Андрей Никипелов: «Мы войдем в топ-5 российских машиностроительных компаний»
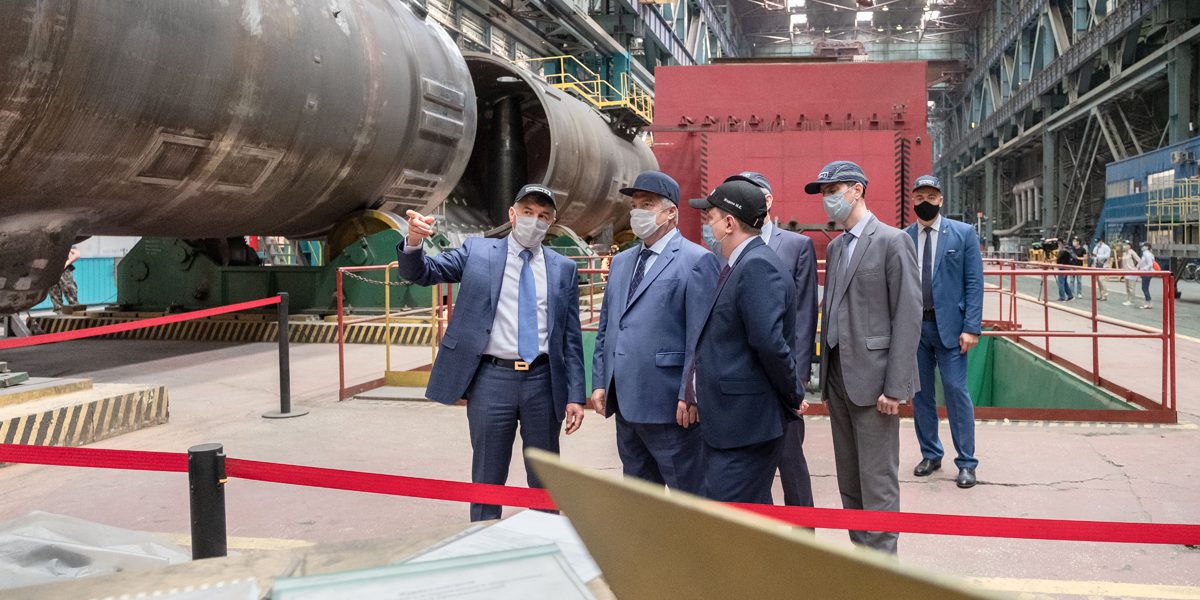
Машиностроительный дивизион «Росатома» в этом году отметил 15-летие. В преддверии двух профессиональных праздников, Дня машиностроителя и Дня работника атомной промышленности, мы встретились с гендиректором «Атомэнергомаша» Андреем Никипеловым, чтобы расспросить его о ключевых этапах истории дивизиона, о рекордах и планах, а также о главных вызовах будущего.
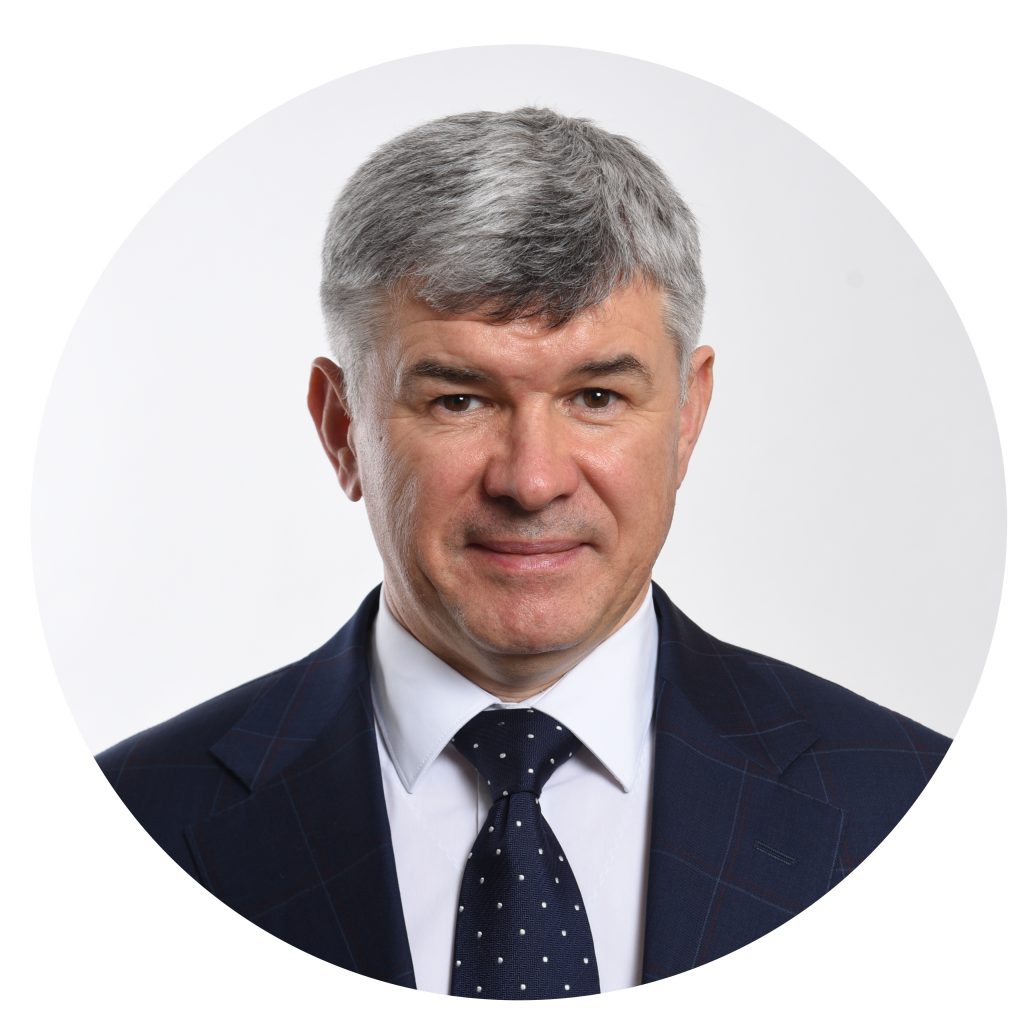
— «Атомэнергомаш» в 2020 году поставил абсолютный производственный рекорд — выпустил 18 парогенераторов и три корпуса реактора для АЭС. Сложным ли оказался путь к этому рекорду?
