«Атомэнергомаш»: вибрация станков на контроле
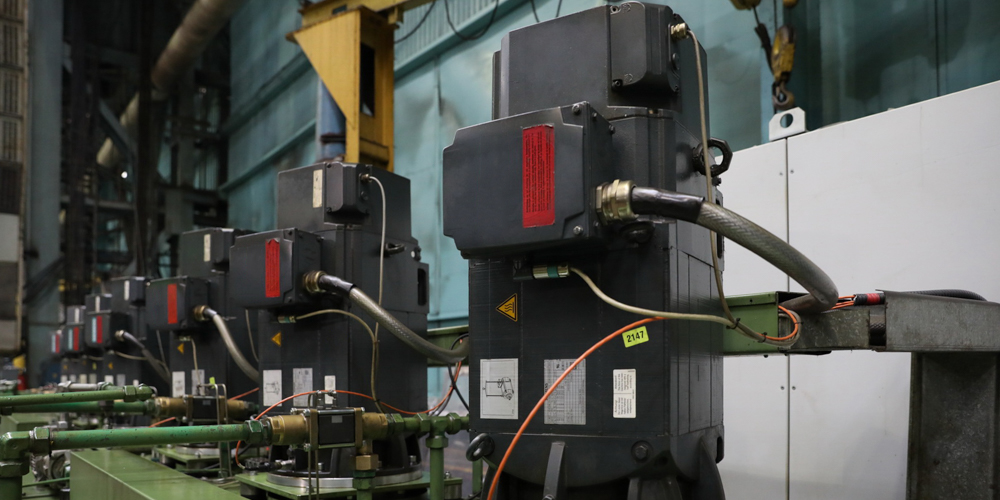
Машиностроительный дивизион подключает предиктивную аналитику к системе эксплуатации производственного оборудования, чтобы свести к минимуму внезапные поломки. Пилотный проект — комплексы вибродиагностики. В перспективе «Атомэнергомаш» оснастит ими не только станки, но и собственную продукцию.
Три года назад топ-менеджмент «Атомэнергомаша» решил проанализировать причины неплановых простоев оборудования, чтобы максимально сократить их количество и снизить риск срыва производственных планов. Опыта и интуиции рабочих не всегда достаточно, чтобы предвидеть поломку, — нужна системная предиктивная аналитика.
Протестировали предложения и крупных, с мировым именем, производителей, и небольших компаний, и в сентябре 2019 года одно из ключевых предприятий дивизиона «АЭМ-технологии» заключило договор на внедрение. Опытной площадкой выбрали волгодонский филиал «Атоммаш». На пять станков механической обработки установили системы вибромониторинга. Вдобавок «Атомэнергомаш» заказал два мобильных комплекса — для вибродиагностики станков малого механического парка и кранового оборудования.
Как это работает
Вибрация — наиболее показательный параметр работы основных узлов оборудования, помогающий определить, есть ли нарушения и насколько они критичны. На станок крепят датчики (до 28 штук в зависимости от его типа) амплитуды виброперемещения, виброскорости, виброускорения и т. д. Датчики снимают параметры вибрации в разных режимах. Информация тут же выводится на монитор. Оператор отслеживает, как вибронагруженность изменяется во времени. Аппаратура откалибрована под три зоны: рабочую, зону внимания и зону опасности.
Статистика формирует «вибропаспорт» оборудования. Динамику отклонений можно соотнести с возникновением дефекта и запланировать своевременный ремонт, не дожидаясь критических изменений в узлах.
