает «СР» коммерческий директор «РусАТа» Алексей Марченко.
На горячую линию принимают обращения любых российских технологических компаний. Сейчас есть некоторые ограничения на размер деталей — крупные комплектующие для аэрокосмической отрасли напечатать вряд ли получится. Могут возникнуть временные трудности с медицинскими изделиями, например имплантами: изготовить их можно, но лицензирование займет время.

Приоритетное направление — реверс-инжиниринг деталей из сплавов, а также их частичное или полное производство аддитивным методом. Реверс-инжиниринг — это исследование готовой продукции и ее документации для создания аналогов, имеющих схожие с оригиналом характеристики, но без прямого копирования. Это позволяет сократить расходы на разработку, изготовление и испытание изделия или оборудования.
В «РусАТе» рассматривают каждое обращение индивидуально: принимают заявку, подробно выясняют, с какой проблемой столкнулась компания, проводят первичную оценку возможности изготовления изделия, исходя из описания и документации. Заказчик привозит изделие инженерам «РусАТа», они его сканируют, смотрят чертежи и технический паспорт, анализируют состав материала. Если удается подобрать подходящую по техническим характеристикам замену сплава и создать 3D-модель изделия, его отправляют на печать.
«Оперативная линия запущена совсем недавно, да и самой идее буквально месяц. Тем не менее у нас уже есть большое количество обращений и первая статистика, показывающая, что эта услуга крайне востребована. В прямой проработке 10 проектов, и это только за первую неделю работы. Есть обращения просто эмоциональные: люди звонят и говорят, что это нужно было сделать давным-давно. Также через горячую линию мы параллельно с заявками компаний принимаем предложения от российских инженеров, готовых работать в этом направлении. У них есть идеи, которые раньше они не могли реализовать», — комментирует Алексей Марченко.
В ближайшее время все производственные мощности «РусАТа» будут полностью загружены. Кроме того, прорабатывается проект формирования национального оператора по импортозамещению в сфере аддитивных технологий, что позволит задействовать мощности не только «РусАТа», но и других предприятий «Росатома», а возможно, и предприятий вне контура госкорпорации.
Проблем с материалами для печати специалисты не предвидят: в России есть производства металлических порошков и других исходных материалов. Порошки из алюминиевых, медных сплавов, нержавеющей и высоколегированной стали для 3D-принтеров и металлургии производит новоуральское НПО «Центротех» (входит в ТВЭЛ). Там в 2020 году началась промышленная эксплуатация установки «Капля». На ней металлические порошки производят методом газового распыления расплава. По химическим и физическим характеристикам они не уступают зарубежным и отечественным аналогам. Еще одна установка «Центротеха», «Шайба», делает титановые порошки для медицинских протезов. ЧМЗ выпускает титановые порошки и проволоку, порошки из циркония и керамики.
Специалисты отмечают, что напечатанные на 3D-принтере детали по качеству могут даже превосходить произведенные традиционными методами — например, литьем. Можно модифицировать изделие, улучшить механические характеристики. Однако вопрос в цене. «Мы воспринимаем эту меру как скорую помощь. Аддитивные технологии более дорогие, так как предполагают сложный цикл производства: от сканирования до изготовления изделия. Это огромное количество процессов, в которых задействовано много людей. Сейчас мы говорим лишь о стратегическом замещении, чтобы предприятия не прекращали свою деятельность. О какой-либо коммерциализации речи пока не идет. В будущем — возможно, но это нужно делать несколько другими способами. Например, если мы произвели единичное изделие методом 3D-печати, то потом его можно модифицировать, улучшить и адаптировать для более массовой печати или даже для классических методов производства, например литья», — поясняет Алексей Марченко.