— Думаю, этот путь начался с момента создания «Атомэнергомаша». В 2006 году в отрасли была принята программа развития атомной энергетики России, которая предполагала постепенный выход на выпуск двух, а впоследствии даже трех блоков АЭС ежегодно. На этапе согласования программы многие в правительстве говорили, что это невозможно просто потому, что никто не сможет обеспечить отрасль оборудованием в нужных объемах.
Действительно, такая проблема была. Пауза в строительстве АЭС после Чернобыля, отсутствие больших зарубежных проектов… Было понятно, что единственный на тот момент изготовитель реакторов в стране, «Ижорские заводы», не сможет обеспечить необходимый объем поставок оборудования. Так и возникла идея создания машиностроительного дивизиона в контуре «Росатома».
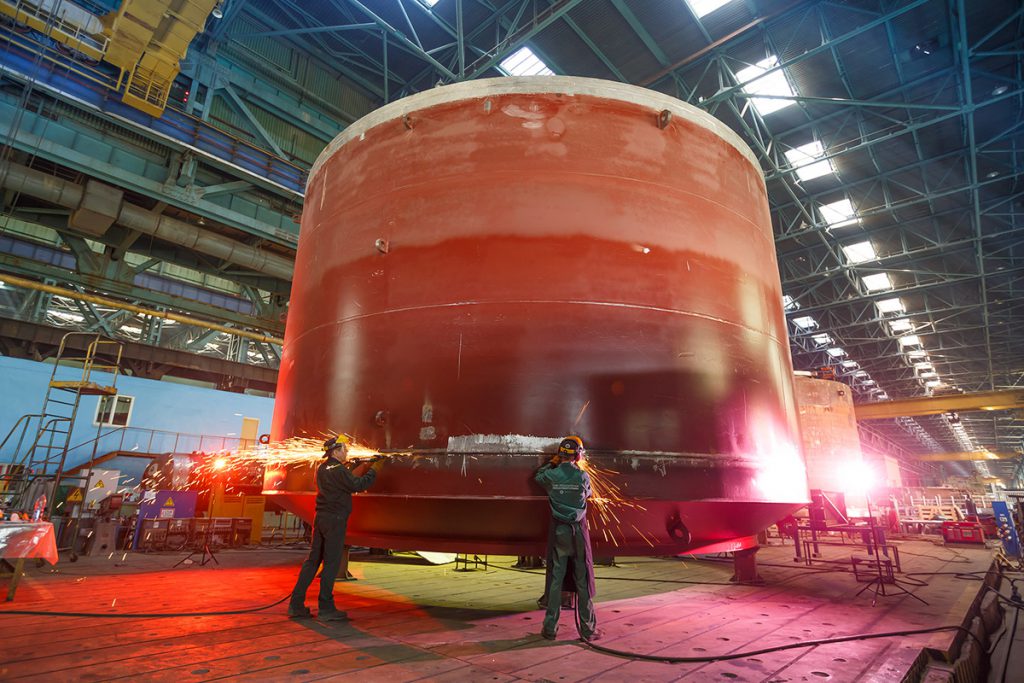
— С чего начали?
— Первая задача, которая была поставлена перед «Атомэнергомашем», — обеспечение графика строительства атомных станций, сначала в основном в России, потом уже и за рубежом. Начали с покупки единственного изготовителя парогенераторов — «ЗиО-Подольска». Причем на тот момент там только набивали уже готовый корпус парогенератора, а полного цикла производства, от обечайки до готового изделия, на не было.
Мы стали искать площадку, которая была бы в состоянии делать также корпуса реакторов и парогенераторов. Изучили около сотни предприятий по всей России и остановились на «Петрозаводскмаше». Он в то время представлял собой, скажем так, остатки завода по выпуску бумагоделательных машин, но обладал производственными корпусами нужной нам размерности, а также полезным оборудованием, например кранами. Одним из безусловных преимуществ площадки была собственная причальная стенка — доступ к воде, что позволяет легко вывозить крупногабаритные изделия. Почти одновременно купили и «Энергомашспецсталь» — поставщика заготовок для корпусов.
