В России наладили производство ключевых компонентов ветроустановок
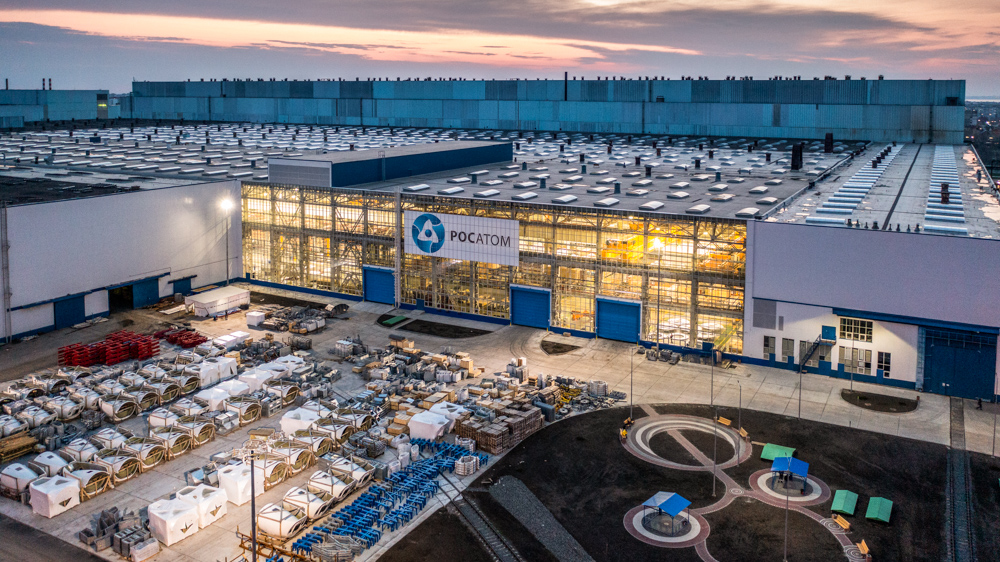
Прошло чуть больше года с момента пуска первой ветроэлектростанции «Новавинда». Не так давно заработала четвертая: 1 июля Марченковская ВЭС в Ростовской области начала поставки на оптовый рынок энергии и мощности. Как удалось нарастить темпы строительства ВЭС и создать с нуля производство компонентов ветроустановок — в нашем материале.
Набор скорости
«Суммарно с начала проекта мы ввели 540 МВт ветроэнергетических мощностей. Строим еще три ветропарка общей мощностью 240 МВт, — рассказывает Андрей Нестерук, заместитель гендиректора «Новавинда» по обеспечению жизненного цикла ветропарков. — Проделана огромная работа по ДПМ‑1 (договоры о предоставлении мощности, в рамках которых суммарно будет введено 1,2 ГВт. — «СР»), и мы уже готовимся к ДПМ‑2 (углубление локализации и экспорт оборудования и услуг. — «СР»). Рассматриваем ряд площадок, включая пять в Ростовской области, изучаем возможность экспорта комплектов, ведем переговоры со странами Юго-Восточной Азии, Среднего и Ближнего Востока».
Нарастить темп строительства ВЭС позволила организация серийного производства ключевых компонентов ветроустановок на базе «Атоммаша» в Волгодонске: генераторов, гондол, ступиц и оснований башен — 120 комплектов в год. Но повышенный интерес к Ростовской области вызван не столько расположением производства компонентов ВЭУ, хотя и это важно, сколько ветровым потенциалом региона. «Мы ожидаем очень высокий коэффициент использования установленной мощности на Марченковской ВЭС. Это большой плюс для эксплуатации, — продолжает Андрей Нестерук. — С начала строительства первых ВЭС мы набрали хорошую скорость, наработали базу технических решений. Не обошлось и без нюансов, они свойственны каждой площадке. Так, достаточно долго выполнялся монтаж установок, потому что постоянно дули мощные ветры. Зимой даже здесь, на юге, были сильные снегопады, пришлось убирать снег, чтобы продолжать работу».