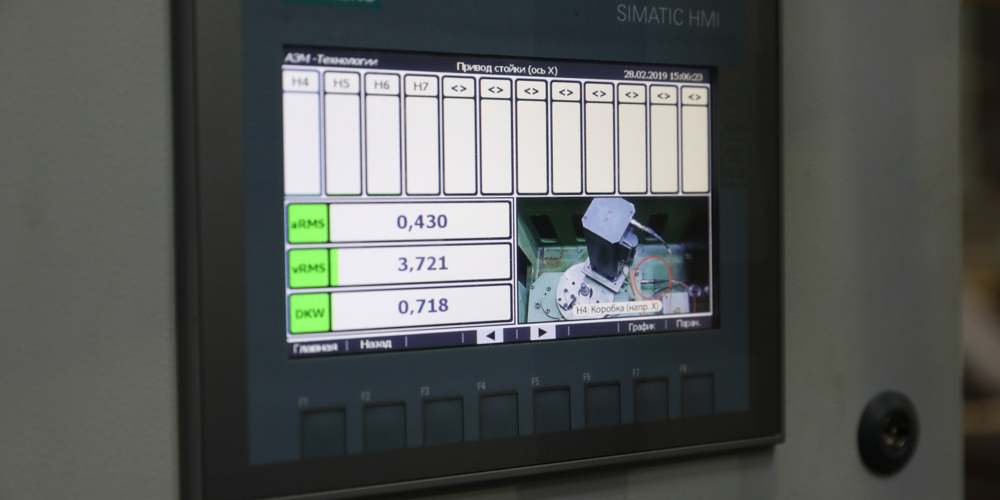
«Мы недолго эксплуатируем систему, и статистики еще не так много, как хотелось бы. Больших дефектов и выхода из строя оборудования не было, — рассказал директор департамента информационных технологий «Атомэнергомаша» Роман Токаренко. — Но параметры явных отклонений уже зафиксированы. На основании этих данных специалисты сегодня понимают, какие узлы нужно ремонтировать, не дожидаясь планово-предупредительного ремонта». Это стратегия «ремонт по состоянию».
Результаты мониторинга могут использоваться для корректировки графика ППР. Кроме того, если оператор станка увидит, что показатели вибронагруженности превысили допустимые, он изменит скорость движения резца, частоту вращения шпинделя — естественно, все в рамках технологии изготовления. Благодаря своевременно поступающим точным данным у оператора появились понятные, численно выраженные основания для изменения технологического режима. Данные об изменении, в свою очередь, могут учитывать технологи и конструкторы: если это происходило неоднократно, значит, надо пересмотреть технологическую карту и скорректировать плановые режимы работы либо использовать деталь из более прочного металла — или даже пересмотреть конструкцию узла.
Масштабирование и связи
В планах — развернуть вибромониторинг оборудования на станках «Петрозаводскмаша», а потом и на других предприятиях. АЭМ работает с университетами и компаниями над развитием системы вибромониторинга с российскими технологиями и комплектующими.
«Атомэнергомаш» также рассматривает возможность объединить систему вибромониторинга с системой мониторинга производственного оборудования (СМПО). Это отечественный программно-аппаратный комплекс, который фиксирует и накапливает информацию об эксплуатации ключевого технологического оборудования и причинах простоя — не пришла вовремя заготовка, сломался инструмент и т. д.
СМПО позволяет оценить загруженность каждого станка и сравнить ее с загруженностью остальных станков на одном предприятии и на нескольких. «Если зафиксировано снижение загрузки оборудования в течение какого-то периода, начинаем разбираться в причинах. Появляется база для углубления цифровизации производства и аккумулирования аналитики по производственному циклу. Мы сможем строить предиктивные модели выполнения плана», — поясняет Роман Токаренко.
За счет более эффективного использования оборудования, балансировки загрузки в «Атомэнергомаше» рассчитывают повысить производительность труда и сэкономить на покупке новых агрегатов. В крупнотоннажном машиностроении станок может стоить сотни миллионов рублей, а от подачи заявки на приобретение до запуска в работу проходит много месяцев. В целом по машиностроительному дивизиону планируется установка СМПО на 400 единиц оборудования.
Перекрестный мониторинг
«Атомэнергомашу» интересен опыт таких предприятий, как ВНИИА, у которого система мониторинга производственного оборудования совмещена с автоматической системой управления дискретным производством «Призма». Это собственная разработка ВНИИА.
Внедрять передовые цифровые решения и делиться опытом с другими предприятиями «Атомэнергомашу» поможет «Цифрум» (частное учреждение, входит в блок «Росатома» по цифровизации). Специалисты «Цифрума» также будут участвовать в разработке вариантов архитектуры системы, объединяющей вибромониторинг и СМПО, и готовить ее тиражирование в отрасли и за ее пределами.
Кроме того, «Атомэнергомаш» хочет обсудить со своими клиентами установку систем вибродиагностики на собственную продукцию, чтобы получать по закрытым каналам связи данные о работе оборудования АЭС. Что это даст? Ту же статистику — она покажет, нужны ли корректировки в конструкции оборудования, материалах. А заказчику можно будет предложить дополнительные услуги — например продленную гарантию.