Для освоения производства длинноциклового оборудования в дивизионе была принята достаточно большая инвестпрограмма.
— А потом появился «Атоммаш»?
— Да. В конце 2012 года стало понятно, что у нас появляется возможность взять под контроль «Атоммаш». Мы остановили инвестпрограммы на других предприятиях. Получив «Атоммаш», мы наконец смогли производить полный комплект оборудования ЯППУ для АЭС. Так был сформирован основной контур дивизиона. При этом иногда приходилось принимать очень сложные решения. Например, тот же «ЗиО-Подольск», который был куплен именно из-за производства парогенераторов, в итоге этого производства лишился. Мы перевели этот функционал на «Атоммаш», а его заместили другими заказами, в том числе выпуском реакторного оборудования для ледоколов, для мусоросжигания, тепловой энергетики.
В итоге специализация распределилась следующим образом: главный конструктор АЭС — ОКБ «Гидропресс», заготовки для оборудования большой атомной энергетики — «Энергомашспецсталь», изготовление реакторной установки и всего связанного с ней оборудования — «Атоммаш» и «Петрозаводскмаш». «ЗиО-Подольск» мы специализировали на изготовлении всего крупногабаритного теплообменного оборудования для машзалов. Петербургское ЦКБМ как было, так и осталось основным изготовителем главных циркуляционных насосов.
ОКБМ им. Африкантова — разработчик и конструктор для «быстрой» тематики, по реакторам БН, создатель всей линейки судовых реакторов. В год закладки первых ледоколов проекта ЛК-60 мы начали выстраивать под них цепочку производства оборудования. ОКБМ выступало главным конструктором и изготовителем судовых парогенераторов, а также вспомогательного оборудования. А вот выпуск корпуса разработанного ОКБМ нового транспортного реактора РИТМ предстояло освоить «ЗиО-Подольску». При этом предприятия дивизиона выпуском судовых реакторов до того момента никогда не занимались — все корпуса для транспортных реакторов делал либо «Красный Октябрь», либо, когда-то давно, — «Ижорские заводы».
Так мы завершили первый этап в истории дивизиона — создание базовых производственных мощностей. Основная задача второго этапа, освоить производство, выпуск и перестать зависеть напрямую от внешних поставщиков, также была решена. Следующей задачей стало обеспечение постоянно растущей дорожной карты строительства новых объектов. К этому добавилась еще специфика зарубежного рынка. Поскольку сегодня практически все основные заказы на строительство АЭС у нас за пределами страны, то мы еще должны были обеспечить соответствие своего оборудования всем международным нормам и правилам — получить аттестации и лицензии за рубежом. Нам нужна была полная готовность каждого звена производственного процесса к работе на внешнем рынке.
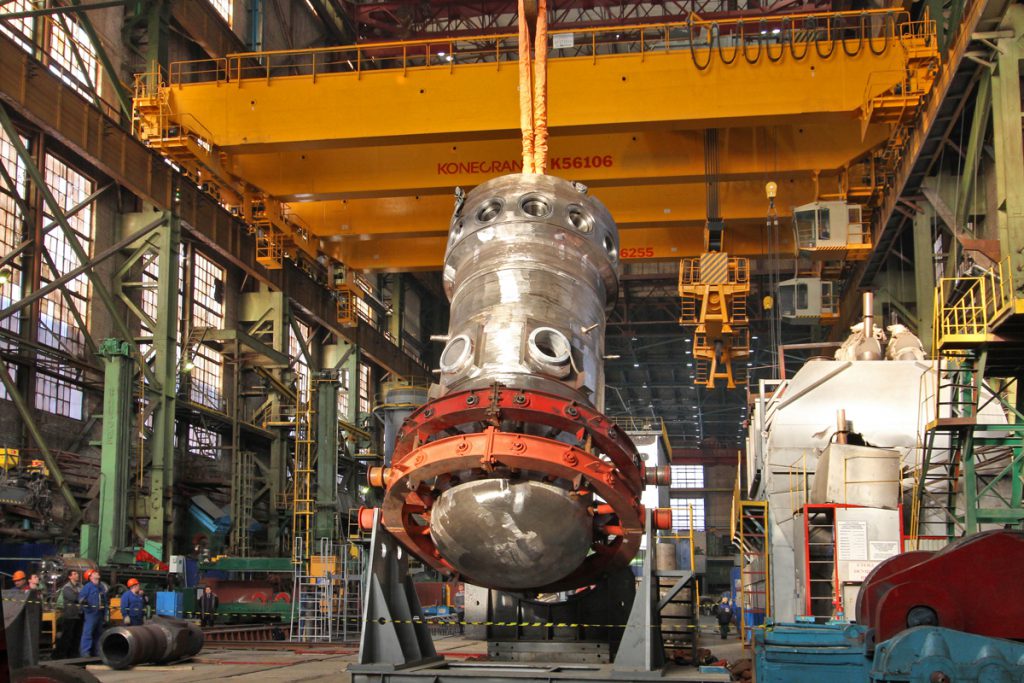
— Что было сделано на основных заводах дивизиона, чтобы привести их в необходимое состояние?