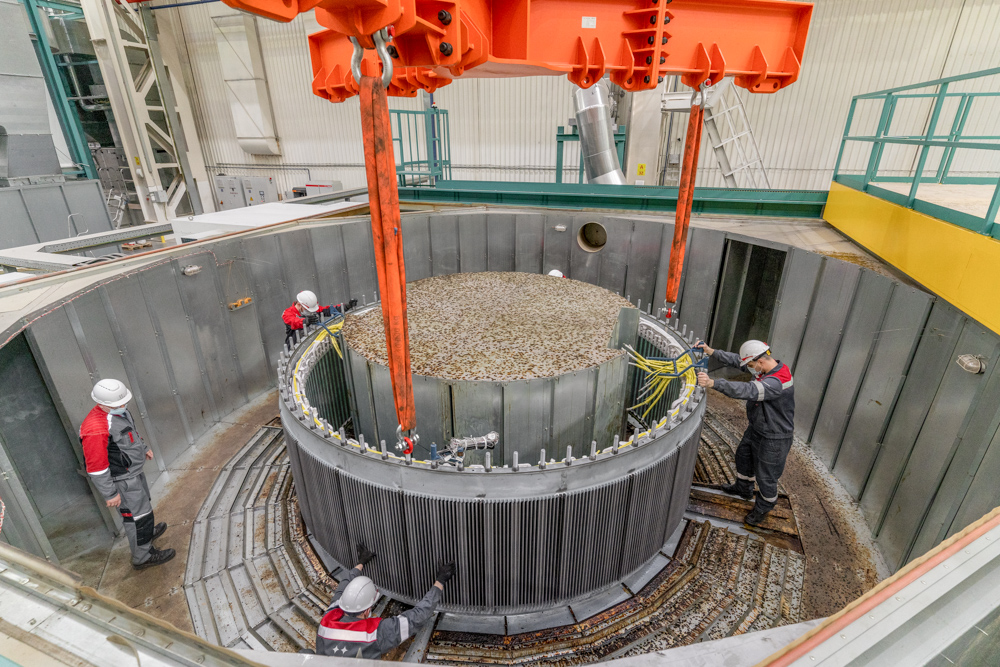
Шире диапазон
Фактически «Новавинд» локализовал новую в стране технологию — ВЭУ на постоянных магнитах. «Они работают в более широком диапазоне ветра и считаются более «тихоходными», это прогрессивная технология. Все отечественные ВЭС, кроме наших, — на редукторных машинах. Вдобавок в России нет компаний, которые производят редуктор полностью сами, а нам нужна была максимальная локализация, — комментирует Григорий Тихий, директор департамента контрактации и качества «Новавинда». — Когда мы проанализировали рынок, поняли, что большую часть компонентов для ветроустановок в России никто не делает. Нам предстояло создать цепочку надежных поставщиков, которые смогут изготавливать компоненты ВЭУ у нас в стране. Это было непросто, как и запустить уникальное производство ветроустановок в Волгодонске и найти квалифицированные кадры».
«Новавинд» отправил 50 человек изучать производство ветроустановок: теорию — в Голландии, практику — в Германии. Специалисты вернулись, начали работать и обучать других. «Еще мы сделали курс с элементами виртуальной реальности по производству генератора, гондолы, ступицы и проч. В обязательном порядке каждый новый сотрудник проходит курс, закрепляет знания на производстве под присмотром наставника. 16 смен — и допуск к самостоятельной работе», — рассказывает Григорий Тихий. На заводе работают более 270 человек.

В целом степень локализации производства оборудования, поставляемого с завода «Новавинда» и предприятий-партнеров, уже достигла 68 %. Помимо российских поставщиков в проектах «Новавинда» участвуют производители из Европы, США, Великобритании, Китая, Индии, Японии.
Фабрика ветряков
Генератор с прямым приводом — один из основных компонентов ВЭУ, которые производят на заводе. Он преобразует механическую энергию вращения ветроколеса в электрическую. «Новавинд» адаптировал инновационную разработку голландского партнера Lagerwey, создав полноценное серийное производство ветроустановок.