— Сначала мы вложили довольно большие деньги просто в восстановление станочного парка, потому что некоторым станкам было по 40 лет. Они были работоспособны, но нам нужна была точность и скорость, то есть другие, гораздо более высокие, производственные характеристики.
«Петрозаводскмаш» мы фактически полностью переоснастили. Купили несколько реально уникальных станков. Так, один из них имеет глубину фундамента метров десять, а площадь под ним сравнима с большим дачным участком — 10–12 соток. Зато он обрабатывает целый корпус главного циркуляционного насоса за один раз.
Следом перед нами встала задача оптимизации производства, повышения эффективности существующих мощностей. Вот, к примеру, когда-то мы стояли перед сложной развилкой в судьбе ЦКБМ. Видели, что там идет постоянный срыв сроков, не успевают изготавливать нужное количество выемных частей. Сели разбираться с тогдашним директором ЦКБМ Евгением Дмитриевичем Сергеевым. Поняли, что надо либо покупать еще один завод, либо покупать кучу станков и всего остального, либо разворачивать широченную кооперацию, потому что дорожная карта строительства АЭС подразумевала практически утроение объемов производства.
В итоге мы пошли по другому пути: продали большую площадку с кучей оборудования. Расставаться с ней было тяжело — все-таки историческое место. Кроме того, на момент продажи площадки мы еще не знали, куда будем переезжать. Поэтому мы ее продали с обязательством выехать через год, а сами чуть меньше года искали новую. Были риски, что многие специалисты откажутся переезжать вместе с предприятием. К счастью, удалось найти производственные площади рядом, на Кировском заводе. Не очень далеко нашлись и офисные площади.
Переехали и фактически заново выстроили производственную цепочку. Рассмотрели под сотню вариантов размещения станков — в зависимости от того, по какому циклу будет двигаться заготовка. Стремились сделать так, чтобы все строилось по принципу конвейера, когда станки стоят на месте, а изделие движется от одного передела к другому. И нашли в этом возможность дальнейшей оптимизации.
Вот еще пример. На ЦКБМ станок «Олимп» является одним из базовых, от него зависит изготовление главных циркуляционных насосных агрегатов. В определенный момент мы предполагали, что для обеспечения нужных объемов производства нам надо будет докупить один-два таких станка. Но благодаря ПСР-проекту и вовлечению в решение задачи всех, кого только можно было вовлечь, нам удалось максимально эффективно обустроить производство: станок стал работать в три смены, а мы научились на тех же мощностях делать в три раза больше работы, при этом в резерве еще оставалось 30% свободной мощности.
— Есть еще интересные примеры рекордной эффективности?
— Конечно. ОКБМ, например, увеличило количество производимых парогенераторов для установок РИТМ-200 примерно в девять раз! Если раньше за два года они делали один комплект парогенераторов для транспортного реактора, то теперь в год делают три-четыре.
На «ЗиО-Подольске» были у нас тяжелые времена, когда было сложно справляться с объемами заказов. Коллектив каждый раз находил решение, как выйти на пиковое производство, а после — сохранить в работе все те инструменты, которые использовались для решения этой задачи.
Хочу еще раз подчеркнуть, что рекорд прошлого года был обеспечен за счет совокупности факторов: восстановления оборудования, творчества в планировании, в организации потоков изготовления корпуса реактора и парогенераторов. На «Атоммаше» у нас сегодня также выстроена логика конвейера, когда станки стоят, а продукт движется в одном направлении — от заготовки до готового изделия, которое буквально выкатывается через большие ворота для отправки заказчику.
— На «Атоммаше» огромные площади позволяют так все организовать?
— Это только так кажется. Сейчас из четырех корпусов, изначально предназначенных для производства реакторной установки, мы используем один. Раньше под производственный процесс было задействовано 600 тыс. м2, сейчас — порядка 250 тыс. И, в принципе, мы могли бы уплотниться еще. Причем на этих же 250 тыс. м2 дополнительно размещены и учебный центр, и классы, которые готовят для завода специалистов буквально всех рабочих профессий: там учатся сварщики, крановщики, станочники, специалисты по качеству. Там же у нас находится лаборатория. Туда же переместили конструкторов и технологов. Раньше они сидели за пределами заводской производственной площадки, теперь — внутри. Это сократило время на бесконечное перемещение, когда технолога нет ни на рабочем месте, ни в цехе, а он где-то в пути между этими двумя точками. Что это дало? Оптимизацию процесса: теперь технологи вместе с конструкторами работают прямо на производстве и любой вопрос решают оперативно.
— Какова сегодня максимальная мощность по выпуску оборудования для АЭС у «Атомэнергомаша»? Ее достаточно для выполнения заказов «Росатома»?
— Мощностей у АЭМ достаточно, учитывая возможности по кооперации с другими участниками рынка. И мы, в общем, не заинтересованы в том, чтобы существующие мощности дополнительно наращивать. У нас есть хорошие перспективные планы, мы видим, что нужно сделать, чтобы обеспечить отрасль нужными объемами оборудования. Поэтому какие-то заказы мы запускаем в производство чуть раньше, чем это нужно по графику строительства, а какие-то — четко по графику. Такой метод позволяет нашим заводам не прирастать ненужными станками, которые будут простаивать и отвлекать инвестиционные деньги.
— Плавучие станции и наземные АЭС малой мощности — это тоже гигантский заказ для ваших предприятий. Как со всем этим справиться?
— В ближайшие два года выручка дивизиона должна вырасти вдвое по отношению к 2020-му. Прошлый год мы закончили с выручкой порядка 83 млрд рублей, а наш план на 2022–2023 годы — это примерно 140–150 млрд рублей, в зависимости от исполнения дорожной карты. Здесь сказывается вклад большой энергетики — мы выполняем заключенные ранее контракты на поставки для больших АЭС на базе ВВЭР и параллельно с этим изготавливаем оборудование для ледоколов, работаем над новыми контрактами по другим направлениям бизнеса, в том числе по плавэнергоблокам и наземным АСММ.
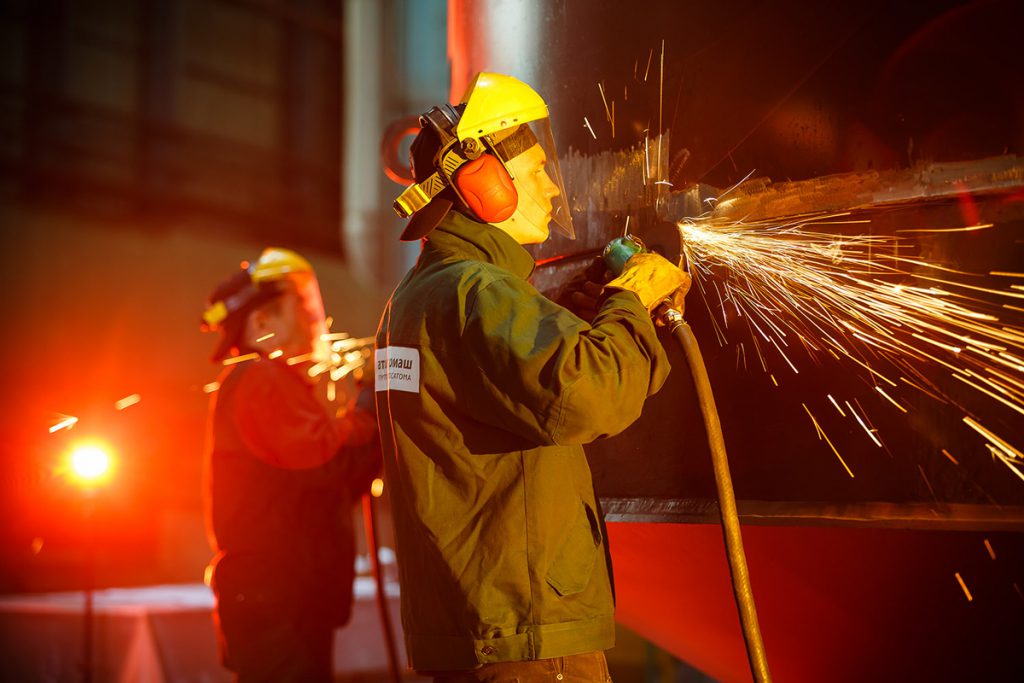
— В этом главный вызов для дивизиона сегодня?
— Думаю, выручка может быть в некотором смысле универсальным мерилом. Я работаю в компании девять лет. Так вот, девять лет назад выручка «Атомэнергомаша» была 35 млрд рублей. В этом году у нас план — 113 млрд рублей. Рост более чем в три раза. И темпы роста будут ускоряться.
Обеспечить изготовление оборудования под все текущие графики строительства АЭС — это для нас по-прежнему сложная, но понятная и отчасти рутинная задача. А для меня лично основная и главная задача — найти, как мы будем расти дальше, в новых бизнесах и в новых продуктах. Я сейчас думаю о загрузке предприятий дивизиона после прохождения запланированных пиков производства в 2026–2028 годы.
«Атомэнергомашу» важно найти свою роль в реализации стратегической цели «Росатома» по достижению выручки в 4 трлн рублей к 2030 году. Задача, поставленная перед дивизионом, — выйти к этому сроку на выручку в 400 млрд рублей, из которых 300 млрд — доля новых продуктов.
Скорее всего, к 2030 году такого количества строящихся блоков большой мощности в дорожной карте, как сейчас, не будет. А новые продукты нам во многом еще только предстоит найти.
— Какие новые продукты вы считаете самыми перспективными?
— Это и плавэнергоблоки, и крайне важная для нас СПГ-тематика, и производство оборудования для заводов по термической переработке отходов.
— Расскажите, что предстоит сделать по проекту для Баимского ГОКа.
— Заказчику для обеспечения добычи нужно порядка 320 МВт мощности. Ее будут генерировать три постоянно работающих плавучих энергоблока. Четвертый плавэнергоблок будет заменять один из действующих, когда тому нужно будет уйти на перезагрузку топлива и техобслуживание. Электроэнергия нужна заказчику уже к началу 2027 года. К этому моменту мы должны изготовить первые два плавблока. И это очень сложная задача.