«В составе генератора — порядка 150 тыс. листов ламинации из динамной стали с очень сложной и высокоточной геометрией, — говорит Григорий Тихий. — На старте мы выяснили, что делать такие листы в необходимом нам количестве отечественная промышленность не способна. Мы нашли в Италии компанию, которая на протяжении последних 60 лет занимается только листами ламинации. Она, кстати, один из партнеров Tesla и Volkswagen. Итальянцы заинтересовались проектом «Новавинда» и решили войти в цепочку поставщиков. При нашей поддержке открыли в России производство, перевезли часть оборудования, спроектировали штампы, отработали с одним производителем стали технологию изготовления заготовки с требуемыми электротехническими свойствами, обучили персонал. Сегодня это предприятие уже исполняет заказы других клиентов, а поставщик стали обладает технологией производства проката с уникальными свойствами».
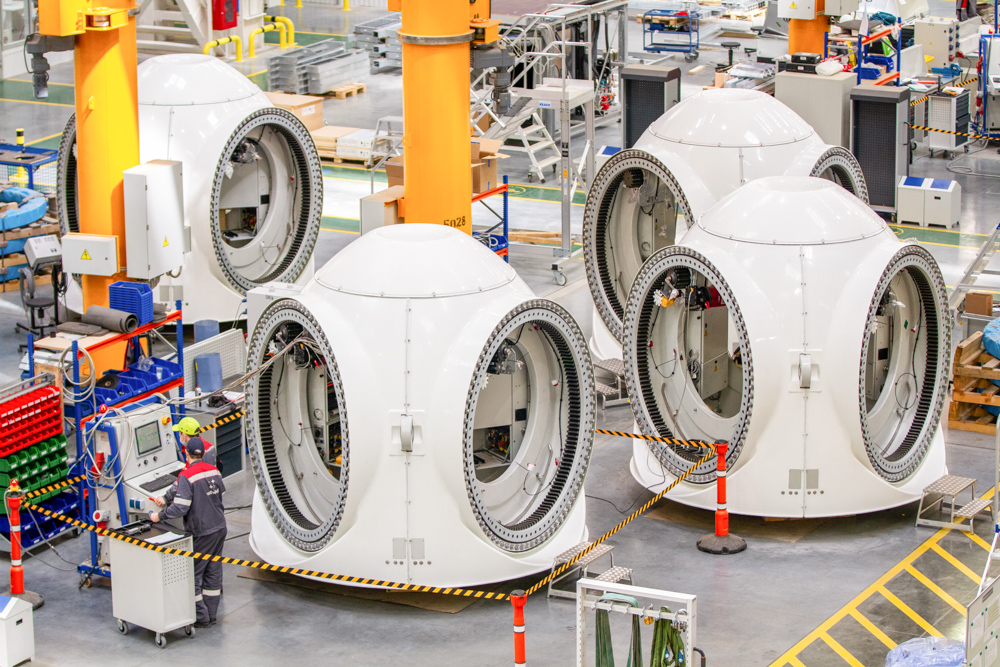
На производстве в Волгодонске установлена вакуумная камера VPI диаметром 6 м, высотой 2,5 м. В ней компоненты генератора пропитывают электроизоляционной смолой. Для тестирования каждого изделия построены стенды. К примеру, главный подшипник на стенде вращают 72 часа без остановки. Именно на него приходится колоссальная нагрузка при эксплуатации ВЭУ. На других стендах проходят финальные тесты генератора: в течение 12 часов имитируются разные режимы работы. Характеристики изделий заносят в электронную базу данных, чтобы отслеживать жизненный цикл каждой ВЭУ.
Еще один крупный компонент — гондола. В ней размещается основное оборудование: система управления углом поворота, главный подшипник, блок управления, метеостанция. Гондола, которую делает «Новавинд», — в своем классе самая легкая и компактная в мире.
Такие парки можно строить даже в труднодоступных районах, без развитой транспортной инфраструктуры. ВЭУ способны работать 20 лет, практически не требуя обслуживания, все параметры контролируются дистанционно.