Из-за сжатых сроков проекта мы приняли решение использовать корпус, аналогичный корпусу ПАТЭС «Академик Ломоносов». При этом у нас уже есть эскизное решение оптимизированного плавэнергоблока, который примерно на 30% меньше в физических размерах, но при этом способен производить больше электроэнергии, чем ПАТЭС.
Ключевое отличие новых плавэнергоблоков от «Академика Ломоносова» — реактор и турбина. На «Ломоносове» стоят реакторы КЛТ-40 мощностью 70 МВт, а мощность базового реактора для нового плавблока, РИТМ-200, примерно 100 МВт.
Вообще, мы уже говорим о целом семействе плавэнергоблоков, прародителем которого является ПАТЭС «Академик Ломоносов». Для Баимского ГОКа «Атомэнергомаш» делает модернизированный ПЭБ, МПЭБ, мощностью примерно 106 МВт на базе корпуса «Ломоносова», но с другим составом основного оборудования. Дальнейшим развитием идеи является оптимизированный плавэнергоблок, ОПЭБ, — уже с другим корпусом, еще рядом изменений и вариантами по мощности и исполнению — арктический и тропический.
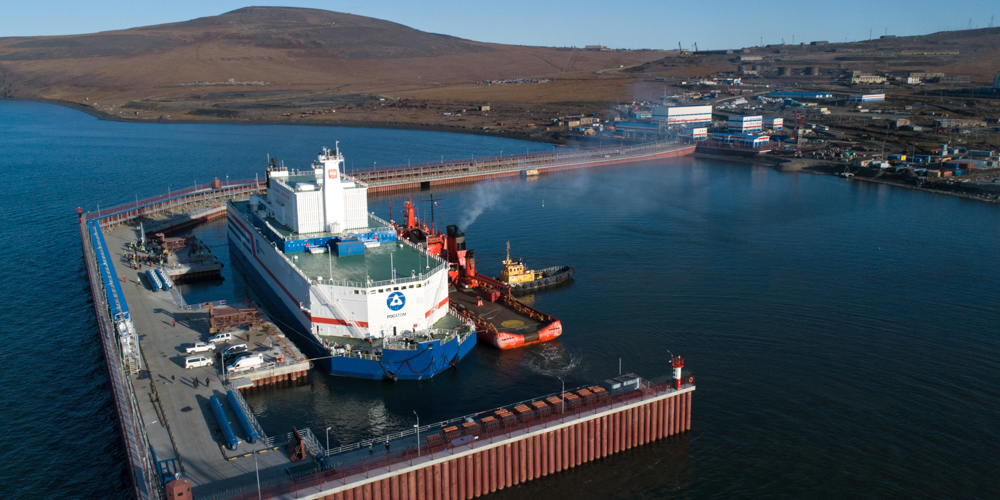
— В чем отличие арктического и тропического ПЭБа?
— Там есть свои нюансы. Дело в том, что температура воды прямо влияет на мощность плавучего энергоблока. Например, в тропиках нет такой холодной забортной воды, как в Арктике. Кроме того, все, что в арктическом исполнении требует в ПЭБе нагрева, в тропиках, напротив, требует охлаждения.
— На Восточном экономическом форуме было подписано соглашение с компанией «Глобалтэк» по проекту энергообеспечения газового комплекса с использованием плавучих АЭС. О чем это?
— Это проект по производству СПГ в Якутии. Здесь заказчику нужно около 800 МВт, то есть примерно восемь плавучих блоков одновременно, что, в общем, не очень эффективно, потому что ПЭБов получается слишком много. Так что мы сейчас работаем над следующей версией плавэнергоблока, в два раза более мощной, на базе реактора РИТМ-400. Соответственно, новая, более мощная версия ПЭБа также предполагает более мощную турбину и другой корпус.
— Газовый комплекс для якутского СПГ — это какие примерно сроки реализации?
— Там тоже первая мощность нужна в 2027–2028 годы. Но заказчик еще не принял окончательное решение по инвестициям, хотя у нас уже есть понимание по предварительным шагам в рамках этого проекта. Задача «Атомэнергомаша» сейчас — как можно быстрее завершить техническое проектирование оптимизированного плавблока с РИТМ-400, чтобы в следующем году уже можно было обсуждать с заказчиком конкретные коммерческие условия.
— «Атомэнергомаш» ведь уже работает по СПГ-тематике. Расскажите об этом, пожалуйста, чуть подробней.
— Мы очень хотим изготавливать оборудование для СПГ-комплексов. Шансы на поставку криогенных теплообменников у нас есть только там, где применяется российская технология, потому что зарубежная технология требует в главном технологическом переделе применения зарубежного оборудования.
Так что пока больше всего обсуждений идет именно по насосам, это тоже очень сложное оборудование. Большие криогенные насосы для крупнотоннажного производства СПГ — это изделие массой под 40 т. Наш размерчик, что называется. Несколько таких насосов мы уже ранее поставили заказчику. Они прошли ряд испытаний, доказали соответствие техническим параметрам. Заказчик доволен.
Сейчас мы изготавливаем следующий насос, это уже пятый или шестой типоразмер, который мы осваиваем. Планируем в декабре этого года начать его испытания на новом стенде в НИИЭФА им. Ефремова, с тем чтобы как можно быстрее предъявить хорошие характеристики заказчику. Тогда мы, надеюсь, получим контракт еще на семь-восемь единиц.
— Расскажите об испытательном стенде. Почему была выбрана площадка НИИЭФА?
— Так решил «Росатом». Стенд был очень нужен стране. Без него ни один отечественный изготовитель не сможет предъявить результаты натурных испытаний своего СПГ-оборудования в той среде, в которой оно будет эксплуатироваться. Среда СПГ-проектов — это минус 163℃. Мы, например, испытывали до этого насос в азоте также при сверхнизкой температуре — минус 190℃. Но заказчик справедливо заметил, что формально это другая среда — не сжиженный природный газ, а ему важно точно понимать, как оборудование будет вести себя в реальной эксплуатации на СПГ-заводе, ведь это риск огромными деньгами. Поэтому встал вопрос о строительстве специализированного испытательного стенда в России. Его проработка с Минпромторгом началась еще в 2018 году.
В мире подобных стендов меньше, чем пальцев на одной руке. Основные два работают в США. Еще один стенд поменьше — в Японии.
Относительно площадки для российского стенда были разные идеи. Рассматривалось место поблизости от ОКБМ, который на сегодняшний день является основным плановым потребителем услуг этого стенда. Построить объект в Нижегородской области у нас не получилось — вокруг не было необходимой инфраструктуры. Ведь стенд — опасный объект, поскольку использует в работе сжиженный природный газ, что требует особых мер безопасности. Питерский НИИЭФА, у которого есть вся необходимая с точки зрения безопасности инфраструктура, предложил использовать свободную территорию у них. «Росатом» поддержал эту идею. И эта площадка победила в конкурсе.
— Насколько сложной оказалась реализация проекта?
— Проект был однозначно сложным, в частности из-за пандемии, но мы справились. Например, по графику мы должны были направить проект в Главгосэкспертизу как раз тогда, когда в стране шел второй день общего карантина. Если бы не помощь Алексея Евгеньевича (А. Е. Лихачева, гендиректора «Росатома». — «СР») буквально на каждом этапе согласования проекта, было бы совсем тяжко.
Прошли экспертизу, начали изготавливать оборудование. Абсолютно каждый поставщик, с кем мы работали, столкнулся с той же проблемой: либо его собственное предприятие было закрыто из-за эпидемиологических требований соответствующего региона, либо внешние поставщики подвели. Добавьте сюда еще транспортный коллапс, закрытые границы. Самый большой срыв сроков в графике нам принесли немецкие поставщики арматуры, которых на данной стадии производства заменить было фактически некем. В итоге по основному оборудованию нам сорвали сроки поставки примерно на четыре месяца. И только за счет графика монтажа и серии компенсирующих мероприятий сумели выполнить работы в срок.
Сейчас стенд построен. Впереди еще много работы по регистрации объекта и подготовке его к работе — закачке жидкостей: СПГ и азота. Например, для испытаний требуется немалое количество азота. Несколько производящих азот предприятий два-три месяца будут работать только для того, чтобы наполнить наши емкости. В течение ближайших месяцев мы рассчитываем завершить подготовку и до конца декабря начать на стенде первые испытания.
— Есть ли какие-то проблемы у вас со специалистами? Какой план набора людей с учетом увеличения заказов?
— Нам предстоит набрать до 1,5 тыс. человек, чтобы выйти на численность, которая позволит реализовать все планы. Люди так или иначе нужны на разных предприятиях — на «ЗиО-Подольске», «Петрозаводскмаше», «Атоммаше». Это самые разные специальности, но кадры мы готовим самостоятельно. Фактически на каждом предприятии налажено взаимодействие со школами, техникумами, вузами. Так что к задаче обеспечения кадрами мы относимся спокойно. Нужно набирать людей — будем набирать, нужно готовить — будем готовить. У нас для этого все есть.
Сложности бывают, когда нужно найти много людей и срочно. Тогда начинаем искать в соседних регионах, перемещать специалистов, думаем над тем, как им переехать, где им жить. Но в большей степени мы заинтересованы в том, чтобы растить людей «снизу», в городах присутствия предприятий. Жить дома, в привычной обстановке и работать на хорошей работе — это всегда лучше, чем даже на самую замечательную работу уезжать куда-то, отрываясь от семьи.