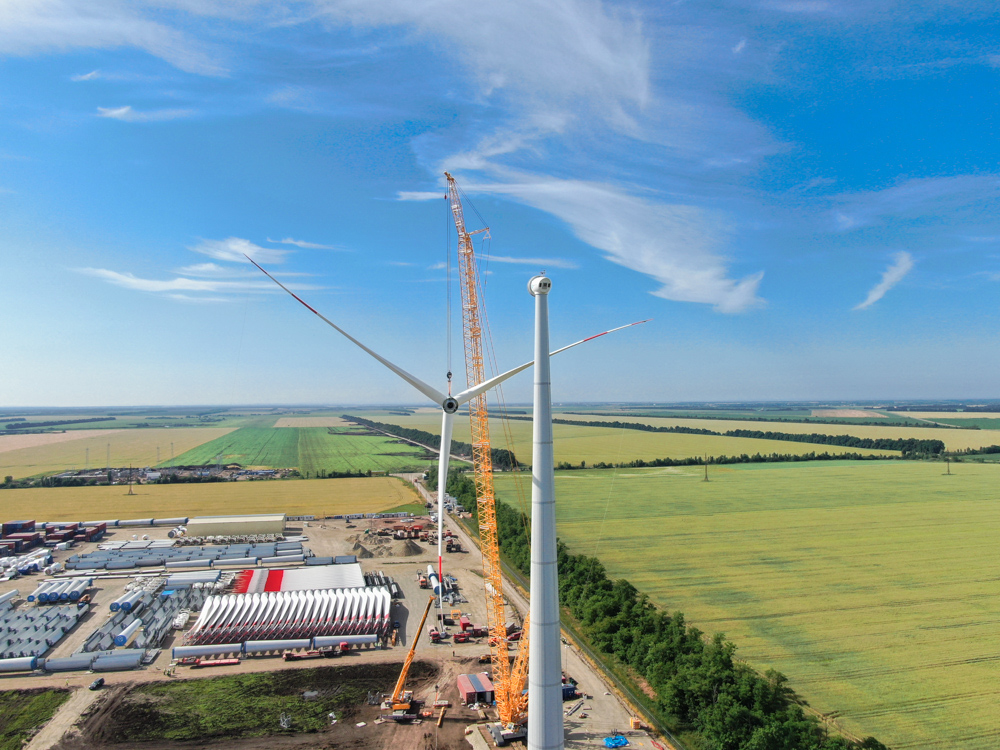
«Новавинд» применил интересное решение для упрощения монтажа — так называемую «ИКЕА»-фабрику. На ней комплектующие раскладывают в контейнеры — по три для каждой ВЭУ (крупные элементы привозят отдельно). «Монтажники на площадке открывают первый контейнер — и перед ними сразу то, что нужно на начальных этапах инсталляции, и точно в необходимом количестве. Во втором и третьем контейнерах — для последующих этапов. «Такой подход значительно ускоряет монтаж, — говорит Григорий Тихий. — Вообще, у нас все производство — от поступления компонента на склад до выпуска готовой продукции — расписано буквально по минутам. То же касается и пусконаладочных работ».
На базе «Атоммаша» производят все крупногабаритные части, кроме лопастей. «Новавинд» обсуждает с композитным дивизионом Umatex возможность локализовать и их производство.
Если говорить о более широких перспективах, то кроме нынешних 2,5‑мегаваттных ветроустановок «Новавинд» планирует со временем заняться и 4,5‑мегаваттными. «По конструктиву они схожи, но компоненты масштабнее, — объясняет Григорий Тихий. — Например, генератор 2,5‑мегаваттной машины весит 52 т, а 4,5‑мегаваттной — уже 120 т. Когда мы проектировали завод, сразу думали о будущем. Все основные конструктивные решения — дверные проемы, полы и грузоподъемные устройства — сделаны и под 4,5‑мегаваттную машину. Как и основное оборудование — камера пропитки VPI, печи и стенды».
РАБОТАЮТ
Адыгейская ВЭС — 150 МВт
Кочубеевская ВЭС — 210 МВт
Кармалиновская ВЭС — 60 МВт
Марченковская ВЭС — 120 МВт
СТРОЯТСЯ
Бондаревская ВЭС — 120 МВт
Медвеженская ВЭС — 60 МВт
Берестовская ВЭС — 60 МВт