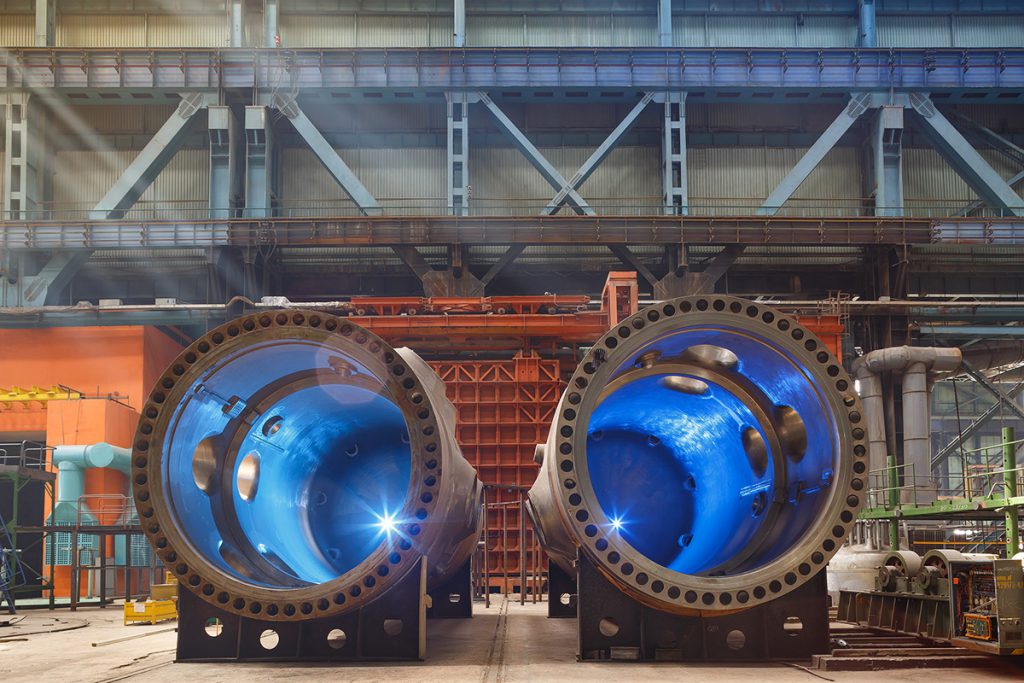
— Каким вы видите «Атомэнергомаш» через пять, десять лет?
— Стратегия дивизиона для нас не просто документ на полке — это наше руководство к действию на каждый день. Когда создавался дивизион, мы покупали предприятия под задачи, связанные с производством реакторных установок, но у этих предприятий были также и другие компетенции. Это заложило основу диверсификации бизнеса «Атомэнергомаша».
В итоге АЭМ сегодня уже не просто крупнейшая компания в энергетическом машиностроении. «Атомэнергомаш» — значимый игрок в машиностроении как таковом. И я рассчитываю, что мы через несколько лет войдем в топ-5 крупнейших российских машиностроительных компаний.
Мы следим за разными направлениями, смотрим, что можем производить сами, а что — нет, нужна кооперация. Вот, например, за плавучие энергоблоки «Атомэнергомаш» отвечает как за продукт. Но АЭМ не планирует покупать себе верфь и строить корабли. Кораблестроение — это отдельная история, а наша задача — выстроить соответствующие кооперационные цепочки, чтобы этот продукт появился — в нужные сроки, с нужным качеством и ценой. Кроме того, недавно мы создали в Санкт-Петербурге филиал, который будет выпускать элементы пропульсивного комплекса для судов. Это довольно сложное изделие, супер-хай-тек. Для понимания: одна лопасть винта ледокола весит 23–24 т. Мы планируем делать винты не только для ледоколов, но и для других судов — для рынка.
Производство оборудования машзалов АЭС — тоже довольно большой кусок работы. Мы делаем все вспомогательное оборудование под отечественные быстроходные турбины. В рамках СП с GE выпускаем оборудование для тихоходных турбин. Сейчас еще создаем сервисное подразделение, чтобы не ограничиваться изготовлением и поставкой запчастей.
В будущем «Атомэнергомаш» должен стать диверсифицированной компанией, с разными направлениями работы как в большой, так и в малой энергетике: плавучие энергоблоки, наземные АСММ. И, кроме того, иметь целый ряд проектов, не связанных с атомной тематикой, например по мусоросжиганию, на которое мы сильно рассчитываем с учетом актуальности «зеленой» повестки в стране.
— Сложно представить, что еще нового может появиться в линейке бизнесов через пять лет?
— В «Атомэнергомаше» часто происходит так: сначала рождается какая-нибудь «безумная» идея, потом вокруг нее появляется еще с десяток связанных бизнес-идей, а затем некоторые из них вырастают в реальные проекты.
Например, года полтора-два назад у нас появилась идея, почему бы не сделать турбину, которая будет работать не на пару, а на углекислом газе? Такая турбина будет по размеру в разы меньше традиционной, потому что среда углекислого газа настолько по-другому работает, что позволяет турбине потенциально выдавать те же характеристики, но в меньших габаритах. И вот сейчас мы уже по чуть-чуть работаем над этой «углекислой» тематикой.
— Готовите настоящий прорыв?
— Вполне возможно. Потому что это означает, что машзал потенциально может уменьшиться в размере в 10 раз. А если эту технологию перенести еще в наши судостроительные проекты, может появиться огромная экономия в весе. Конечно, это пока идея. Вырастет ли после НИОКР что-то конкретно реализуемое, мы еще не знаем.
— А есть какие-то сроки по этой углекислой турбине?
— Все упирается в то, что для подтверждения работоспособности технологии фактически нужно построить специальную электростанцию, которая будет работать на углекислом газе. Это довольно большие деньги. Так что дать прогноз, будет ли принято такое решение в будущем и когда, я не могу. Но мы над этим работаем.